Bottomhole Pressure Calculations
Estimating bottomhole pressure from measured wellhead pressure and temperature is an important task in petroleum engineering. Bottomhole pressures are required in most classical well-performance forecasting techniques such as rate-transient analysis (RTA), history matching using reservoir simulation, inflow-performance-relationship (IPR) estimation, and more.
Based on production data measured at the surface (i.e. surface rates, wellhead pressure, and wellhead temperature), and key properties describing the wellbore (i.e. a deviation survey describing the curvilinear shape of the well, wellbore diameter, and pipe roughness), we can estimate the bottomhole pressure by numerical integration of the pressure- and temperature gradient expression.
Multiphase flow in inclined pipe involves calculations of oil, gas, and water which require an accurate fluid description (PVT). We achieve this by leveraging all the relevant capabilities of whitson+ seamlessly to provide accurate and consistent phase behavior in all calculations made on a particular well.
Currently Supported Correlations:
- Hagedorn and Brown (Liquid-Rich Wells)
- Beggs and Brill (Liquid-Rich Wells)
- Gray (Low-LGR Gas Wells)
- Woldesemayat and Ghajar (Liquid-Rich Wells)
1. Input
1.1. Production data
Daily production rates can be provided at stock-tank conditions or at separator conditions. If separator rates are provided, then the Common Process Conversion module can be used to generate stock-tank rates for the BHP calculations. In addition to production rates, one must also provide casinghead pressure and tubinghead pressure if a tubing is installed. If the well is subjected to either gas-lift or rod-pump assisted lift, lift-gas rates or liquid level in the annulus must be provided, respectively.
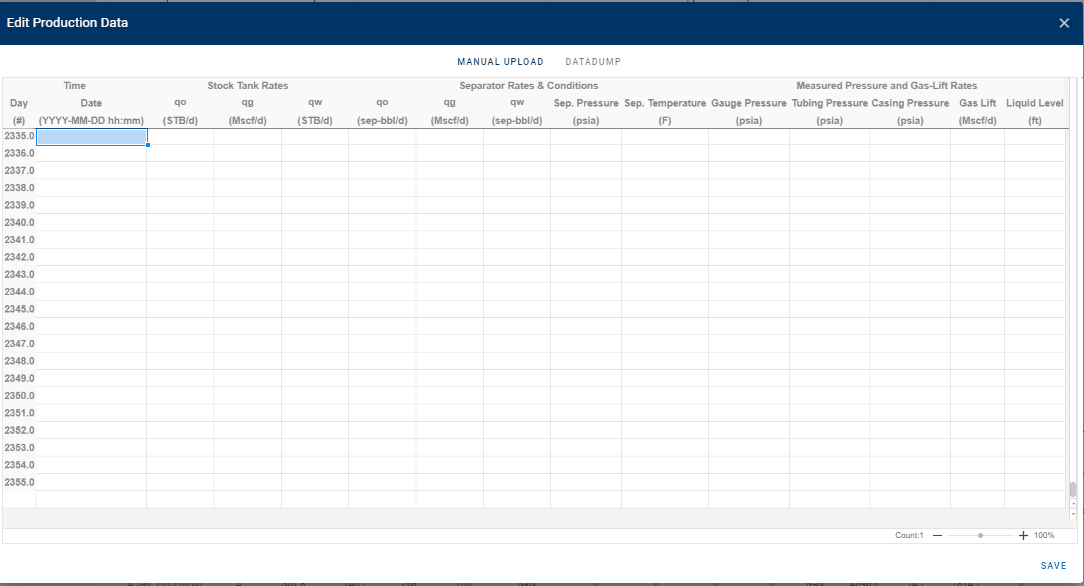
1.2. Well deviation survey
The well deviation survey describes the trajectory of the wellbore, and consists of a measured depth (MD) and calculated true vertical depth (TVD). The user can provide the full deviation survey of the well as the BHP module will sample the deviation survey backend to create the wellbore grid for BHP calculations. The perforated interval must be specified by providing the MD of the top and bottom perforations. The top perforation is also the reference depth at which the BHP is calculated.
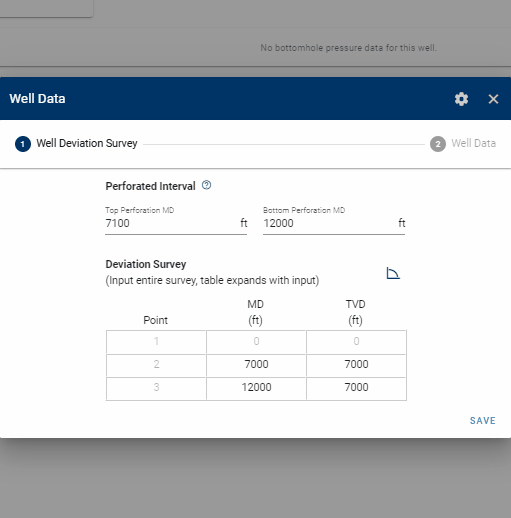
1.3. Well data
1.3.1. Casing and Tubing Data
The well data consist of properties for the tubing and casing string(s) relevant for pipe flow calculations, (i.e. the depths of the different pipes, their diameters, and roughnesses). Multiple tubing and casing strings can be specified, where an API tubing- and casing table is available to simplify the input of the pipe data.
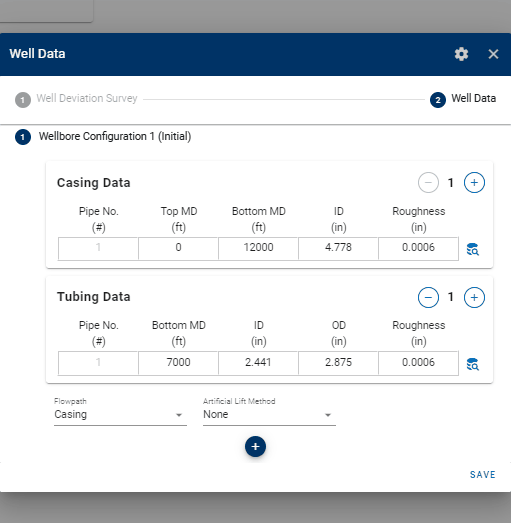
1.3.2. Multiple Wellbore Configurations
Multiple completion data sets wellbore configurations can be specified, where a date must be set to tell the BHP module from which date in the production time series each completion is used.
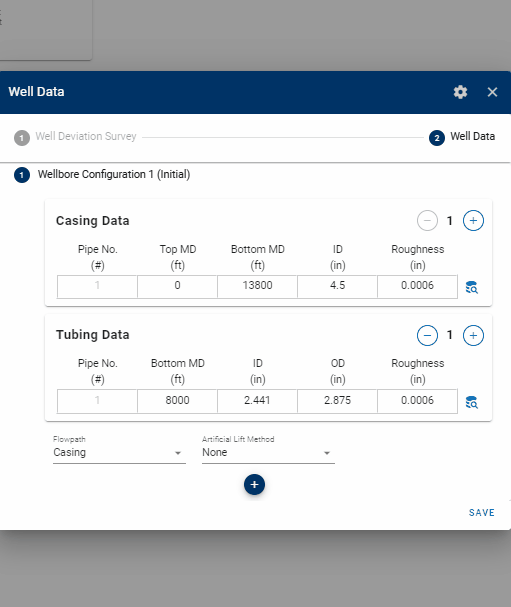
You can easily set the date for the new wellbore configuration graphically by clicking on the symbol adjacent to the date input field, as demonstrated in the .gif below. Then, simply align the vertical dashed line to the desired point in time when your new wellbore configuration should take effect.
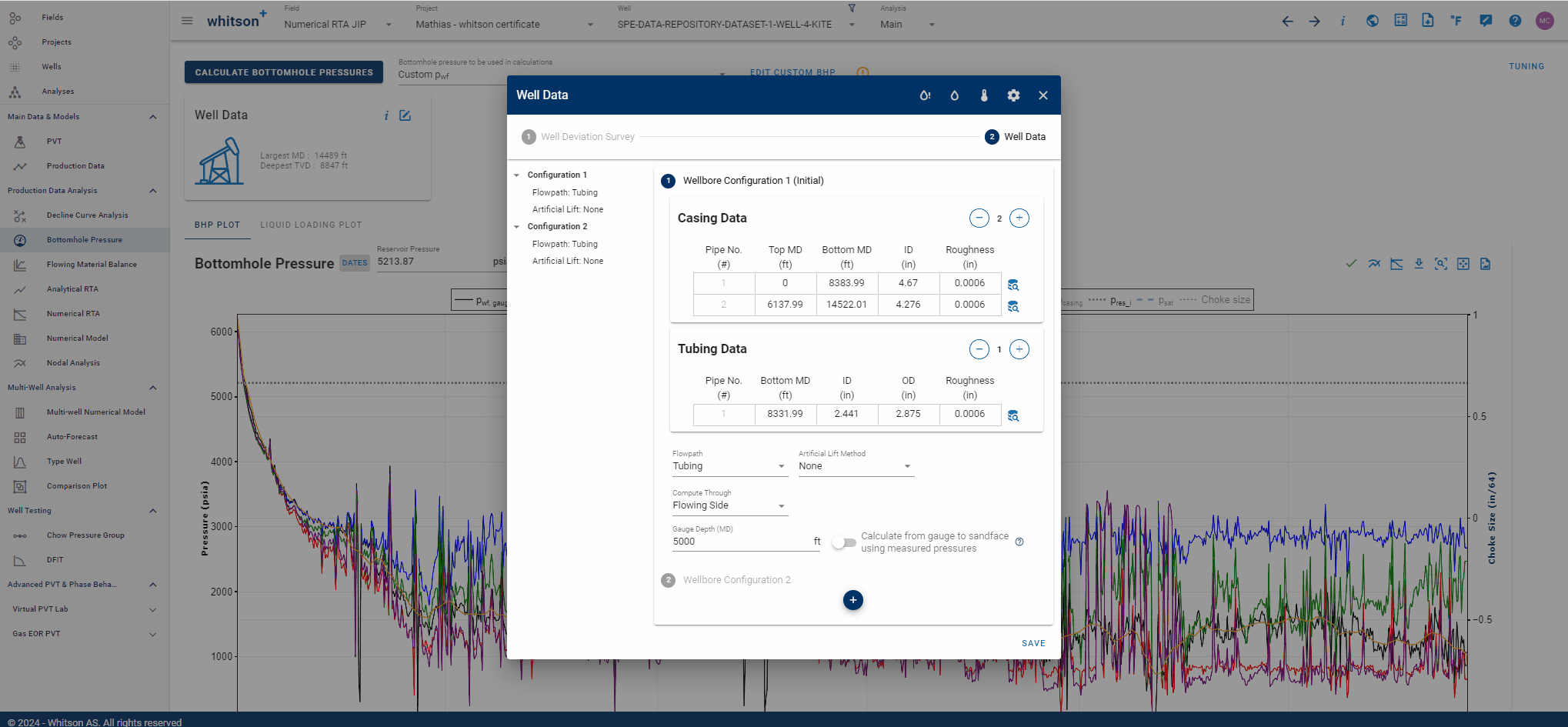
1.3.3. Flow Paths
The user must also specify the flow path of the well stream for each wellbore configuration. The flow path can be:
- Tubing—well stream flows through a tubing string.
- Casing—well stream flows through the production casing.
- Annulus—well stream flows in the annular space between the tubing and production casing.
- Tubing & Annulus—well stream flows both through the tubing string and the annular space between the tubing and production casing. See the section on dual conduit flow for further details.
- Measured BHP—If pressures from a downhole gauge have been provided under the Gauge Pressure column in production data, one can instruct the BHP model to echo the measured BHP (applies to wells for which an accurate estimate of the BHP is available, and where the user wants to include that pressure in the resulting BHP profile for completeness).
- Unknown—Automatic selection of flow path depending on the casinghead pressure, tubinghead pressure, and associated well configuration. The following table summarizes the logic applied for the unknown flow path.
Condition | Selected Flow Path |
---|---|
> and Tubing is Installed | Tubing |
≤ and Tubing is Installed | Annulus |
Tubing is not Installed | Casing |
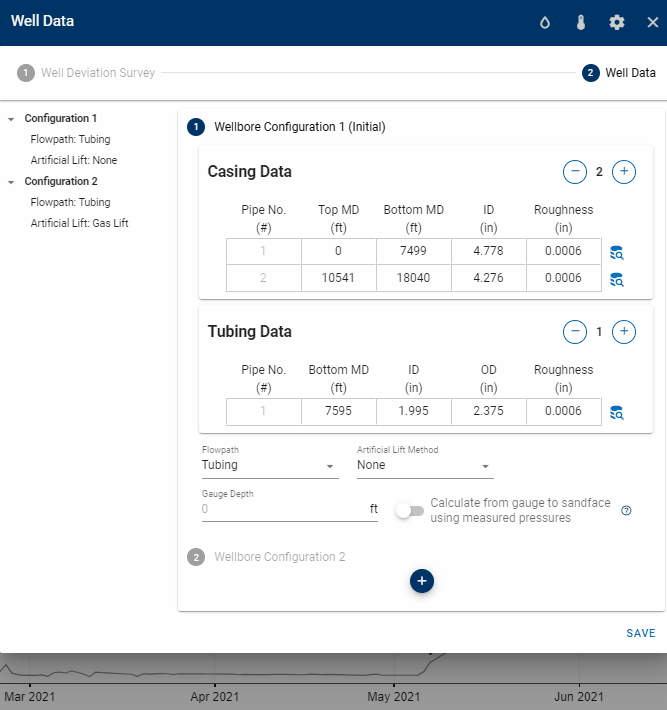
1.3.4. Static (Quiet) Side
The user may select which side of the tubing the bottomhole-pressure calculation should follow. Using the static (quiet) side of the tubing assumes that there is a single-phase gas column with communication to the flowing side at the EOT (i.e., no isolating packer).
The static-side calculation is well suited for gas-lift assisted wells where it is certain that the static side is filled with gas at least down to the gas-lift valve. The figures below explain how the static-side calculation works for a naturally flowing well, and a gas-lift assisted well. The flow path in this case is set to "tubing", but the static-side calculation also works when the flow path is set to "annulus", with everything being reversed compared to the figures below.
For gas-lift assisted wells where the gas-lift configuration is set to "valves" or "automatic", it is also possible to select whether to do the static-side calculation down to the gas-lift valve or to the end of the tubing.
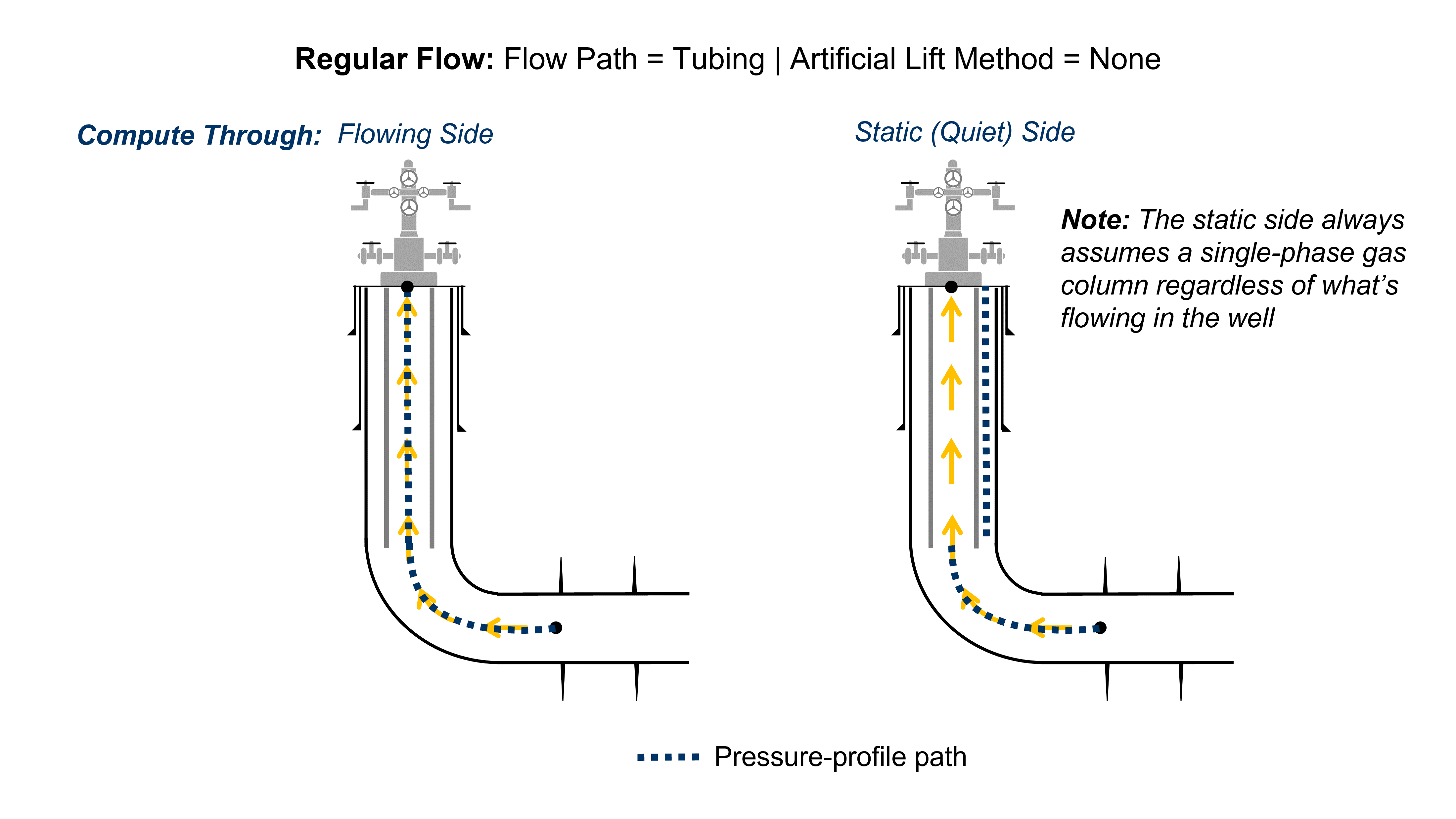
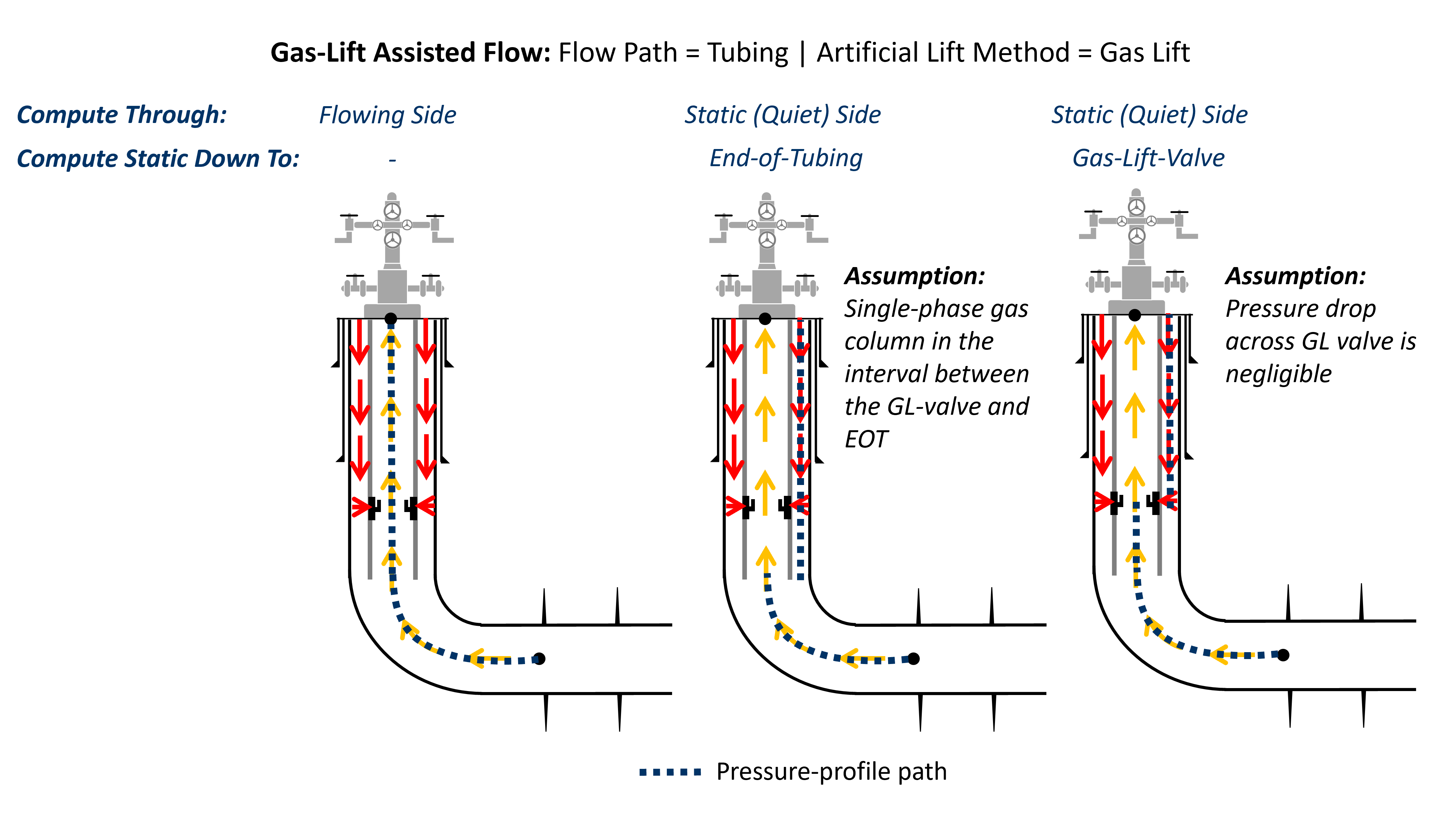
1.3.5. Convert from Gauge Pressure to Sandface
If the user has entered pressures for one or several rows in the Gauge Pressure column in production data, one can convert from this pressure and down to sandface. To do this, toggle on "Calculate from gauge to sandface using measured pressures".
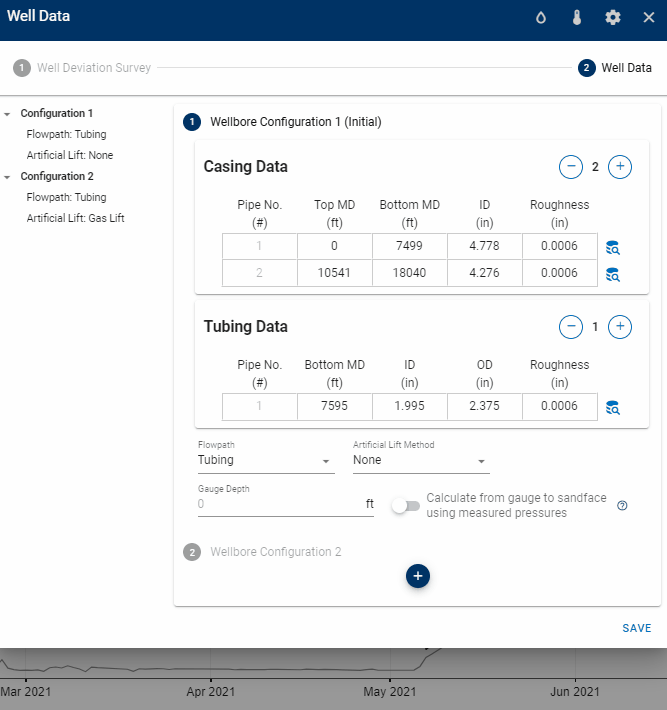
When the "Calculate from gauge to sandface using measured pressures" switch is activated, the behavior of the software is going to be dependent on whether a gauge depth is provided or not.
Condition | Software Behavior for BHP Calculation |
---|---|
If a gauge depth is provided | The software will correct the gauge pressure from that gauge depth to top perforation depth. |
If a gauge depth is not provided | The software will continue calculating the BHPs as if the switch was not activated. |
So basically, for the activation of the switch to be useful for your purposes, ensure that you have provided the gauge depth within the corresponding wellbore configuration.
1.4. Temperature Data
The temperature data require two inputs, the rock temperature at the surface (to create the linear temperature profile in the rock), and the average wellhead temperature for the production time series.
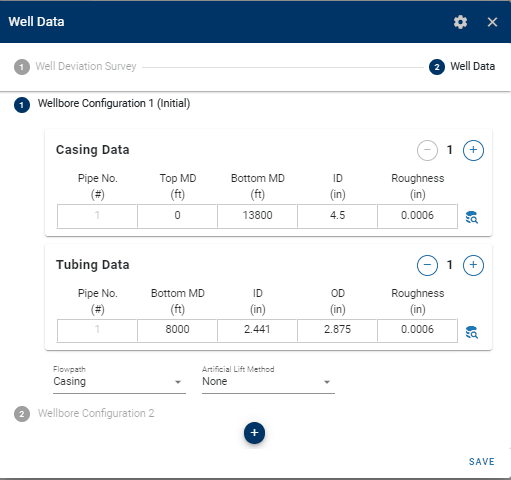
1.5. Water & Lift-gas Properties
This section allows you to customize the properties of water and injected lift gas used in well calculations.
-
Lift-gas PVT:
By default, the Lift-Gas PVT option is set to Surface Gas SG, which automatically uses the specific gravity of the produced gas to represent the gas being injected for lift. This is a common assumption when the lift gas is recycled from the same well. Alternatively, selecting Specified SG allows you to manually input a different gas specific gravity if the lift gas comes from a different source. -
Water PVT:
You can also adjust the water salinity and water specific gravity. Editing one will automatically update the other, ensuring consistency in the water PVT properties used throughout your modeling. These settings directly affect the water density and viscosity and are calculated automatically.
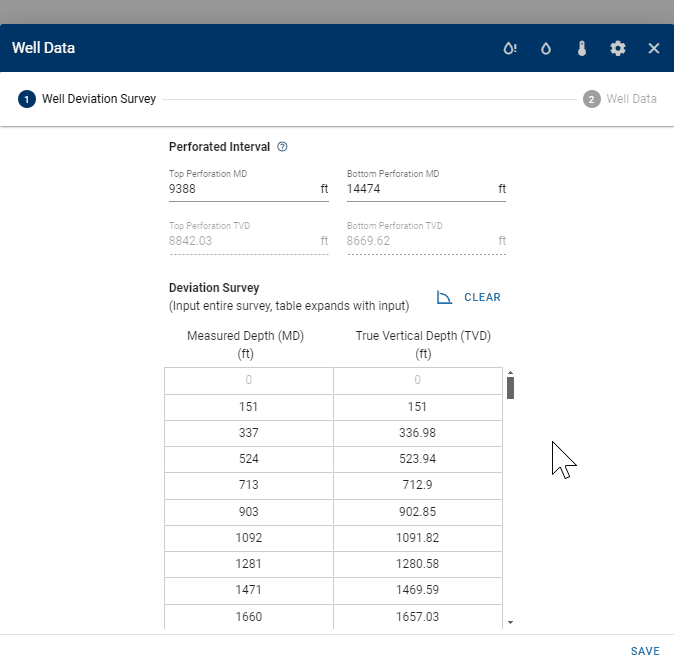
1.6. Artificial-Lift Data
The BHP can be calculated while the well is on gas-lift, rod pump, plunger lift, or ESP.
Artificial Lift Method | Activation Condition for a Given Day |
---|---|
Gas Lift | The active wellbore configuration for that day has gas lift as the artificial lift method, AND \(q_{g,\text{gas lift}}\) in the production data is greater than zero. |
Rod Pump | The active wellbore configuration for that day has rod pump as the artificial lift method, AND the "Liquid Level" in the production data is greater than zero. |
Plunger Lift | The active wellbore configuration for that day has plunger lift as the artificial lift method, AND the "Liquid Level" in the production data is greater than zero. |
ESP (Electric Submersible Pump) | Can only be activated if downhole pressures are measured at the inlet of the ESP with a pressure gauge. If this option is selected, the user can provide the depth of the pressure gauge and correct the pressures from measurement point down to sandface. |
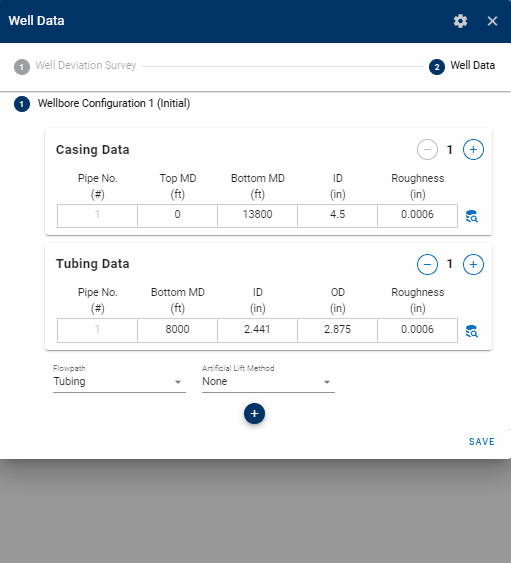
2. Output
2.1. Output Curves
The output data for the BHP module is the calculated bottomhole pressure, at the top perforation depth, for every entry in the production time series. The user can choose whether to use the noisy data resulting from raw production data, or to apply a smoothing of the data. Furthermore, the user can select which BHP data set to use in other features of whitson+ that rely on bottomhole pressures. This ensures consistency in all calculations across the platform.
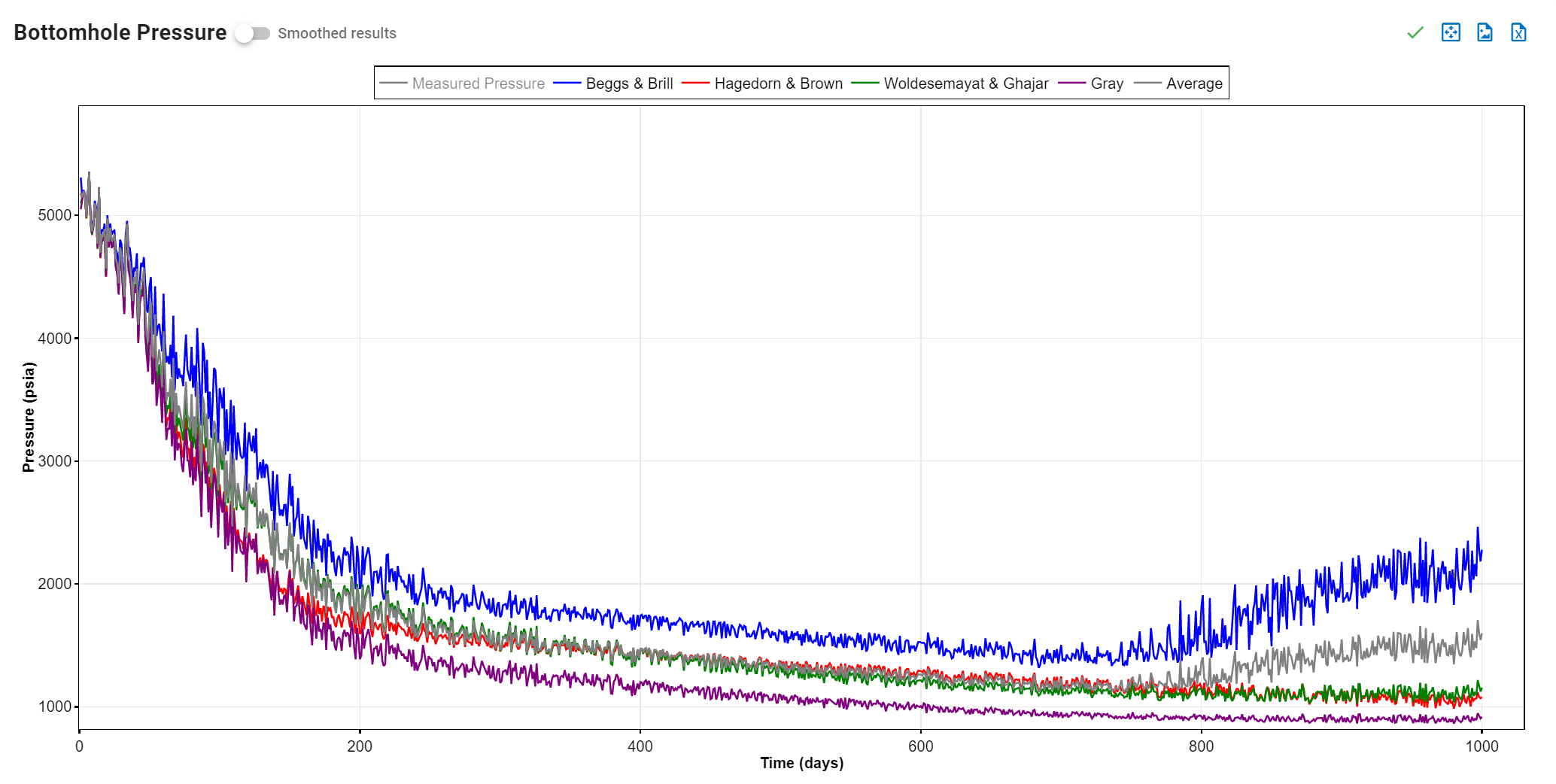
2.2. Custom BHP
Calculated bottomhole pressures are generally noisy due to oscillations in surface rates and pressures. This noise can significantly impact analysis, especially in RTA or numerical modeling when the well is controlled by bottomhole pressure. The Custom BHP feature allows users to smooth and piecewise-linearize the calculated bottomhole pressures. Users can define the sampling frequency, manually add or remove points to shape the desired BHP curve, and toggle an option to ignore zero-pressure values during the calculation. Additionally, an autofit line can be generated to assist with quickly establishing a baseline BHP profile.
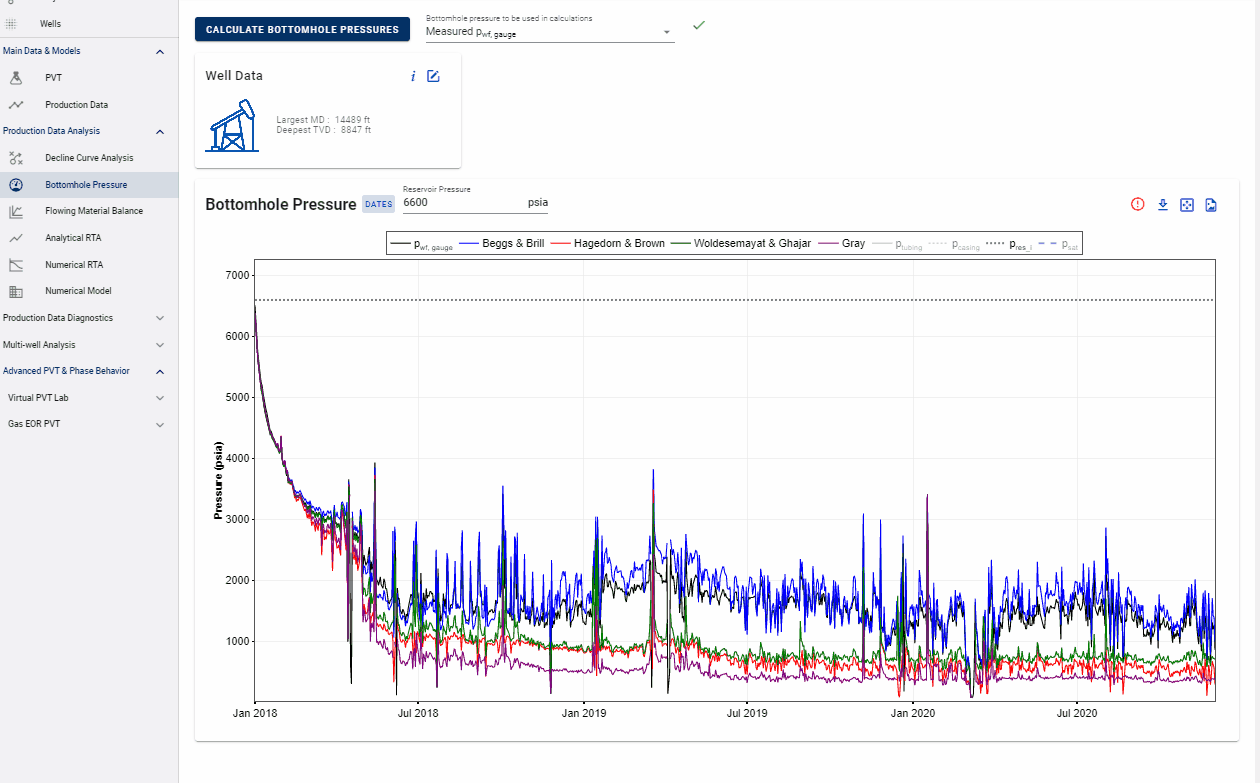
2.3. BHP Calculation Stuck?
When the computation takes longer than expected, the user can try to force re-running the calculation as follows:
- Open Well Data card.
- Click Calculation Options.
- Click refresh icon to Force Run BHP Calculation.
- All steps are shown in the .gif below.
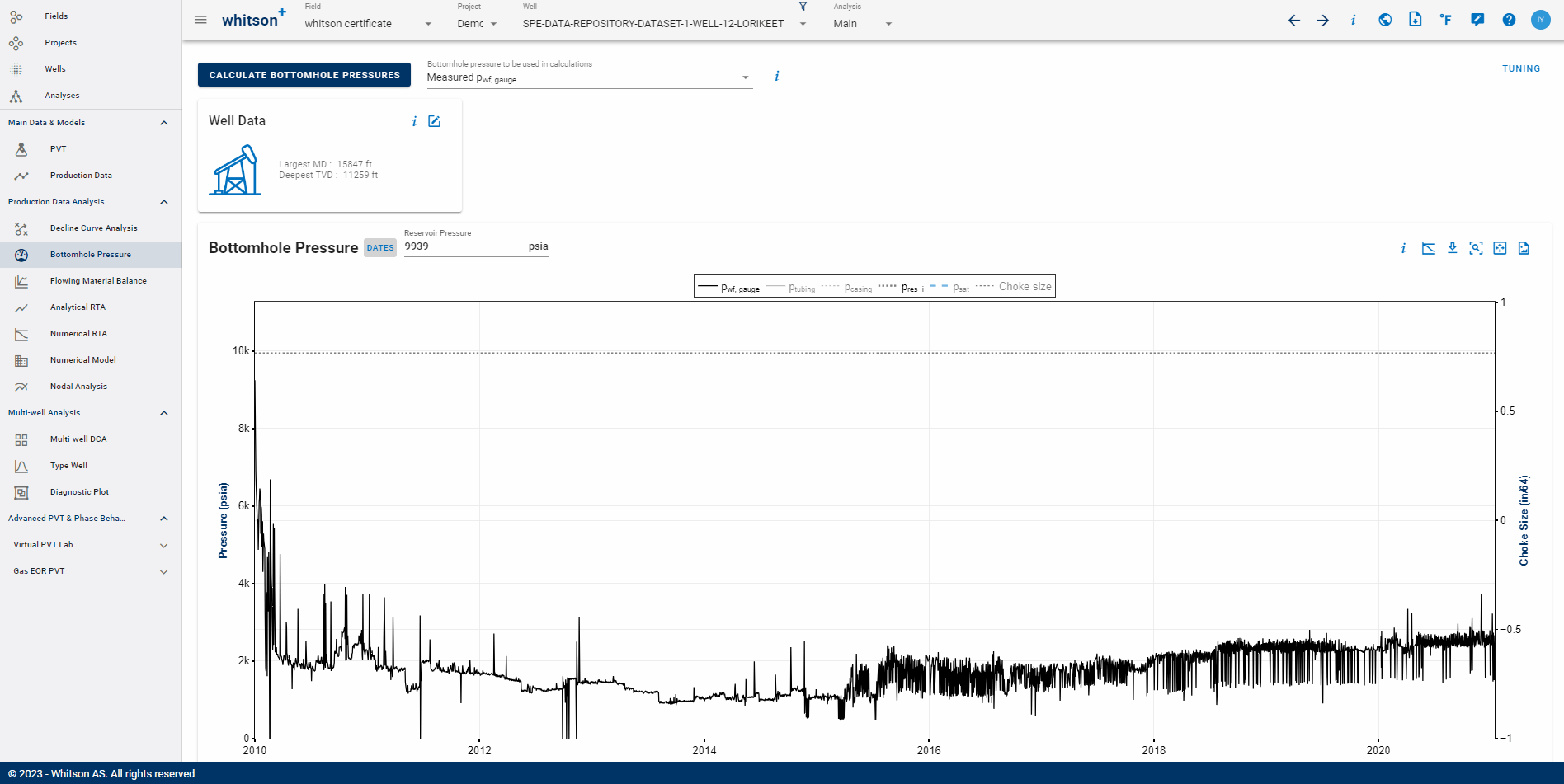
If the problem persists, please contact support@whitson.com
2.4. BHP Plot Options
2.4.1. Show Rates, Surface Pressures
On the BHP Plot tab, you can plot the rates, as well as the surface pressures, alongside the bottomhole pressure calculation results.
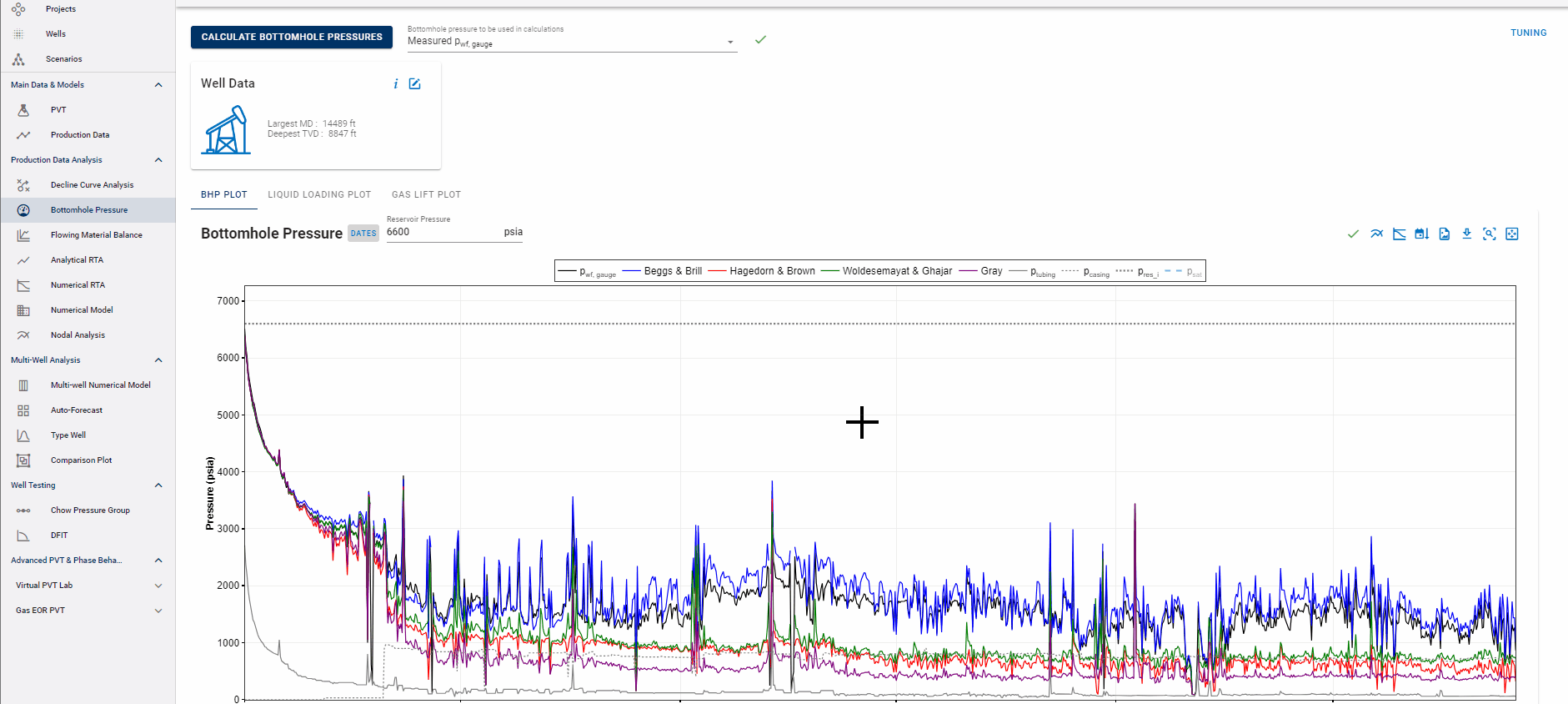
2.4.2. Show Wellbore Configuration Dates
On the BHP Plot tab, you can visually examine how the wellbore configuration changes alongside the bottomhole pressure calculation results.
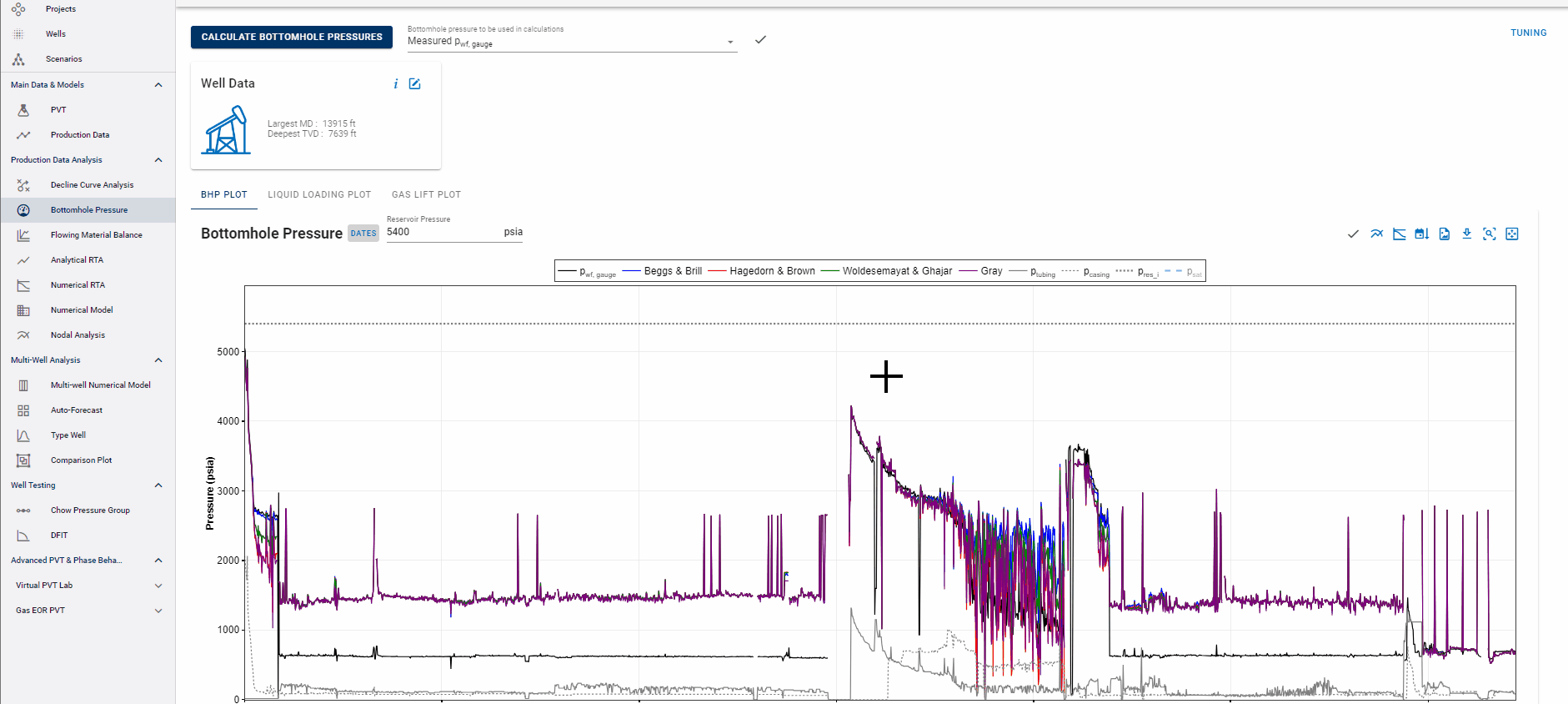
2.4.3. Show Liquid Loading
On the Liquid Loading Plot tab, you can compare your actual gas rates to the required critical gas rates to deliver gas through the current wellbore configuration without any liquid loading issues.
The critical rate is computed at the end of tubing using the Turner correlation by default. You can always change the correlation to use and the depth at which these critical rates are reported for.
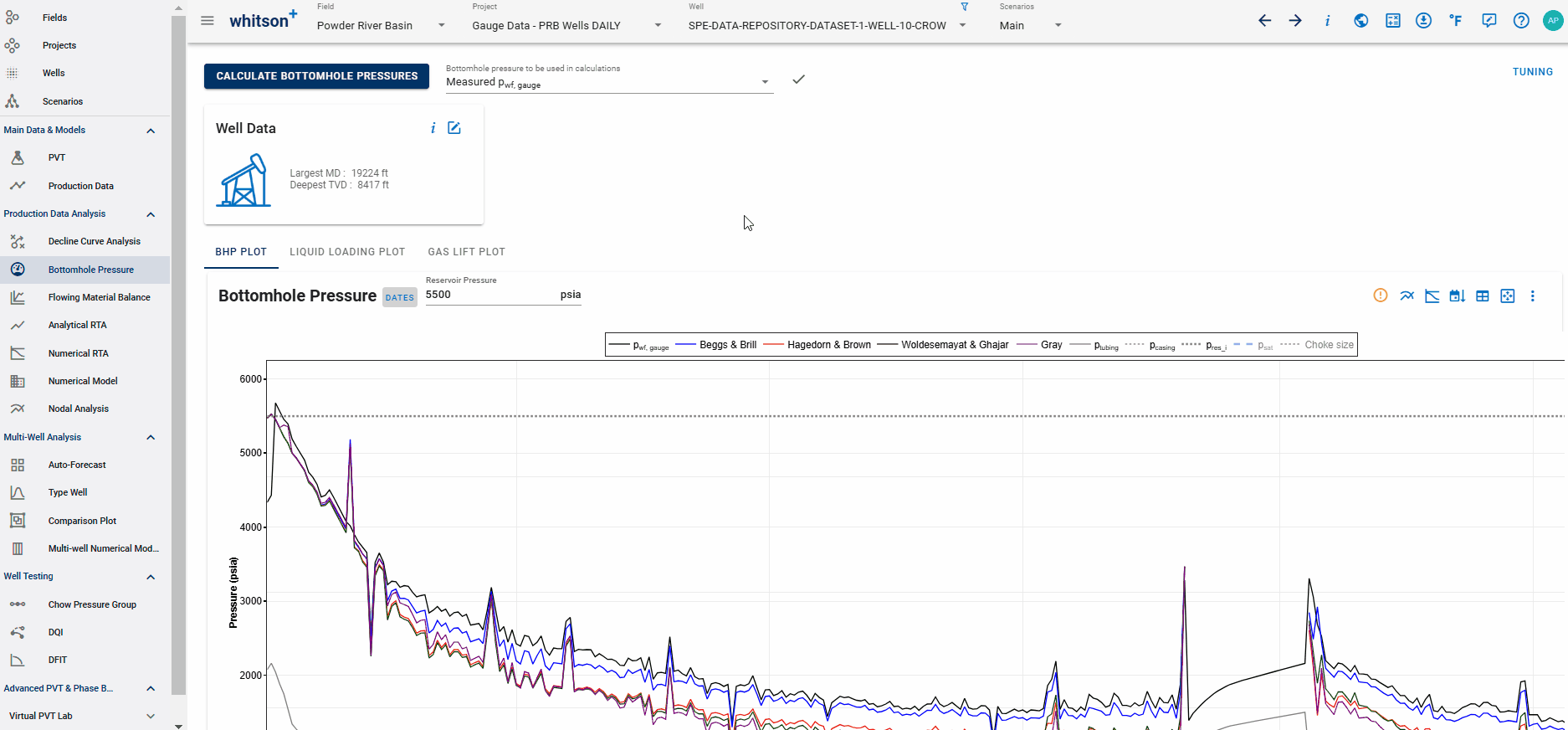
2.4.4. Show Gas Lift Injection Depth
On the Gas Lift Plot tab, you can see the depth of the valve at which the gas was injected and compare it with the casing, tubing pressure and the gas lift gas rate.
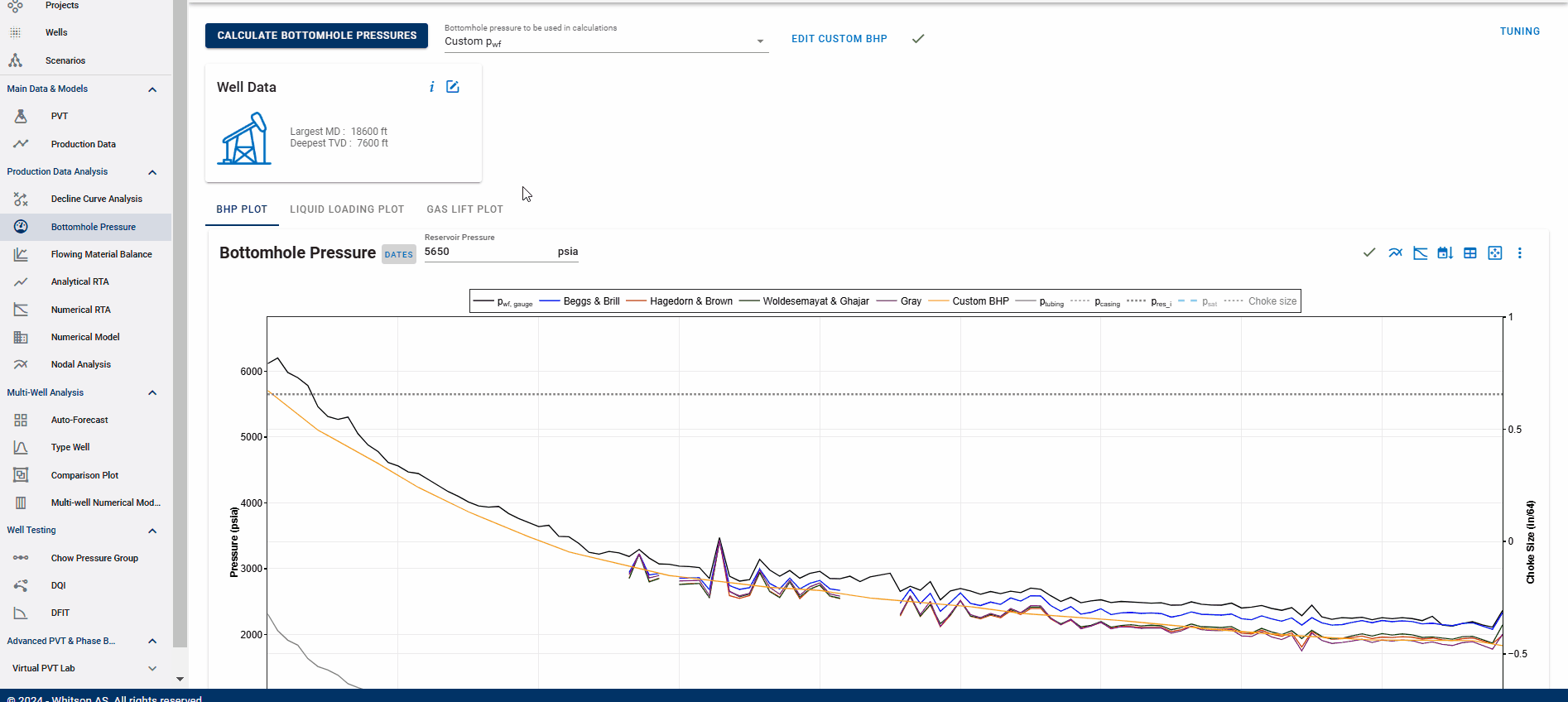
3. Technical Features
3.1. Governing Equations
The main equations used for multiphase flow in inclined pipe are provided here. Our wiki contains a detailed review of the relevant multiphase-flow theory and the commonly used correlations for pipe flow.
3.2. Artificial-Lift Methods
3.2.1. Gas Lift
Gas lift is included as a step change in mass flow at the injection valve. We assume the lift gas to completely mix with the flowing mixture, resulting in a step change in the gas rate, and consequently the producing GOR.
When the well is on gas lift, are gas rates netted or gross (including gas lift rates)?
The inputted gas rates in the production data editor are assumed to be netted out
The reason we do this is because the gas rate is used everywhere in the system, including numerical model, flowing material balance and RTA; and there the gas lift is not part of the calculation (i.e. not part of the reservoir flow).
In the BHP calculations, to get the total gas that is flowing inside the wellbore, we just do the calculation in the background as follows:
Three options exist for the gas-lift configuration:
1. Poorboy: The term "poorboy" refers to the situation when injection occurs at the EOT.
2. Valves: A single valve at a specified depth, or a set of valves at different depths along the tubing, can be provided. If a full set of valves is provided, the casinghead pressure is used to decide which valve the lift-gas enters the tubing through. We assume all of the lift gas to enter the tubing through the first open valve it encounters, even though this rate might exceed the maximum rate predicted by the Thornhill-Craver equation.
Gas Lift Valve Ordering and Behavior
The gas lift valves are ordered by descending measured depth with valve number. The deepest valve, is valve number 1, the second deepest is valve number 2, and so on. If "Last Valve Always Open" is ticked, then PSC and PSO for valve 1 (if specified) will be disregarded by the calculator.
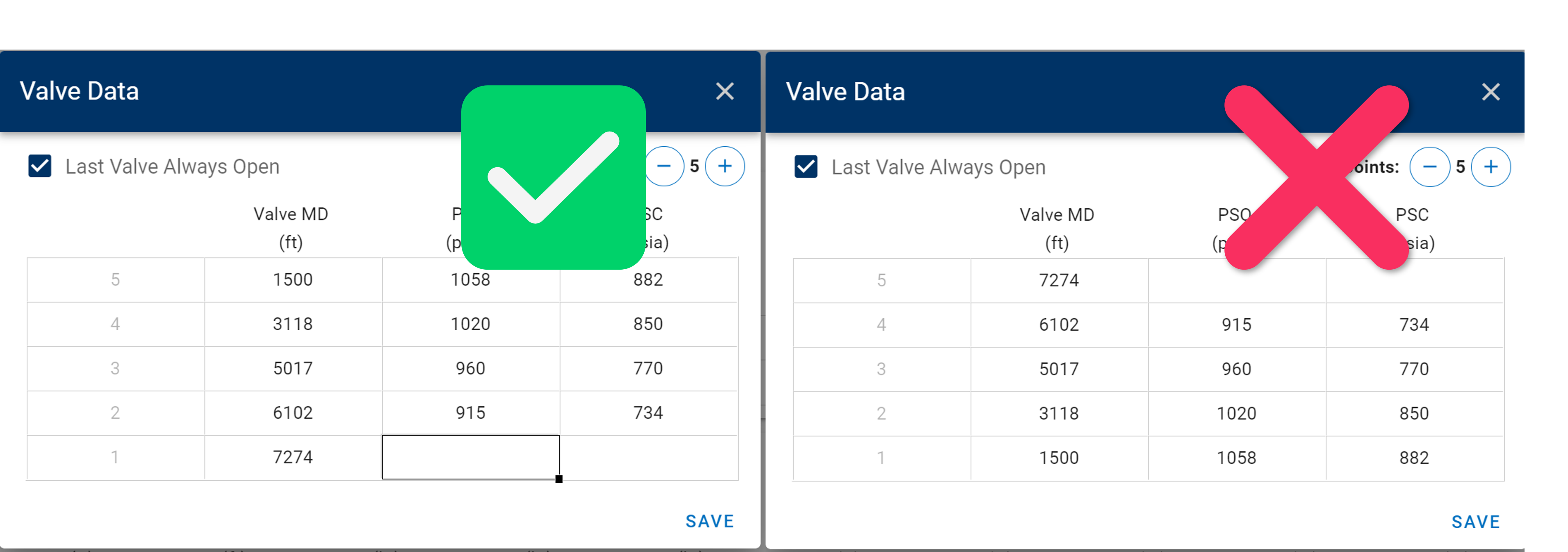
3. Automatic: If the lift-gas injection depth is unknown, then the BHP calculator can estimate the depth by computing the pressure profiles in the tubing and annulus and finding the depth at which they are equal. If this depth is computed deeper than the EOT depth, then EOT depth is used (poorboy).
If the flow path for a given day is set to "Annulus", a reversed gas-lift configuration is applied where the point of injection is set to be at the deepest valve if there is only a single valve depth specified or "Last Valve Always Open" is ticked for a set of valves. If not, the lift-gas is injected at the EOT.
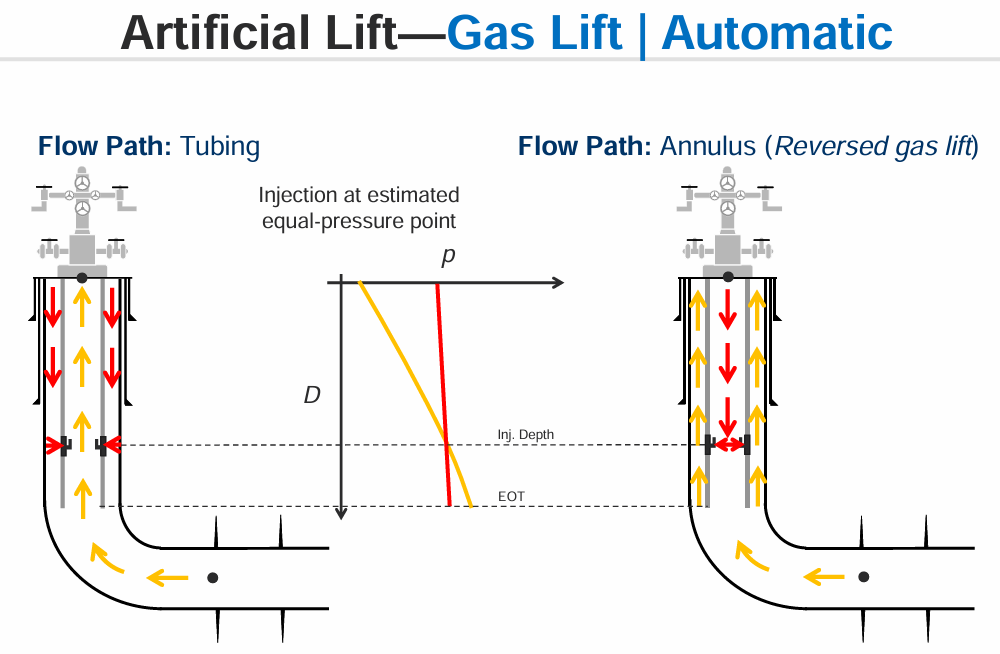
Which gas lift configuration to choose for a given well?
Is there a packer in the well? If so, it is likely that the gas lift configuration uses valves, meaning that the injected gas enters through valves in the tubing. In this case the depth of the valve(s) that allow gas to flow from annulus to tubing (or viceversa) is a required input.
If packers are in the hole, but the valve depth is unknown, then picking the “Automatic” gas lift configuration is the best choice, then the BHP calculator can estimate the depth by computing the pressure profiles in the tubing and annulus and finding the depth at which they are equal (that would be the injection depth). One important consideration is that using "Automatic" gas lift configuration in this case might lead to the injection happening at end of tubing (EOT), which would not be consistent with having a packer in the hole, but this will only occur if the depth is computed to be deeper than EOT based on the input data.
If there is no packer installed in the hole, there is communication between annulus and tubing through the end-of-tubing (EOT) and therefore the appropriate gas lift configuration is “Poor-boy”.
Differences in Gas Lift Configurations
-
Gas Lift configuration "Valves" are assumed to open in the direction Annulus → Tubing (conventional logic).
- This means that when lift gas is injected into the annulus (i.e., flowpath = Tubing), the gas will enter the first valve that opens based on the casinghead pressure (CHP).
-
If lift gas is instead injected into the tubing (i.e., flowpath = Annulus), the gas will typically travel down to the end of tubing (EOT) and enter the well stream directly—this setup is referred to as a "poorboy" configuration.
-
If the "Last Valve Always Open" option is checked, the gas can bypass the poorboy path and flow through the last valve, which is assumed to always be open. Gas lift valves are one-way valves, allowing flow only from annulus to tubing. The exception is the last (deepest) valve, which can be treated as a simple orifice (an open hole) if the "Last Valve Always Open" setting is enabled.
-
Gas Lift configuration "Reversed Valves" results in the opposite logic, with all valves opening in the direction Tubing → Annulus.
Flowpath | Gas Lift Configuration | Lift Gas is Injected Into | Lift Gas enters well stream at |
---|---|---|---|
Tubing | Poorboy | Annulus | EOT |
Annulus | Poorboy | Tubing | EOT |
Tubing | Valves | Annulus | First Open Valve |
Annulus | Valves | Tubing | Last Valve if "Last Valve Always Open", else EOT |
Tubing | Reversed Valves | Annulus | Last Valve if "Last Valve Always Open", else EOT |
Annulus | Reversed Valves | Tubing | First Open Valve |
When using "Unknown" flowpath, the Gas Lift Valve direction is important. This is because the same gas lift well configuration can be used while swapping the flow path between Tubing and Annulus by the maximum wellhead pressure between CHP and THP.
3.2.2. Rod Pump
BHP calculations with a rod pump are achieved by dividing the well into three parts:
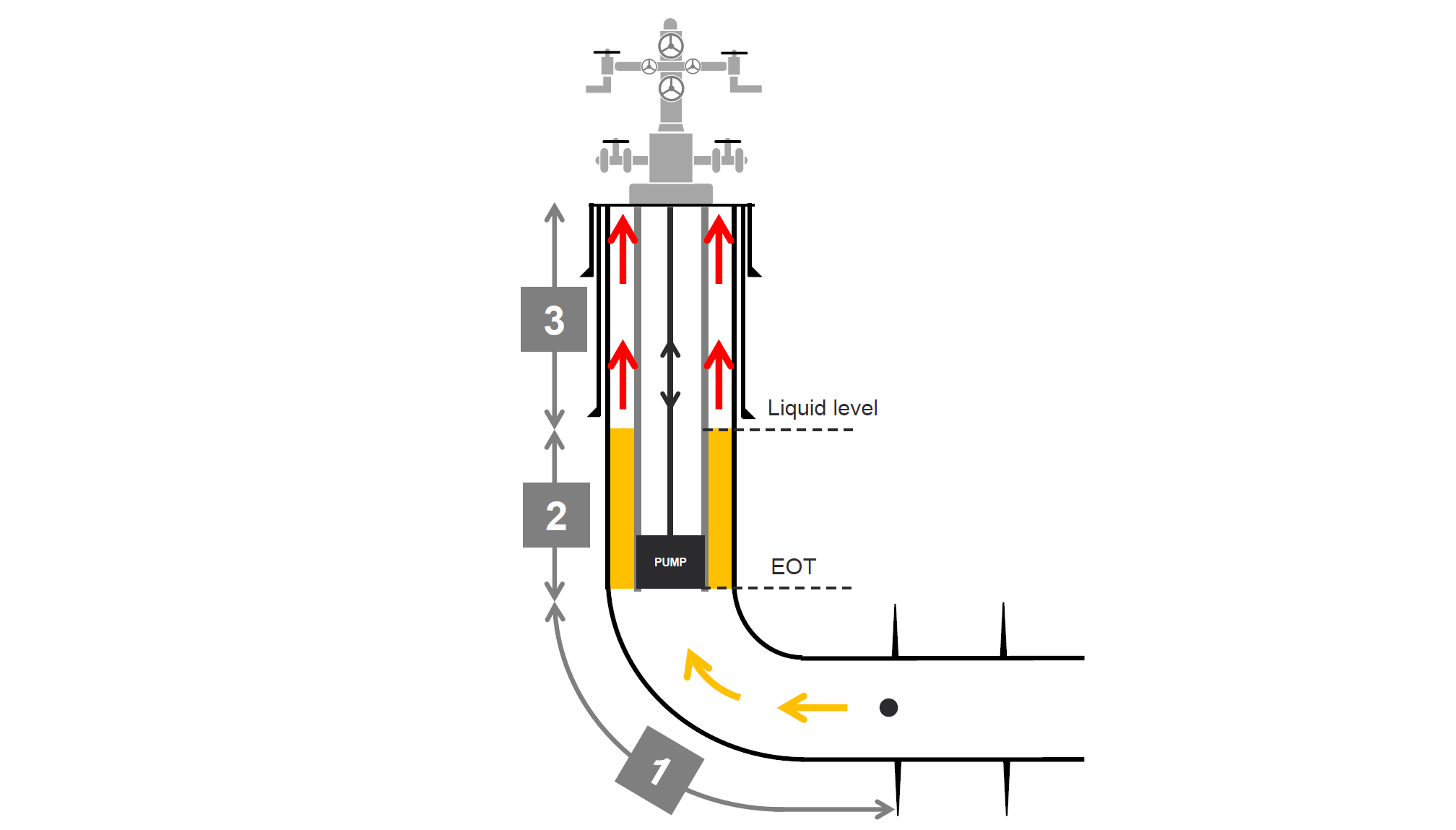
-
Top Perforation to Inlet of Pump (EOT)—Full well stream flowing in production casing, regular multiphase pipe flow.
- BHP is calculated using the correlation specified.
-
Inlet of Pump (EOT) to Liquid Level in Annulus—Static liquid column with gas bubbles percolating through it.
- This section does not use any correlation; instead, the logic is based on calculating the bubble velocity of a Taylor bubble and small bubble.
- The smaller velocity is assumed to be the slip velocity, which is then used to calculate HL. The liquid hold-up (HL) is limited to ≥ 0.7.
- An inclination correction is applied to the slip velocity.
-
Liquid Level in Annulus to Wellhead—Single-phase gas flow in the annulus. Gas percolating through the liquid column flows to the wellhead.
- This section is calculated as single-phase gas flow, meaning correlation selection has no impact.
Which part is affected by correlation selection?
The selected correlation affects the BHP calculation only in Section 1 (Top Perforation to EOT).
We assume the fluid split at the inlet of the pump to be such that all surface gas goes through the annulus, and all liquid goes through the pump and up the tubing. This is an approximation of the true split, and thus the estimated BHP may be somewhat larger than the true solution (less gas goes through the annulus in real life than what is modeled).
Most of the pressure drop for rod pump occurs in the second part, (i.e., the static column of fluid) as this is most-often along the vertical part of the well where the gravity pressure drop dominates. This fluid column will in most cases be liquid-like where the liquid is stagnant and the produced gas is percolating/rising through the liquid as bubbles. A new model to honor this liquid-like fluid column has been introduced to the rod-pump calculations, as the original model was overly sensitive to gas rate and consequently predicted too low pressure drop in the fluid column.
Why can't I select between flowing side or static (quiet) side when artifical lift is set to rod pump?
Casing pressures are always used as a pressure source for rod pumps, ignoring tubing pressures. Therefore, it is always a static (quiet) side calculation, and hence there is no option to choose between flowing and static (quiet) side.
The figure below show four flow regimes/modes for rod pump.
-
The flow regimes to the left represents the situation when the gas is not able to carry the liquid with it, causing a well-defined liquid level in the annulus. This model has been implemented, with a critical liquid hold-up set to 0.7.
-
The flow regimes on the right represents the situation when the gas is able to carry liquid with it. This is not implemented yet.
Unifying the left and right flow modes requires (1) a method of estimating the critical liquid hold-up (i.e., the transition between left and right models), and (2) a method of estimating the fraction of the total produced liquids that goes up the annulus. This is under development.
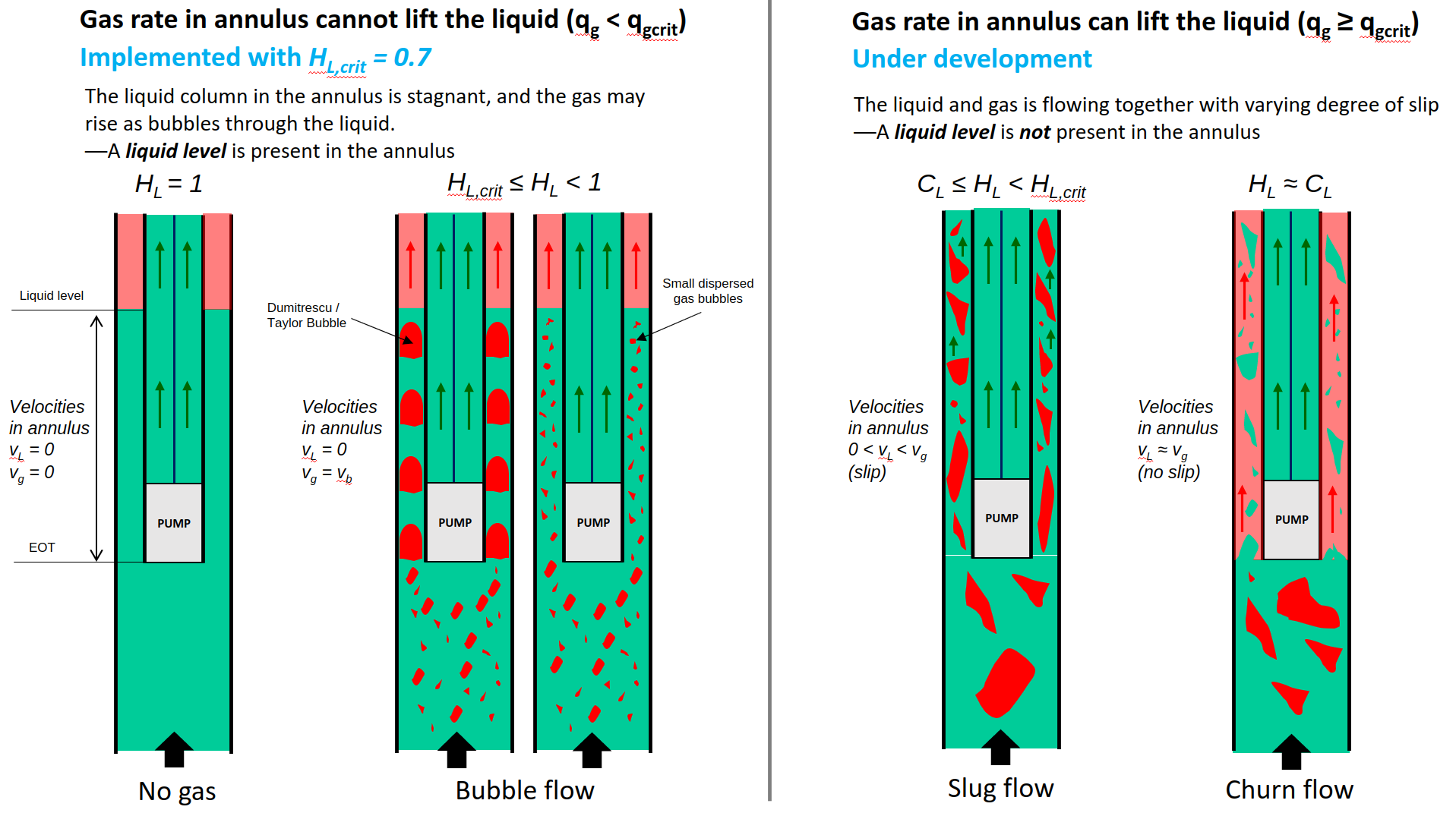
3.2.3. Plunger Lift
Plunger lift is a deliquification method used to remove liquids accumulated at the bottom of the well and improve production. It is often used to counteract liquid loading issues in gas wells. A schematic of a plunger lift system is shown in the figure below.
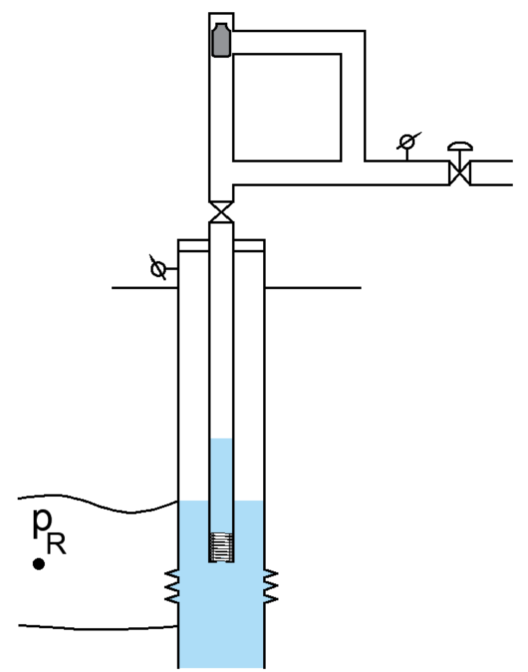
where, the gray component in the figure represents the plunger, which is essentially a cylindrical piston that travels up and down inside the tubing. The plunger's actuation is controlled by the opening and closing of the motorized valve at the surface.
- Upward travel: the piston lifts accumulated liquids from the bottom of the well, reducing flowing bottomhole pressure and improving production.
- Downward travel: when liquid accumulates again, the well is shut-in, allowing the piston to descend before the cycle repeats.
Plunger lift stages:
Stage 1, well shut-in. The well is shut in using the motorized valve, gas production at the surface and in the tubing is interrupted. Liquids slide down and accumulate at the bottom. The plunger drops and travels downward through tubing until it stops at a bumper spring at the bottom. The plunger typically moves at 5 m/s or less (e.g., when passing through the liquid), so, in a 2,000 m-long tubing, it takes approximately 6 minutes or more to reach the bottom. The bottomhole pressure (BHP) increases due to reservoir influx, while gas is stored in the annulus, preparing for the next lift cycle.
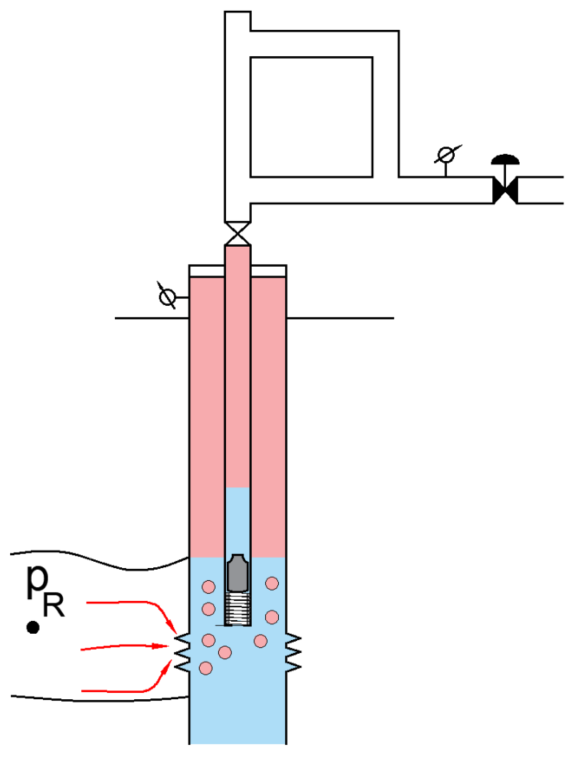
Stage 2, pressure build-up. The well is often kept shut-in for a long period (hours) to allow bottomhole pressure (BHP) to build up. This pressure increase enhances liquid displacement and ensures higher gas production rates when the well is reopened.
Stage 3, production start. When the motorized valve is opened, the plunger is pushed upward by the gas stored in the near-wellbore region and casing. The plunger velocity typically ranges from 5-10 m/s (starting faster at the beginning and slowing down as it nears the top). In a 2,000 m-long tubing, the plunger takes approximately 3-6 min to reach the surface. During this stage, gas above the liquid slug (pushed by the plunger) is produced, and some gas may bypass the plunger and liquid slug.

Stage 4, production. The plunger reaches the top and it is parked. The gas flowing behind it is redirected through a bypass line, which is often accompanied by a modest increase in gas flow rate, as the gas no longer needs to push the plunger and liquid slug. The gas now flows through an unobstructed pipe, and the wellbore is free of liquids, allowing for more efficient production.
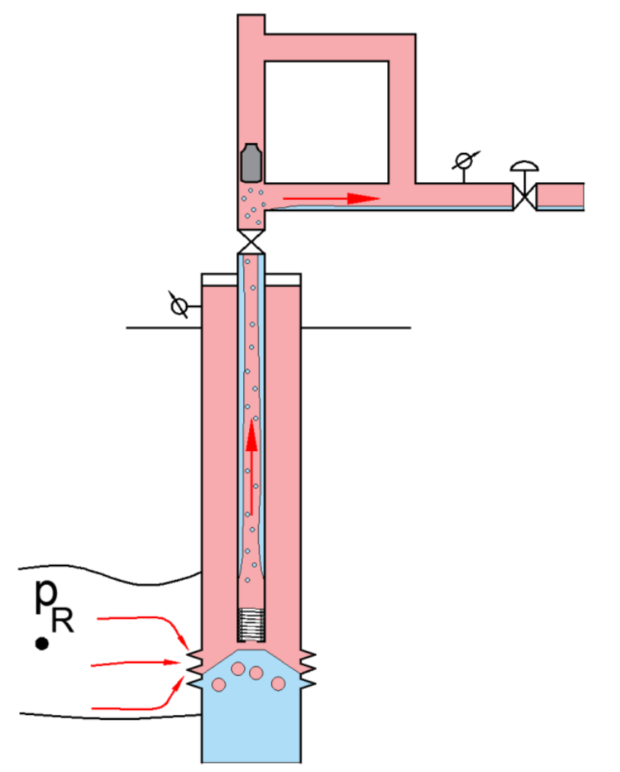
For the rest of stage 4, reservoir gas and liquid enter the wellbore. Most of the liquid remains behind, being accumulated at the bottom of the well. The duration of this stage is typically short (a few hours) since liquid fills the tubing quickly, but it depends on the liquid gas ratio of the well and size of tubing and casing.
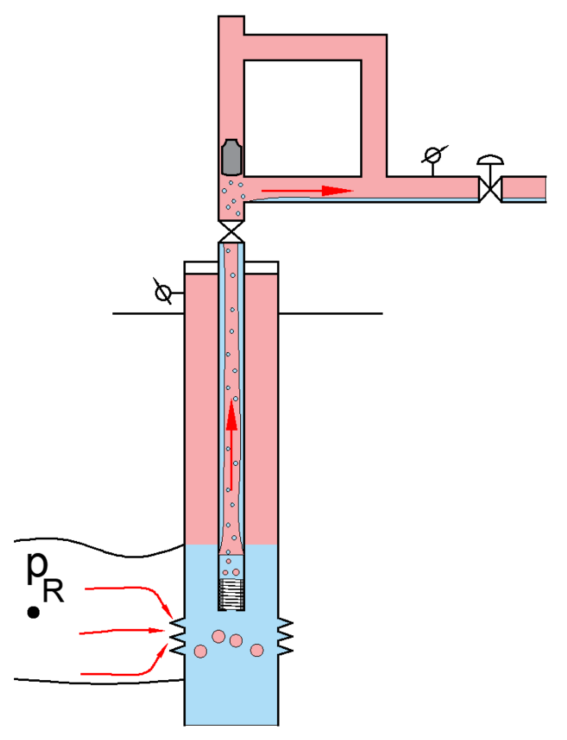
- The cycle is repeated (back to stage 1).
The figure below illustrates the evolution of key well parameters across the four plunger lift stages: gas rate (dark red dots), reservoir influx (bright red line), bottomhole pressure (blue line), and flowing bottomhole pressure (solid green).
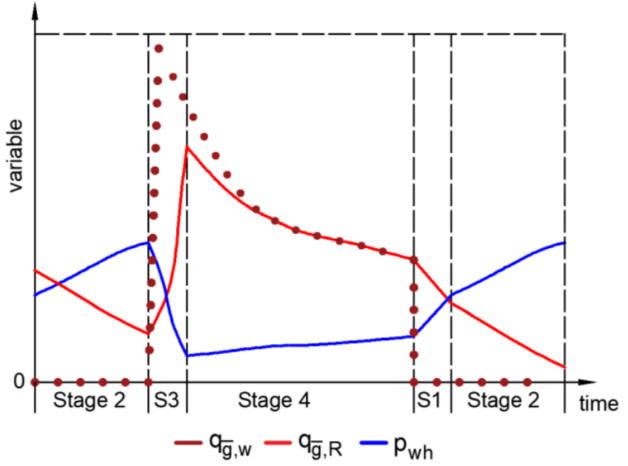
When a well is operating on plunger lift, the wellbore flow undergoes continuous short flow transients due to the cyclical nature of plunger lift process. Calculating bottomhole pressure under these conditions requires a small time-scale simulation of the transient process and such detailed simulations are beyond typical scope of what we normally do for practical petroleum engineering applications. However, it is still possible to calculate an average steady-state bottomhole pressure for plunger lifted wells as follows:
Option 1. If liquid level is measured in the annulus, provide a liquid level together with the production data. Make sure the liquid levels input correspond to times when the well is producing. This method is similar to how BHP is calculated for rod pump wells when liquid levels are available.
Why can't I select between flowing side or static (quiet) side when artificial lift is set to plunger lift?
Casing pressures are always used as a pressure source for plunger lift, ignoring tubing pressures. Therefore, it is always a static (quiet) side calculation, and hence there is no option to choose between flowing and static (quiet) side.
Option 2. Calculate the bottomhole pressures as if plunger was not installed by using the average rates of a producing time period (to capture the effect of less liquid in the tubing during the production period, it is also possible to reduce the OGR of the well). This option consists of:
- Find an average for the producing plunger lift stages (1 and 2). This requires the daily production rate (), the producing cycle duration (, in days), and number of cycles in a day ().
- Run a BHP calculation using the average and neglecting most liquid (e.g. assume dry gas, mist flow)
3.2.4. Gas-Assisted Plunger Lift (GAPL) and Plunger-Assisted Gas Lift (PAGL)
3.2.4.1. GAPL vs PAGL - What's the Difference?
Many people use these terms interchangeably to refer to combinations of gas-lift and plunger-lift. While we know of no formal SPE definition, we use GAPL to refer to gas-assisted plunger-lift, and PAGL to refer to plunger-assisted gas-lift.
Combination Lift Type | Description and Purpose | Conceptual Distinction |
---|---|---|
PAGL (Plunger-Assisted Gas Lift) | The plunger enhances and prolongs the economic viability of the gas-lift system by enhancing efficiency and economics at lower rates. This extends the operational period of the gas lift system toward the end of the life cycle before transitioning to another lift method. | Continuous gas-lift supported by a continuous-run plunger. |
GAPL (Gas-Assisted Plunger Lift) | Gas injection boosts and extends the economic life of the plunger-lift system by complementing the reservoir drive. This extends the operational period of the plunger-lift system toward the end of the life cycle before transitioning to another lift method. | Plunger-lift supported by continuous or intermittent gas injection. |
While both PAGL and GAPL, when appropriately applied, can enhance production over using a single lift method, they represent distinct lift approaches that can be strategically incorporated into the well's life cycle planning. By designing the well to anticipate these changes and minimize workover costs, one can optimize production and economic efficiency.
3.2.4.2. How Calculate BHPs for GAPL/PAGL systems?
As of now, it is not possible to input more than one artificial lift method in whitson+ simultaneously. However, in the case of GAPL/PAGL, we suggest using Option 2 + Gas Lift as the artificial lift method, under the Plunger Lift category mentioned above. Option 2 implies calculating the BHPs as if plunger lift were not installed, then using gas lift and accounting for the valve depth. Gas lift does not alter any of the plunger lift mechanisms. The only difference is that with a bottom packer, gas in stage 1 comes solely from the reservoir. With gas lift, a bottom packer disconnects the liquid level from the BHP.
3.2.5. Jet Pump
A jet pump consists of four static parts: nozzle, throat inlet, throat and diffuser. Highly pressurized power fluid is converted to kinetic energy through the nozzle. Reservoir fluid, with a much lower pressure, is accelerated into the throat. The fluids are mixed in the throat and a homogeneous mixture is developed at the diffuser inlet. The kinetic energy of the mixed fluids is converted to pressure energy in the diffuser. This pressure increase across the pump is what lifts the mixture to the surface. Jet pumps are one of the most difficult pumps to model for hydraulic calculations, and a lot of the information needed to make the calculation is proprietary to the pump owner. That is why most pump suppliers have their own software for modeling hydraulics with jet pumps.
In addition to the geometrical configuration and size of the different jet pump components, the most important jet pump parameters that are generally held confidentially by the jet pump supplier are the loss coefficients:
- Nozzle loss coefficient
- Suction loss coefficient
- Throat loss coefficient
- Diffuser loss coefficient
Recommendation for Well with Jet Pump.
It is possible to have a bottomhole pressure gauge installed while operating with jet pump, and that is the best way to estimate the flowing bottomhole pressure in such cases. An alternative to finding the correct bottomhole pressures for a period with jetpump is to use the custom pwf feature in whitson+, and “draw” a pressure profile in the jet pump period that is more aligned with an expected pwf decline for the given well. This exercise is even better if you have pwf before and after the jet pump was installed, so we are confident in the limits of the interval (and the drawing is not just a shot in the dark).
3.2.6. ESP
To set up a well with ESP, mainly, you want to ensure the following:
- Your inlet pressures are loaded into the Gauge Pressure (pwf, gauge) column,
- Your wellbore configuration is loaded with the change in wellbore configuration from previous to ESP at the right 'Use From Date'.
- Your wellbore configuration with ESP has a pump intake depth and 'Calculate from gauge to sandface using measured pressures' turned on. This computes the bottomhole pressure drop from the pump inlet to the top perforation - assuming the loaded gauge pressures record the pump intake pressures.
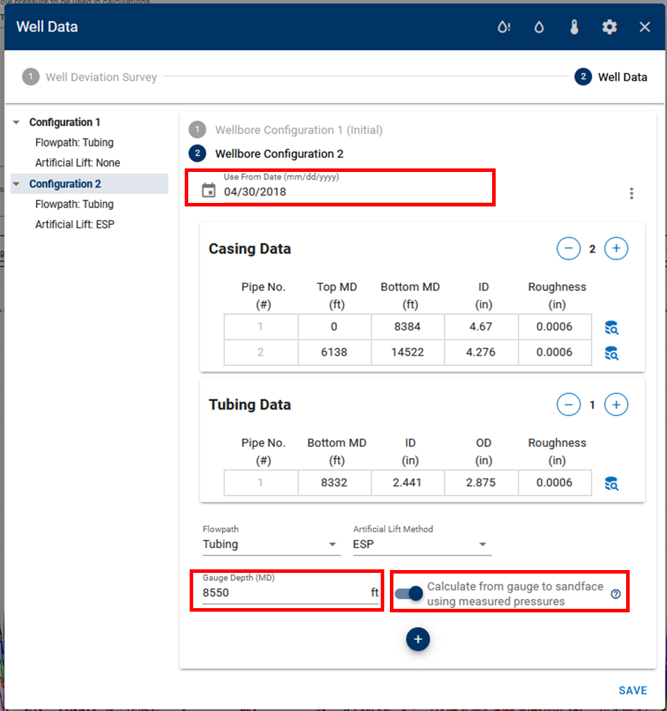
Finally, if everything like the pressure production data, looks okay and the pump is sized appropriately, the bottomhole pressure should show a smooth transition from previous wellbore configurations to flowing via ESP.
BHP Tuning Guidance
Be sure to not use these bottomhole pressures for tuning the correlations, this is why.
3.3. Dual-Conduit Flow
If the flow path is set to "Tubing and Annulus", the BHP is calculated by allowing the well stream to flow in through both annulus and tubing. The split of flow must be solved for by requiring that the pressure at the end of tubing is the same when calculating the pressure drop through both conduits, starting with casinghead pressure for the annular flow, and tubinghead pressure for the tubing flow.
3.4. Liquid Loading
3.4.1. Classical Critical-Rate Correlations
The Tuner[1] and Coleman[2] critical rates are the classical correlations of predicting the minimum required gas rate to avoid liquid loading. These correlations can be used at all depths along the well. The correlations rely on a force balance on a liquid droplet to predict the minimum velocity needed to lift the droplet. The only difference between the two correlations is that Turner is 1.2 times Coleman.
The equation for the Coleman critical velocity is
where \(C\) is a unit conversion factor (1.5935... in field units), \(\sigma_{Lg}\) is the liquid-gas IFT, \(\rho_L\) is the liquid density and \(\rho_g\) is the gas density.
Converting the velocity to rate is done by where \(A_h\) is the hydraulic area and \(B_g\) is the gas formation volume factor.
3.4.2. Critical-Rate Correlations Accounting for Well Inclination
A modification to the Coleman critical velocity was made by Belfroid[3] to account for the well inclination. This is useful if the critical rate is computed at a different depth than the wellhead. The modified velocity is: where \(\theta\) is the inclination (deviation from vertical).
Application of Belfroid's Correction
The correction could be applied to both the Turner and Coleman critical velocities. In whitson+, Belfroid refers to the modified Coleman critical velocity/rate.
Nagoo[4] suggested a different correlation entirely where is a unit conversion factor (0.53244... in field units). Both these velocities are converted to rate using Eq. (\ref{eq:rate})
3.4.3. Identifying Liquid Loading in whitson+ using Critial Rate Correlations
You can use the critical rate correlations above to see if the well is liquid loaded in the BHP feature itself.
Click on the 'Liquid Loading' tab in the BHP feature and choose the following:
- Critical Rate Correlation: to calculate and plot the minimum required gas rate required at the critical rate depth to avoid liquid loading. Choose between Turner, Coleman, Nagoo and Belfroid - the plot should update with the chosen correlation. You can switch between these, without having to recalculate BHP if these are already calculated once.
- Critical Rate Depth Type: Depth at which this correlation is used to calculate critical rate. Ensure that the BHP is calculated at least once and every time the critical rate depth is changed, to ensure the critical rate is recomputed for the right depth. Default critical rate depth, for consistency, is 'End of Tubing' for all wells. For wells without tubing in the wellbore configuration, the default critical rate depth will be 'Top Perforation' instead.
- Critical Rate Multiplier: Multiplier applied to all calculated critical rates for liquid loading. Use this to account for field-specific calibration. For example, enter 1.1 if actual critical rates in your field are consistently 10% higher than the Turner-calculated rates.
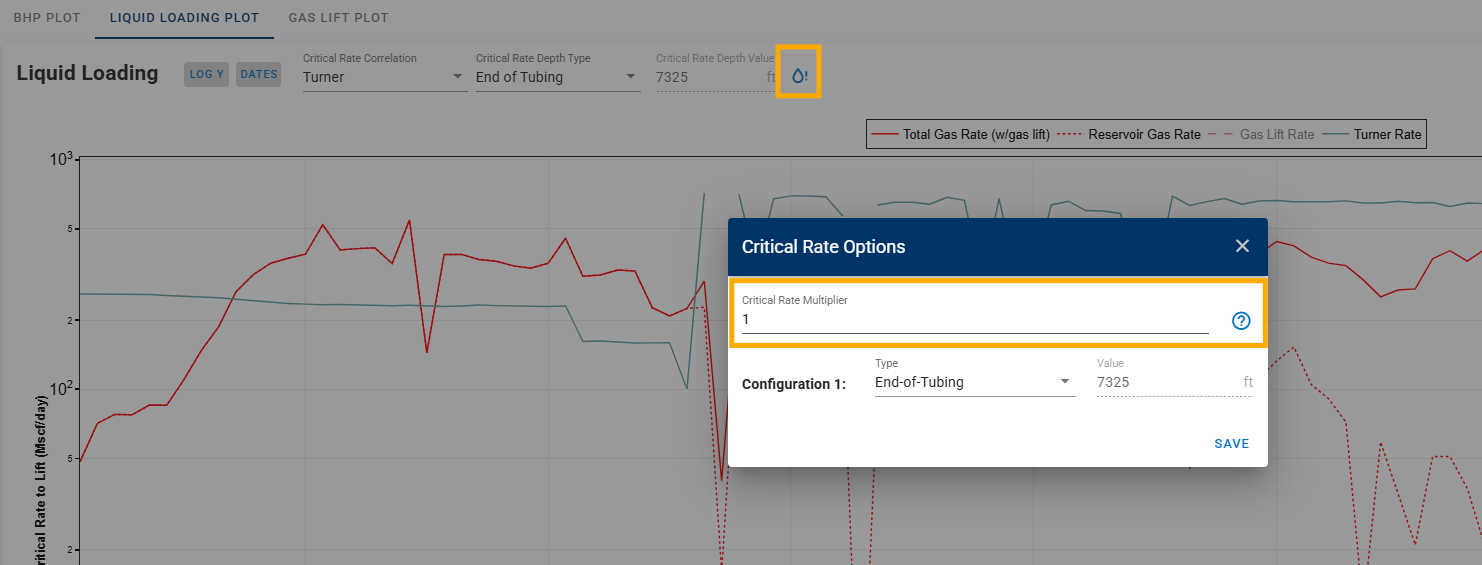
Why is the default critical rate depth 'End of Tubing'?
Within the tubing, the pressure is highest at the End of Tubing (EOT), and therefore the gas velocity is the lowest at the EOT. This is the location, within the tubing, we are most at risk for liquid loading. In short, if we are able to lift liquids at the EOT, we are guaranteed to lift liquids at every depth above the EOT in the tubing, due to the pressure decreasing and the gas velocity speeding up. Alternatively, we may be above the critical lift rate at the surface, but that tells us nothing about whether we're liquid loaded deeper in the wellbore.
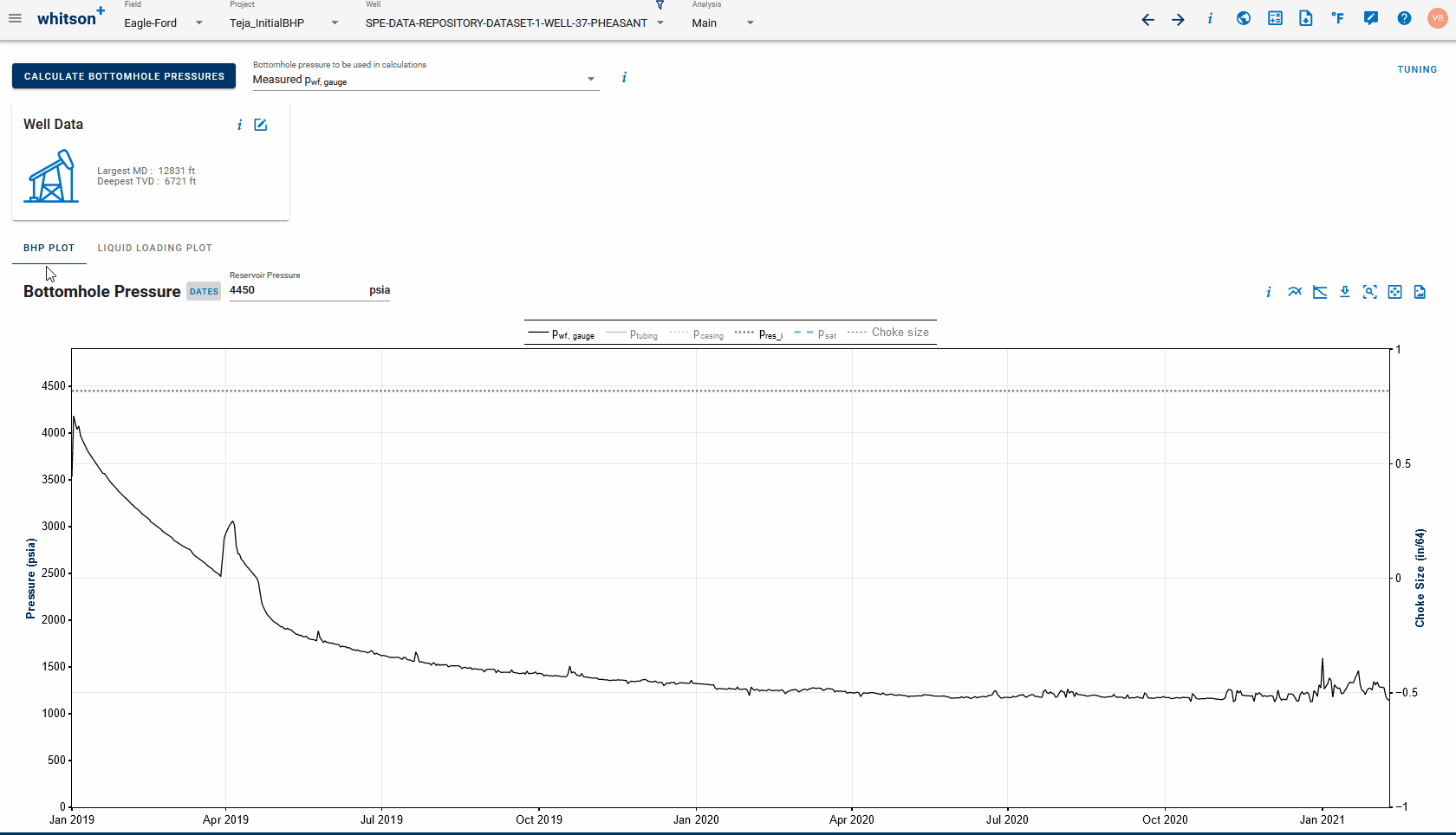
BHP Calculation Dependency for Critical Rate Correlation
Ensure that the BHP is calculated at least once and an appropriate 'Bottomhole Pressure to be used in calculations' is also chosen because the critical rates will change accordingly. You need to strictly use one of the correlations for calculating critial rates so if you have 'Measured pwf, gauge' or 'Custom pwf' selected in 'Bottomhole Pressure to be used in calculations', they will default to Hagedorn and Brown.
Critical Rates can be calculated for the following critical rate depth types:
Depth Type | Description |
---|---|
Wellhead | Critical rate is computed at the wellhead, i.e., at surface (depth of 0 ft). |
Top Perforation | Default if tubing is absent – Critical rate is computed at the top perforation depth (as entered in the well data card). |
End of Tubing | Default if tubing is present – Critical rate is computed at the end of tubing, i.e., at the tubing intake (as per the wellbore configuration). |
Maximum Rate | Critical rate is calculated at all depths and the reported rates are the maximum rates calculated (at variable depths) throughout well history. |
Specified | Using this option, you can manually specify the fixed depth at which critical rates are to be computed throughout well history. |
Multiconfig | To compute the critical rate at different depths, specific to each wellbore configuration, across well history. |
Visualizing Pressures on the Liquid Loading Plot
You can toggle pressures on and off (using the 'Show pressures' button to the top-right of the liquid loading plot) to view the currently used bottomhole pressure, casing and tubing pressures and the difference between them on the same plot.
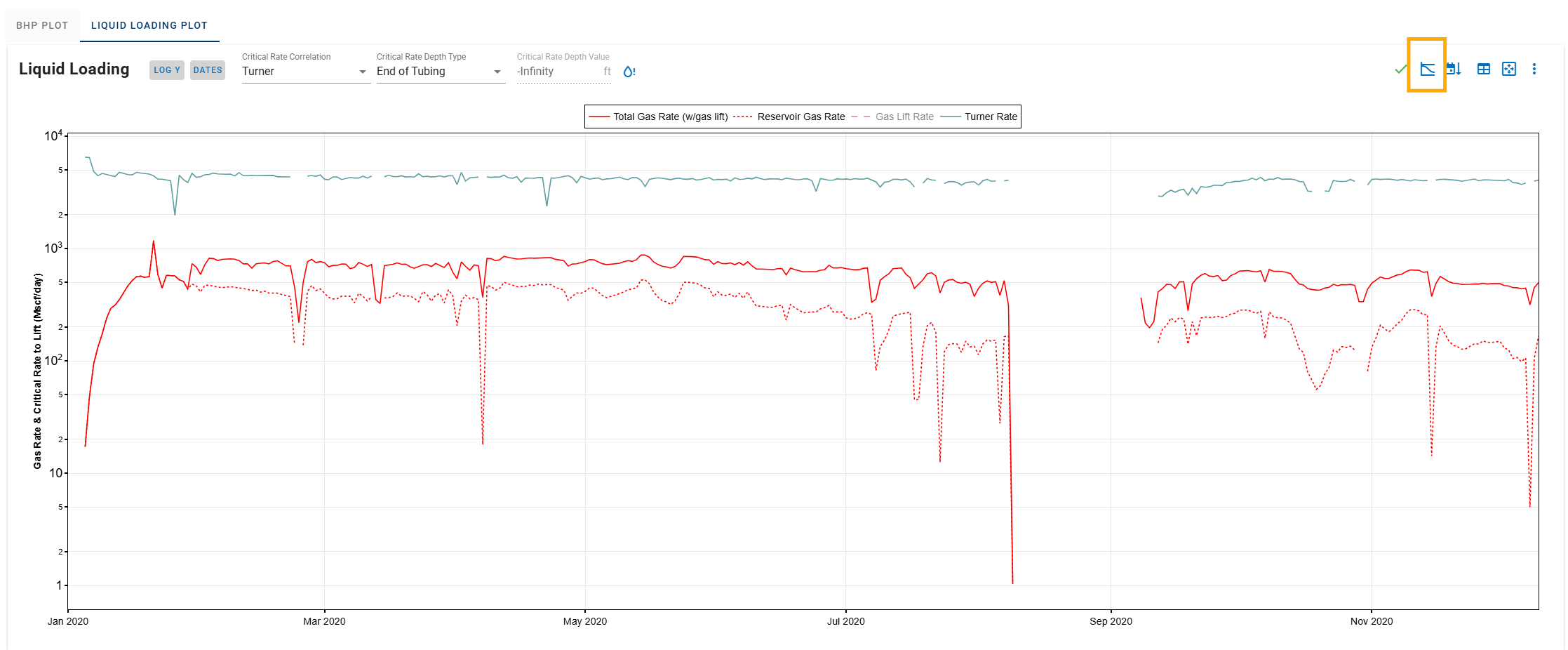
3.4.4. Critical rate correlations in nodal analysis
Here's an example well use case justifying the use of 'End of tubing' as the critical rate depth and quantifying the gas rates needed to prevent liquid loading using the Turner correlation:
In terms of critical velocities:
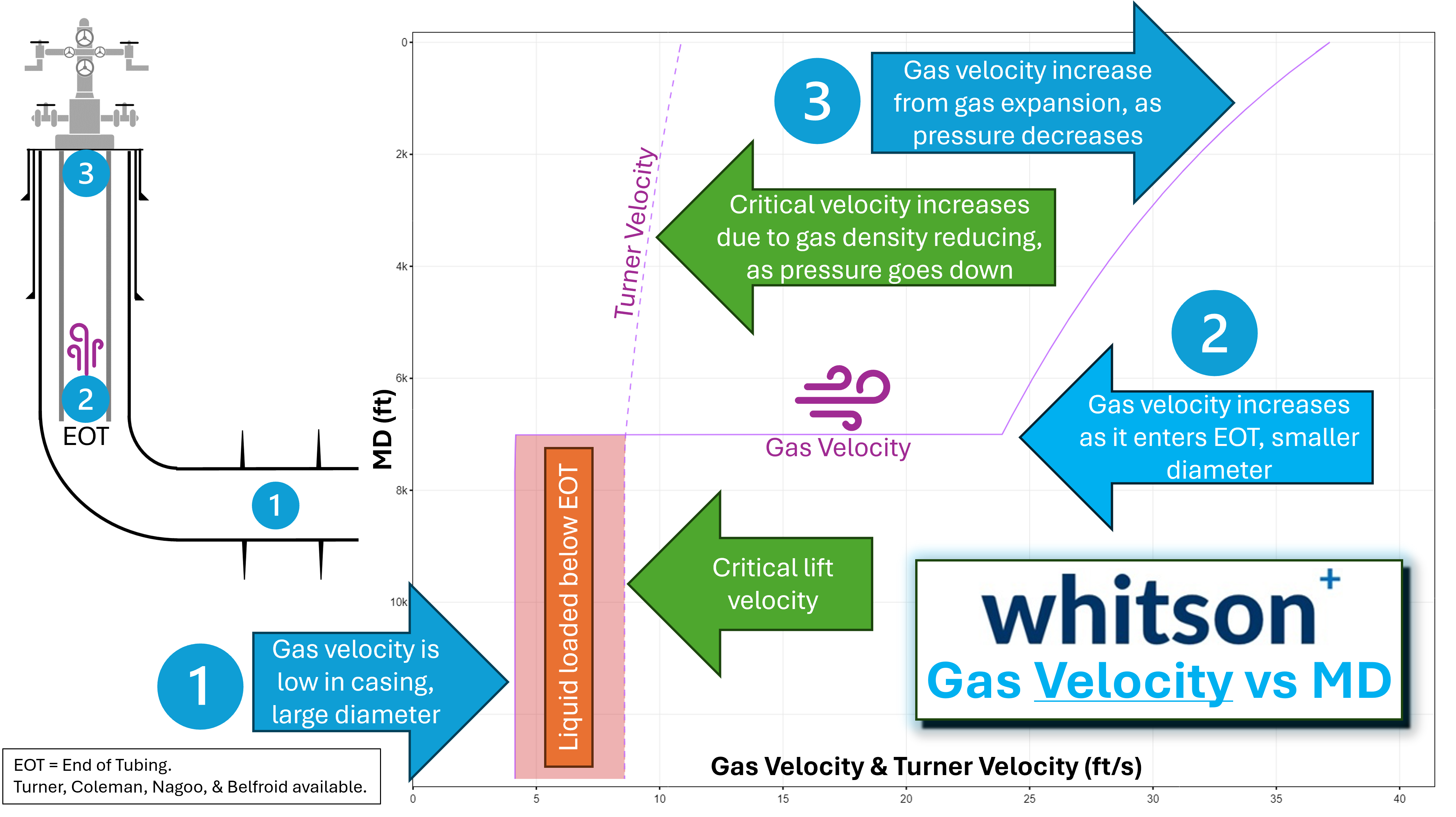
In terms of critical rates:
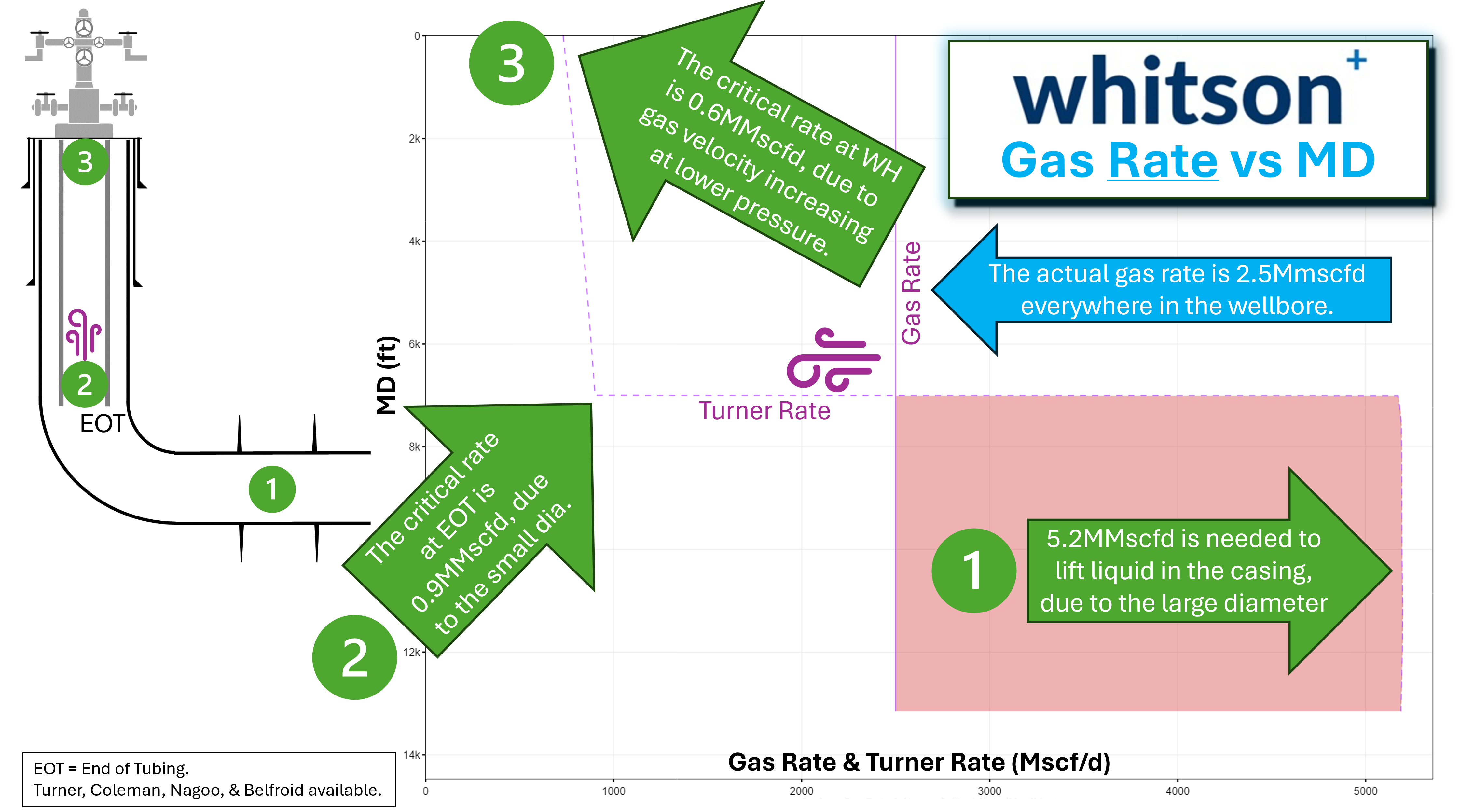
You can compute the critical and superficial velocity/rate vs depth and generate these plots in the Gradient tab of the Nodal Analysis feature for your wellbore.
3.4.5. Indentifying Liquid Loading - Some practical tips
Two typical signatures of a well experiencing liquid loading are:
- The gas rate drops without a change in the wellhead (casinghead and/or tubinghead) pressures.
- The casing-tubing goes from flat to increasing (casing pressure minus tubing pressure is pretty flat when unloaded, once loaded, the tubing pressure starts to fall, so the delta between casing and tubing goes from flat to increasing).
3.5. Correlation Tuning
The BHP tuning functionality can be accessed by clicking Tuning to the upper right of the BHP feature as seen below.
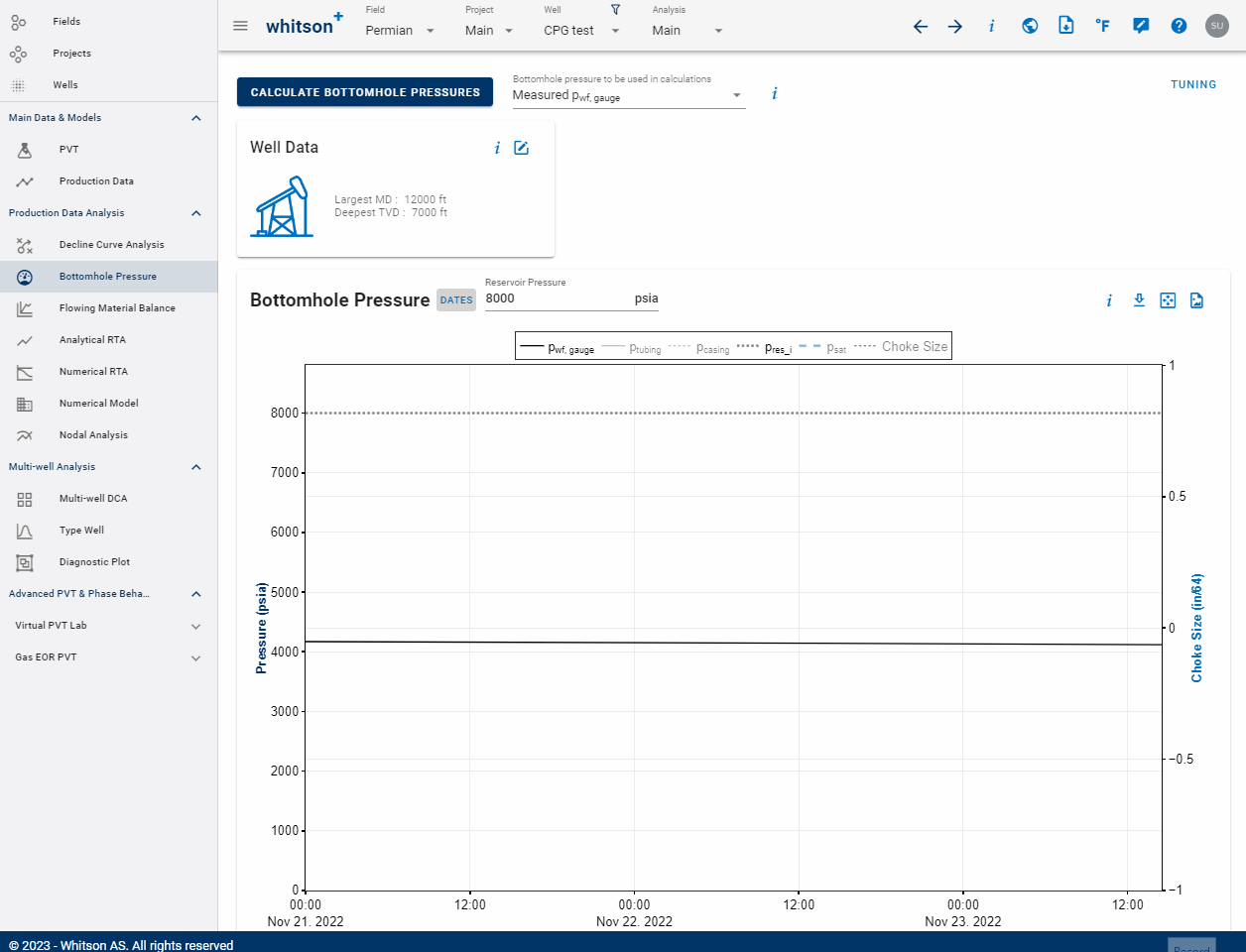
The following video illustrates a practical example of "BHP correlation tuning to measure gauge data"
3.5.1. Correcting the Properties
The multiphase-flow correlations used to compute the bottomhole pressure can be tuned in whitson+. This is achieved by correcting the liquid hold-up by a parameter \(\alpha\), and the friction factor by a parameter \(\beta\). Correcting the liquid hold-up affects mainly the gravity pressure drop, while correcting the friction factor affects the friction pressure drop. The corrections are made as follows:
Liquid Hold-Up Correction:
The liquid hold-up, \(H_L\), is always lower bounded by the liquid flux fraction, \(C_L\), and upper bounded by 1. To honor this bracketing in a tuning process, it is easier to convert the liquid hold-up into an equivalent slip velocity that is only lower bounded by 0, and then apply the \(\alpha\) parameter as a correction multiplier. The slip velocity is defined as
where \(v_g\) and \(v_L\) are the gas and liquid velocities, and \(v_{sg}\) and \(v_{sL}\) are the superficial gas and liquid velocities. Solving (\ref{eq:slipVelocity}) for \(H_L\), we get:
The liquid hold-up correction is made by
- Compute the slip velocity \(v_s\) from \(H_L\) predicted by the default/untuned correlation using Eq. (\ref{eq:slipVelocity})
- Multiply the slip velocity by \(\alpha\) to get \(v_{s}^{corr}=v_s\alpha\)
- Calculate \(H_L^{corr}\) with the corrected slip velocity \(v_s^{corr}\) using Eq. (\ref{eq:liquidHoldUp})
Friction-Factor Correction:
The friction factor is corrected by multiplying the calculated friction factor from the default/untuned correlation by \(\beta\).
3.5.2. Selecting the Measured Pressure Points to Tune
The tuning procedure includes a routine that selects a subset of the measured gauge data over time. This is done for two reasons, (1) to speed up the tuning process by computing less pressures points, and (2) to minimize the effect of outliers. The sampling procedure involves three steps:
- Remove outliers that has more than a 20% relative difference from its neighbors.
- Compute a moving average of the filtered data.
- Sample the moving average at a constant spacing of 20 days.
3.5.3. Correlation Tuning Using Measured Pressures from an ESP
Measured pressures from an electric submersible pump (ESP) should not be used to tune the bottomhole-pressure correlations. The reason for this is that the computed pressures from wellhead to gauge (situated at the ESP inlet) does not account for the delta-pressure caused by the ESP.
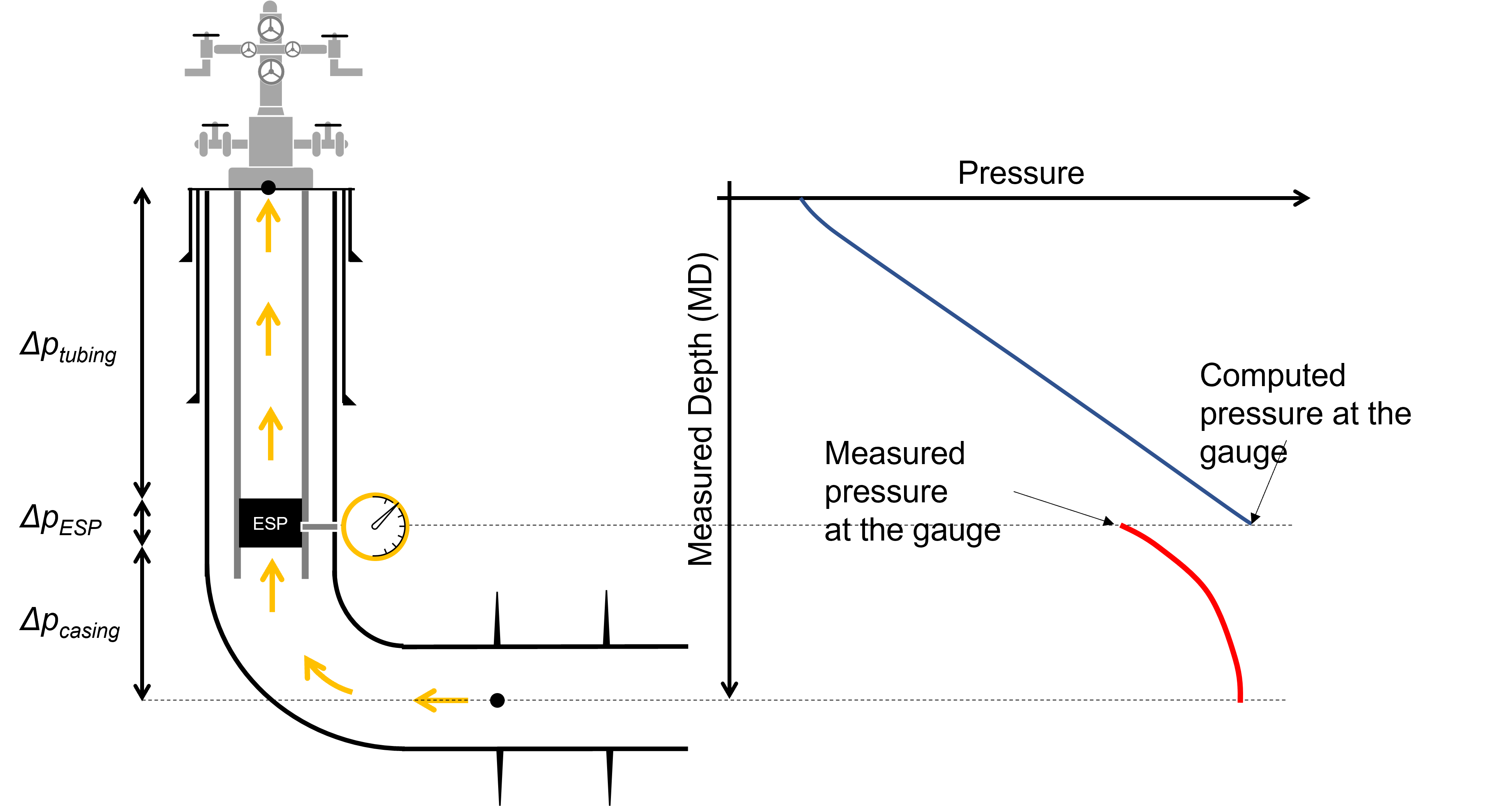
3.6. Estimating Initial Reservoir Pressure in whitson+
Here we are estimating reservoir pressure from flowing pressure and rate data, typically acquired for most wells. These are just approximation methods involving uncertainty and other tests, specific to this purpose, like Diagnostic Fracture Injection Tests (DFIT), downhole formation testing tools, pre-frac step-rate injection tests, post-frac instantaneous shut-in pressure combined with frac gradient relationships, opening pressure of the first port for packer/sleeve completions, etc., should be used wherever available.
In whitson+, the already available rates and pressure data can be used in two ways to estimate reservoir pressure:
3.6.1. Reservoir Pressure from flattening of flowback BHP before hydrocarbon production
This technique is outlined in Jones et al[5], (URTeC: 1934785), and consists of three steps to diagnose reservoir pressure from flowback data (preferably hourly):
- Calculate BHP for the flowback data using a suitable multiphase flow correlation.
- Plot BHP along with rate and other pressure data.
- Look for a flattening or minimum BHP, just before the first measurable hydrocarbon production is reported. Casing pressure might show a similar pattern too. This flat portion or minimum in the BHP curve is the estimated reservoir pressure.
Assumptions
Produced fluids during flowback are initially 100% water, with delayed hydrocarbon breakthrough. Flowback begins shortly after the frac was completed and the frac plugs are drilled out.
This is so that there is least uncertainty in the calculated BHP initially and the BHP at the beginning of flowback is higher than the estimated reservoir pressure, so the "frac charge" is not allowed to dissipate through leakoff (such as during an extended shut in or installation of artificial lift after the frac job). Hourly flowback data makes it easy to identify the pressure behavior associated with first hydrocarbon production.
The simplest explanation for this might be that trace amounts of immeasurable hydrocarbons (due to relatively high water rate) start entering the wellbore and arrest the decline in wellhead pressure, hence BHP tends to remain flat just before measurable hydrocarbon is separated from the flowback frac water and rates are reported.
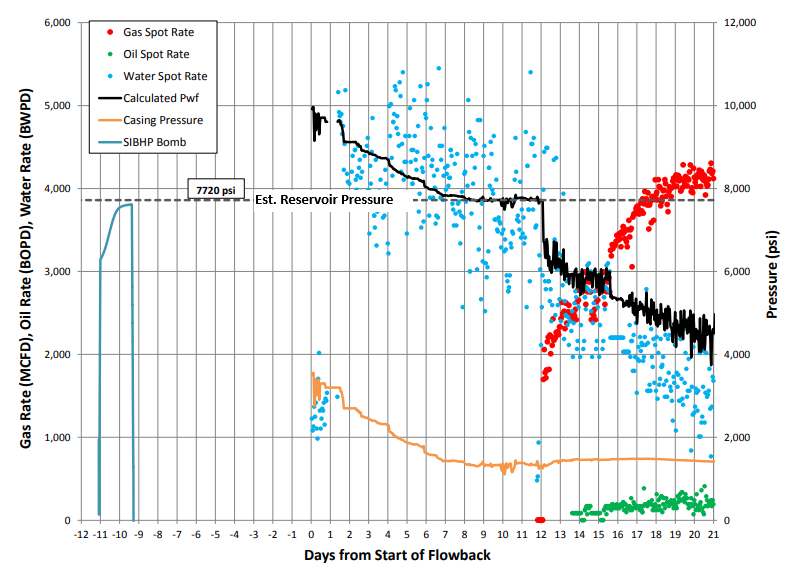
Example flowback data for estimation of reservoir pressure (from Jones et al, URTeC 1934785)
The flattening of BHP, identified as reservoir pressure, may be too short or completely missing if the drawdown is too aggressive, productivity is too low, finite conductivity fractures, near wellbore skin damange, or large changes in choke instead of gradually and monotonically opening them. In these cases, the data has step changes in rates and pressures, or BHP reduces quickly and significantly below the actual reservoir pressure - making it really difficult to identify reservoir pressure.
Visualizing BHP, Rates, and Surface Pressures
In the BHP feature, you can plot rates and pressures simultaneously, as outlined above by clicking the 'Show rates, surface pressures' button on the top right of the BHP plot.
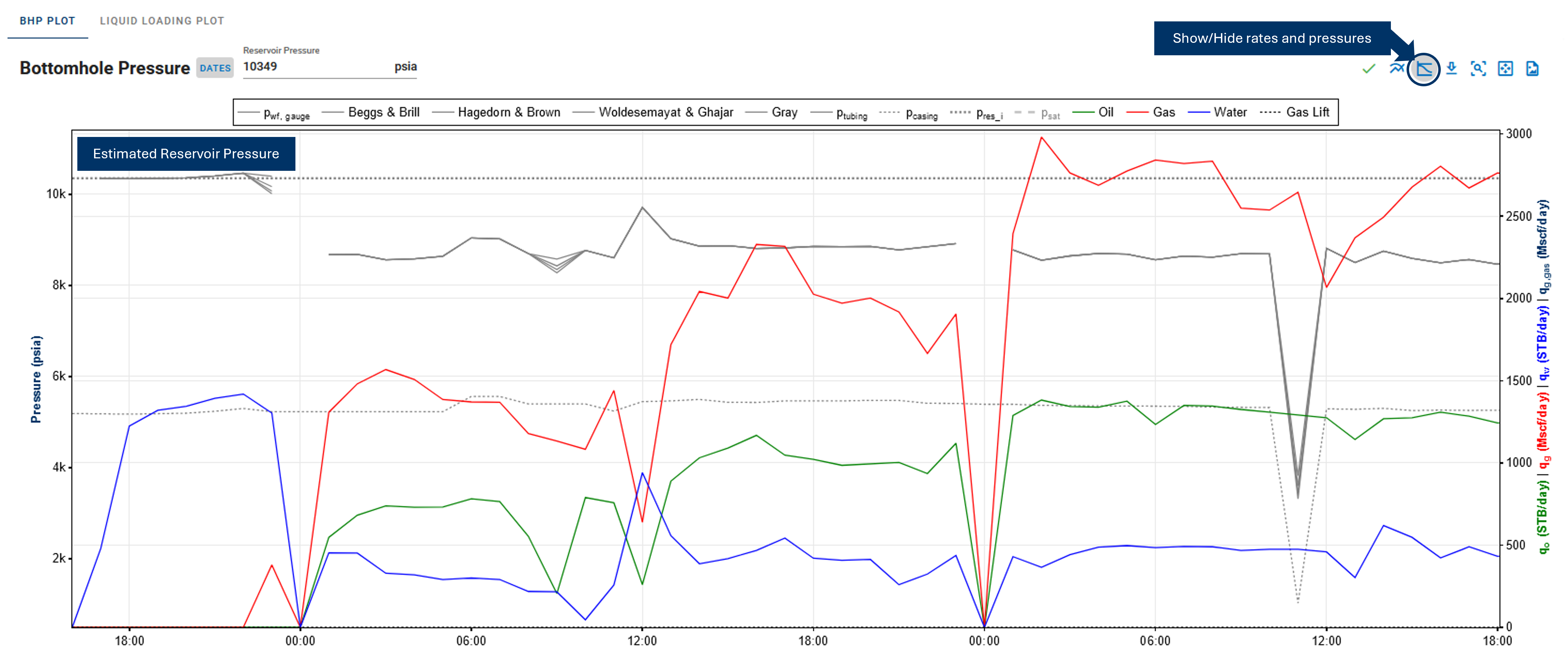
Be sure to zoom into the very early time section of the data and appropriately adjust pressure and rate axis limits on the plot to display a diagnostic plot similar to the one referenced from the paper.
3.6.2. Reservoir pressure from IPR
Here are the steps to estimate reservoir pressure from an approximate IPR fit to BHP vs Rate data:
- Calculate BHP for the pressure and rate data available.
- On the Bottomhole Pressure plot, click 'Estimate Initial Reservoir Pressure' button on the top-right. This opens a new dialog box allowing you to view BHP vs rate plots to choose the IPR type, the BHP correlation to be used and number of days of data to be displayed on this plot.
- By default, the oil wells will plot the calculated BHP vs. measured oil rate data for the first 10 days after oil breakthrough, and use the Vogel's IPR curve. Alternatively, for gas wells, the plot defaults to BHP vs gas rate and C&n or the backpressure equation for IPR type.
- Lasso fit at least 2 or more points to calculate the slope or productivity index and the saturation pressure (from the well's PVT) is used to set up an approximate IPR fit to the data.
- Extrapolation of this IPR to the y axis (or the intercept) gives the initial reservoir pressure.
- Click save to update the initial reservoir pressure for the well with this value.
These steps are shown in the GIF below:
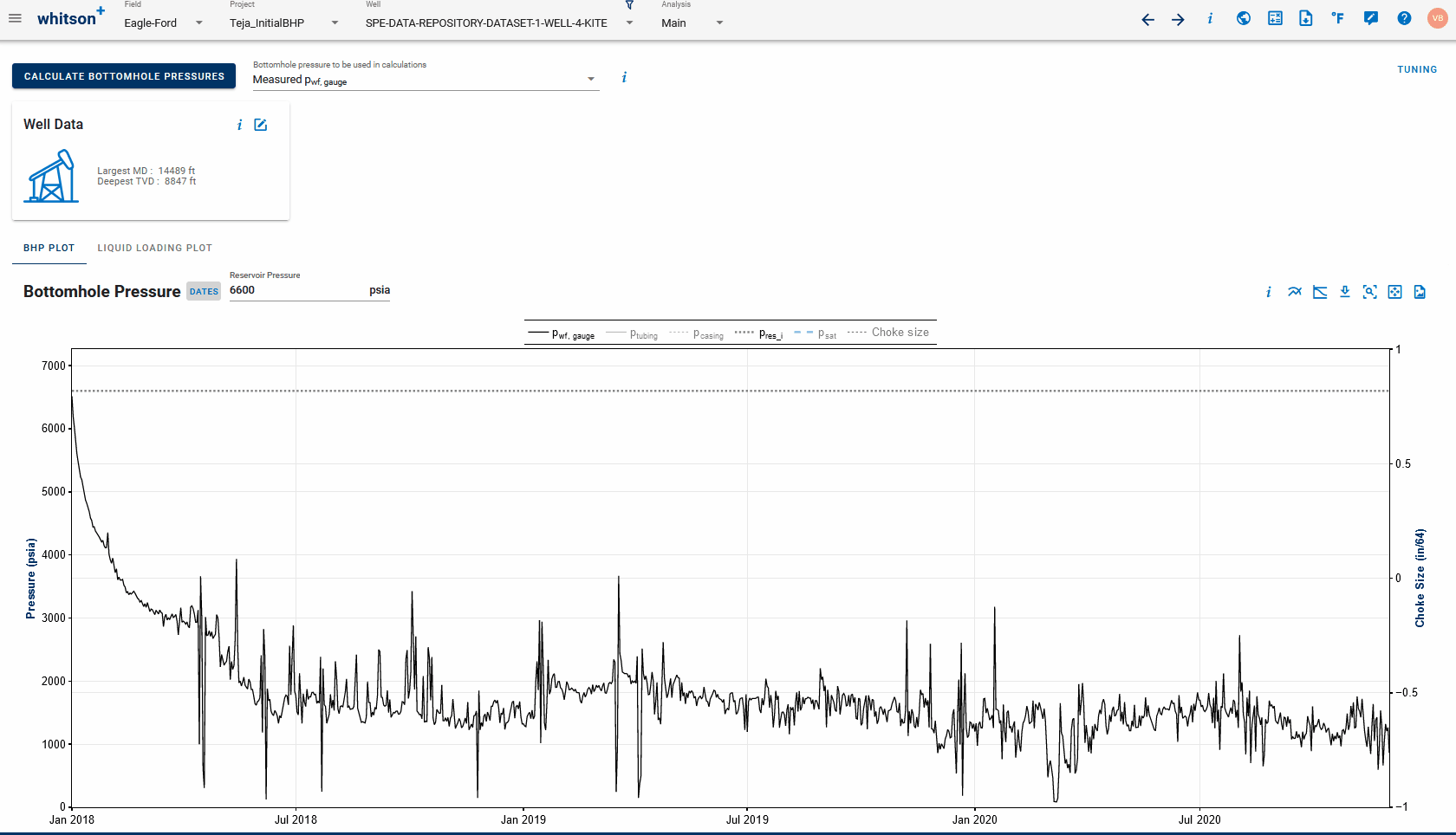
3.7. Activate BHP Injection Mode
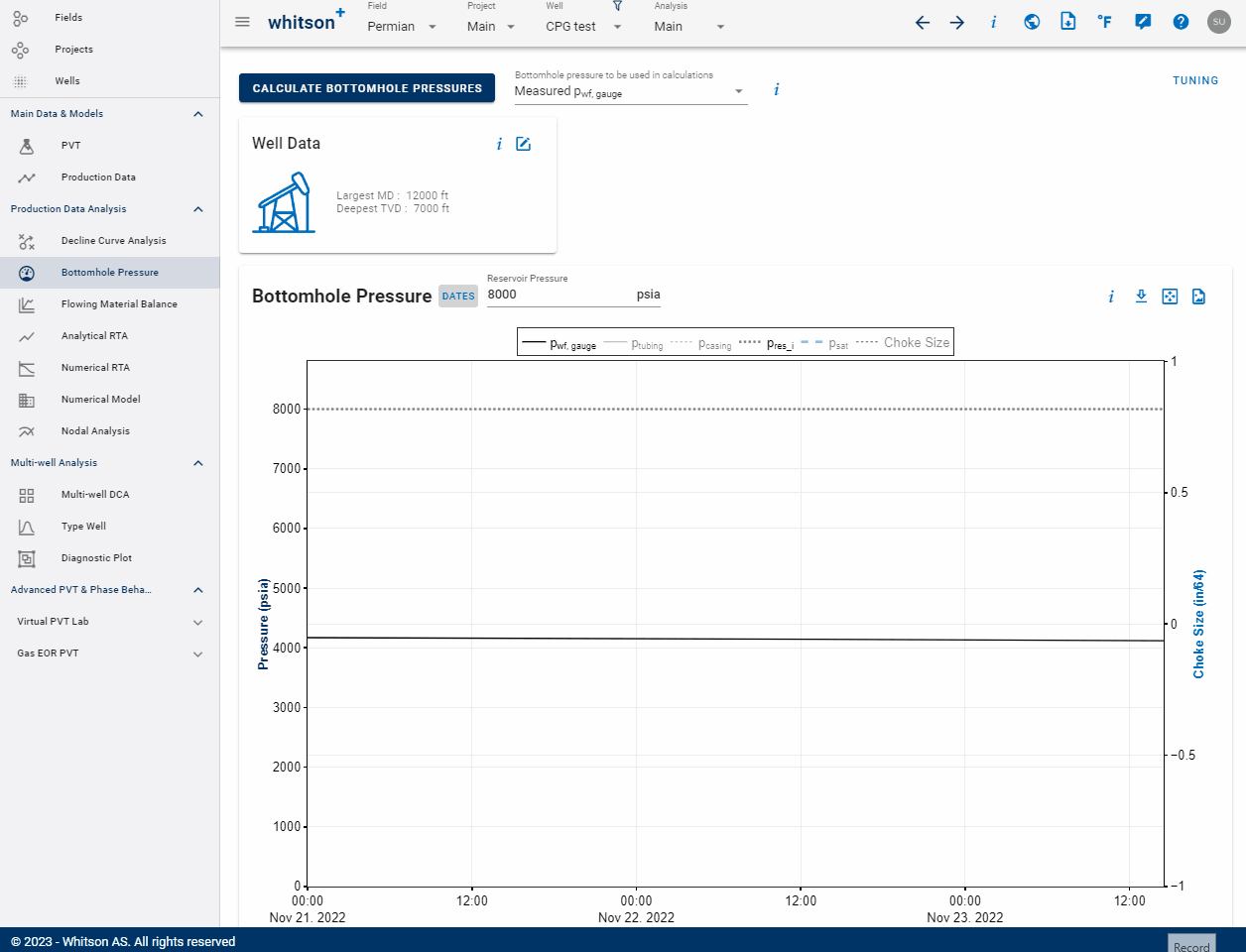
If you want to model the bottomhole pressure during an injection process, that can be done by activating the BHP injection mode. This is done in the Calculation Settings in the Well Data card as seen above. When enabled, this switch allows to simulate the pressure at the bottom of the wellbore during injection. All uploaded rates (e.g. oil, water or gas) will be assumed to be injected rates.
3.8. Shut-in Well Settings
Select whether the BHP calculator should skip or compute the BHP on days when the well is shut (i.e., all rates in the production data are missing or zero).
The shut-well BHP can be calculated by assuming a gas-filled well or by using a specified gradient.
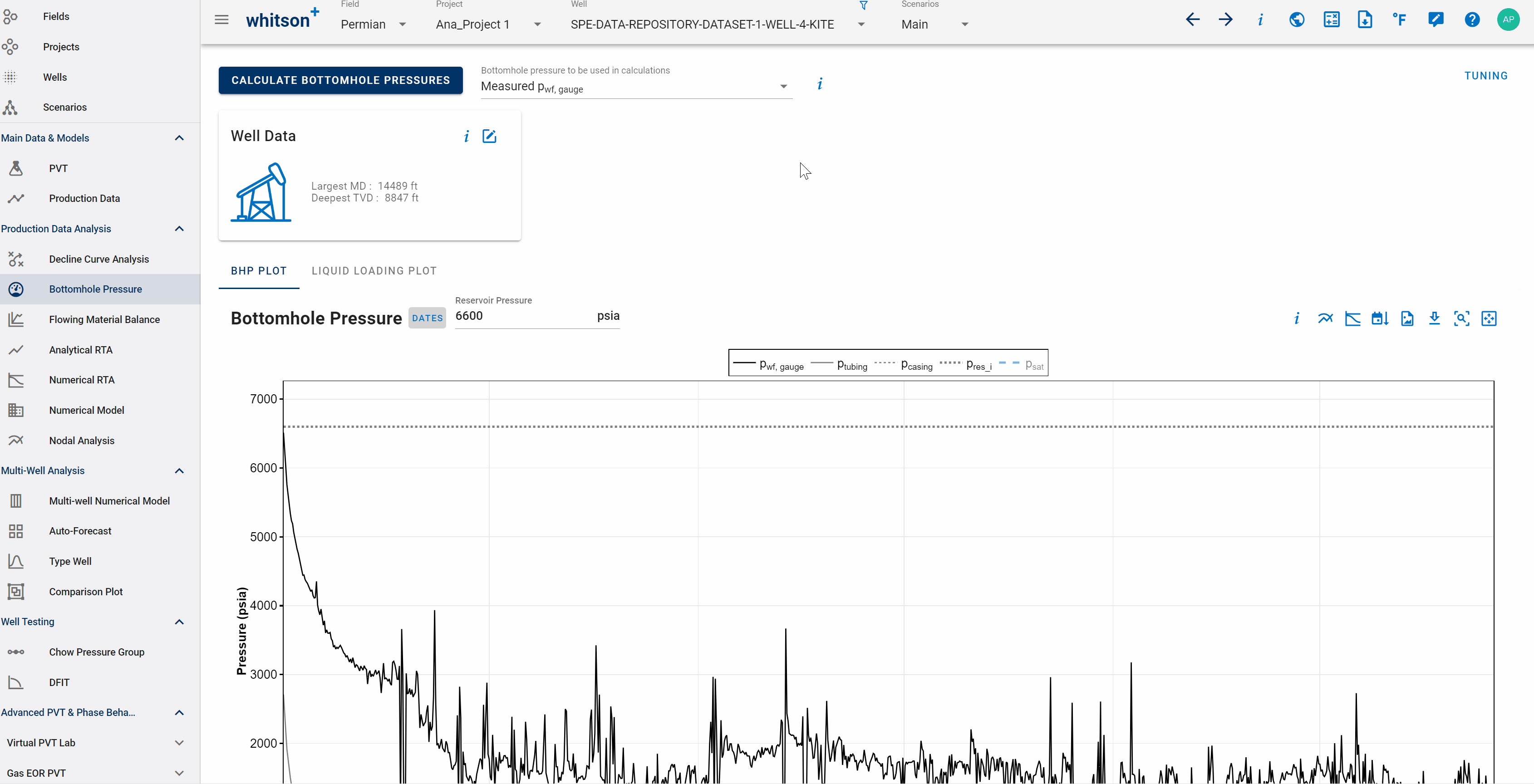
3.9. Choke
The choke setting represents a pressure restriction point in the wellbore or surface facility and determines the pressure drop between two points in the system. This is typically between the wellhead and surface flowline, or at a specified downhole depth. Each wellbore configuration includes one choke settings such as choke coefficient, choke depth, and choke size.
What is Choke Coefficient?
The Choke Coefficient is a correction factor used to account for vena contracta effects and irreversible energy losses. This coefficient can be estimated using single-phase valve coefficients provided in manufacturer datasheets, or more accurately determined through field calibration with measured field data.
When configuring a choke in whitson+, it is important to understand which pressure reference is required depending on where the choke is located:
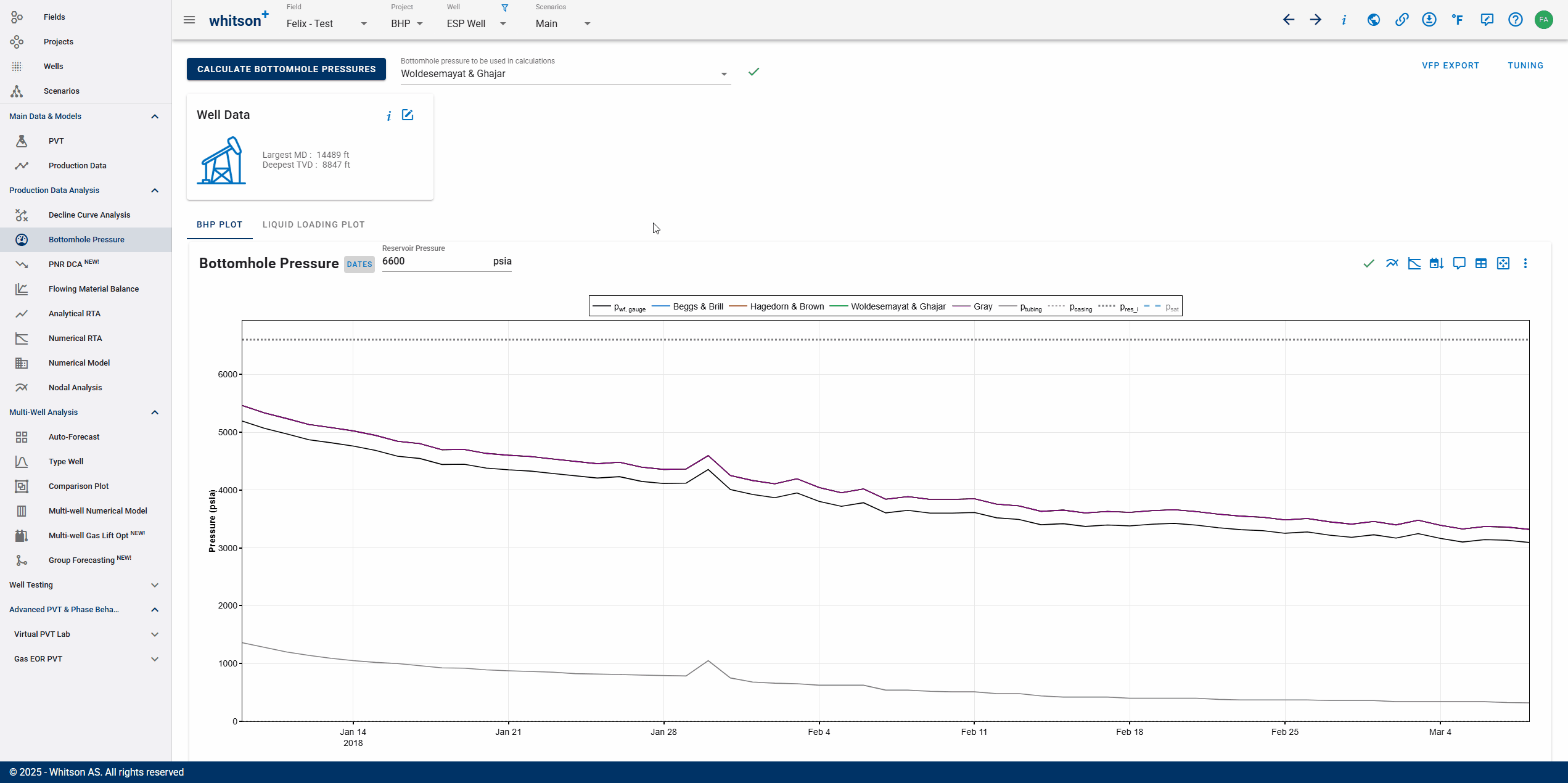
-
For wellhead chokes, the line pressure should be used. Otherwise, you can choose to fall back on tubing or casing pressure using the toggle shown below. Moreover, note that the choke depth is always zero and the choke size is fetched from production data.
-
For Downhole Choke, the default tubing or casing pressure is used. The choke depth and size (opening) are required. If choke size changes with time, user can add new configurations and edit the size for those configurations.
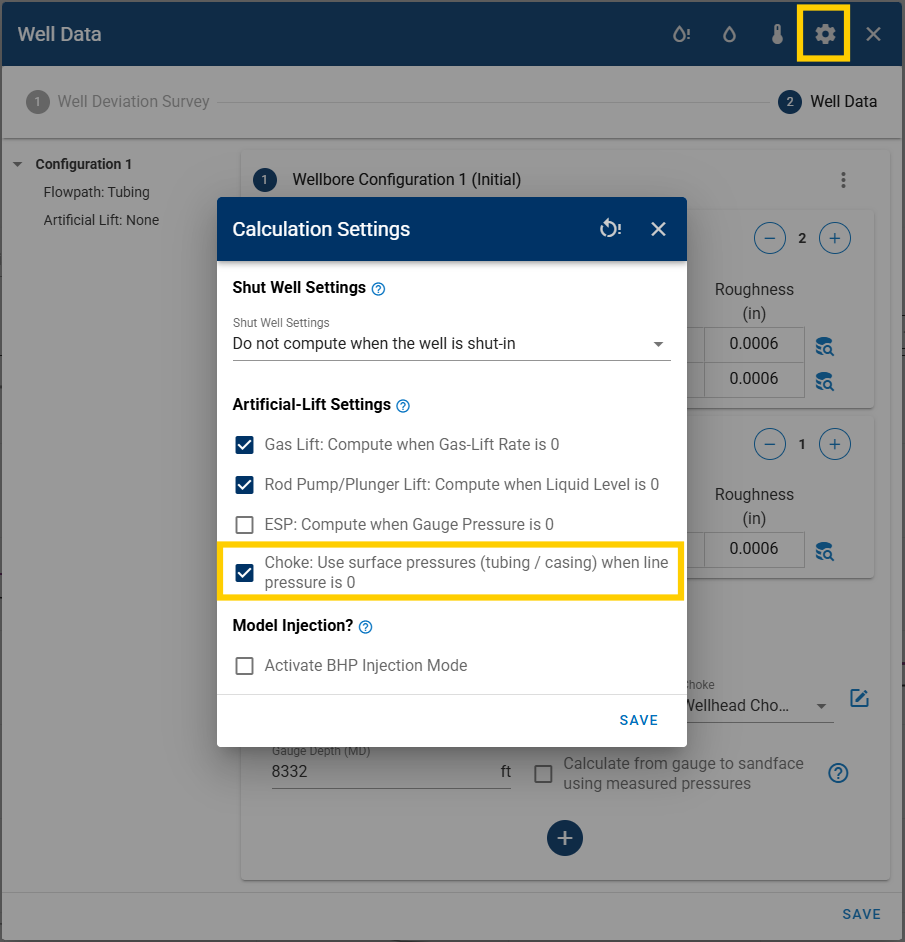
Operational Envelope
A fixed opening wellhead or bottom-hole choke will display the performance curve (pressure drop vs. surface oil or gas rate), shown in the figure below.
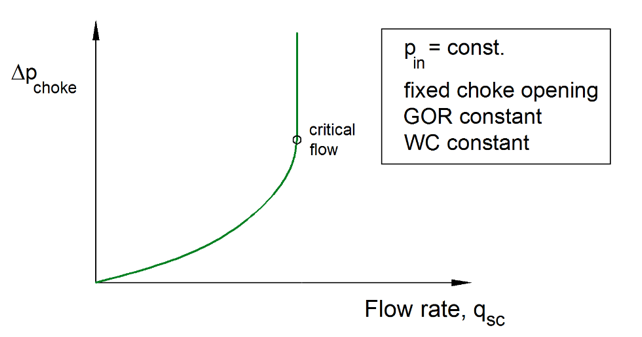
This curve is generated by keeping the inlet pressure, GOR, and WC constant, while changing the downstream pressure from the inlet pressure value to atmospheric conditions (see the sequence plotted in the animation below).
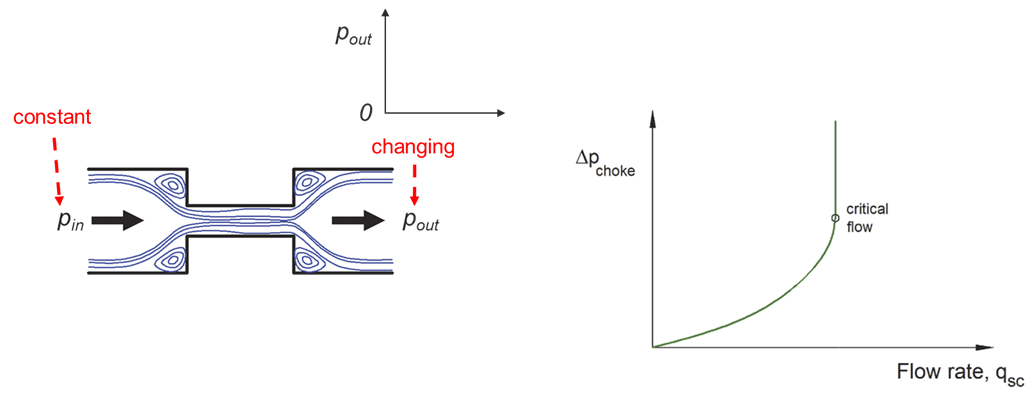
The pressure drop across the choke increases in a non – linear manner when the rate is increased. However, there is a point where it is not possible to increase the rate further (i.e., the pressure downstream the choke does not impact the rate flowing through the choke). This is because the fluid velocity at the throat of the choke has reached the sonic velocity. This typically occurs when the pressure ratio is between 0.5-0.6.
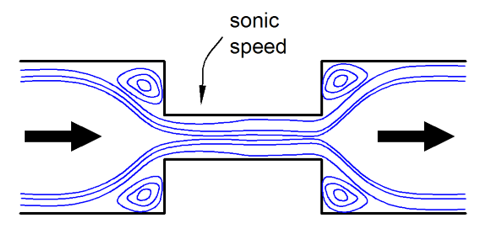
The figure below shows the behavior of pressure along the axis of a bean choke. Note that pressure drops suddenly when the flow encounters the contraction point. In gas-dominated flows this sudden pressure reduction can cause cooling (due to the Joule-Thomson effect), liquid condensation and ice formation (in the presence of free water).
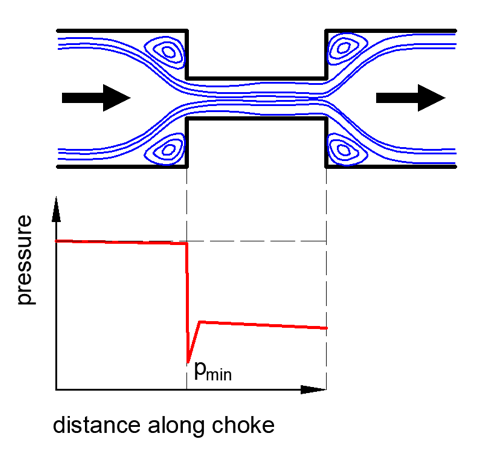
The figure below shows the performance curve of the choke when the inlet pressure is varied. The pressure drop at which the critical flow is reached increases proportionally with the inlet pressure: . Changes in GOR and WC give a similar variation of the performance curve.
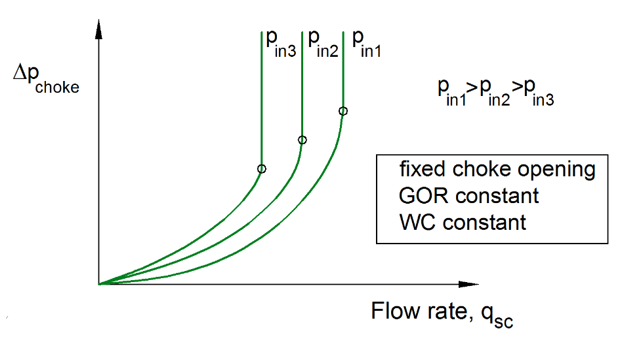
The figure below shows the choke performance curve for 5 different choke openings. A smaller opening will provide a larger pressure drop than a larger opening, and critical flow will be reached at lower flow rates.
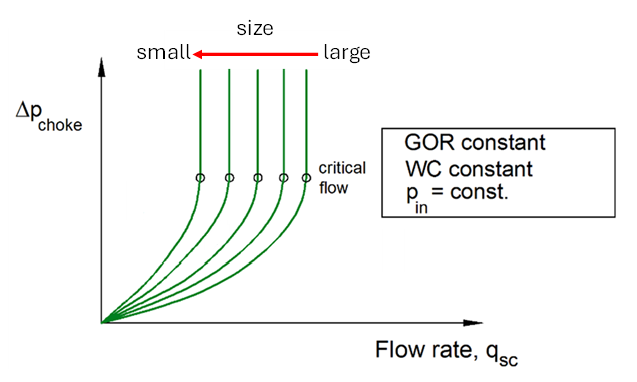
Choke Planning Using Nodal Analysis
Consider the situation shown in the figure below. A nodal analysis is performed at the bottomhole on a well with no wellhead choke. The equilibrium rate is higher than the target rate; therefore, choking is required.
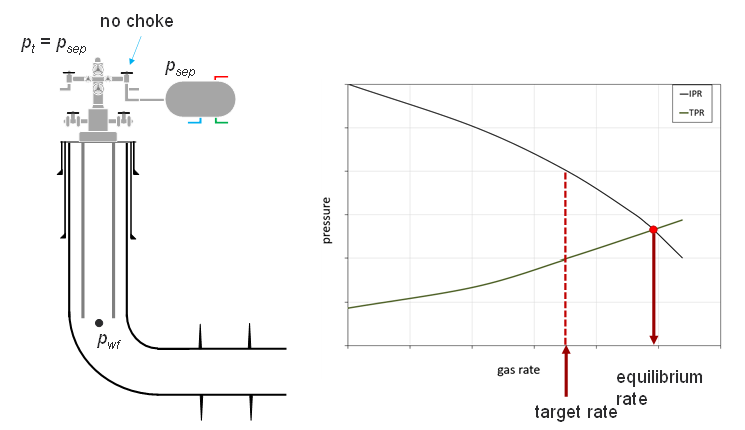
If a bottom-hole choke is used, the choke must drop the pressure from the pressure available from the reservoir (marked with * in the figure) to the pressure required to flow to the surface through the tubing (marked with ** in the figure).
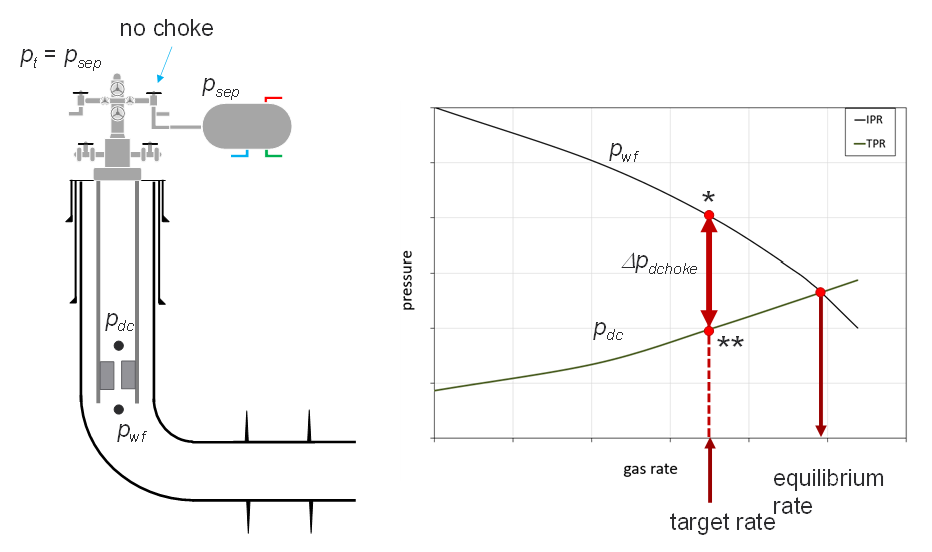
Another alternative is to use wellhead choking (shown in the figure below). In this approach, wellhead choking increases the tubing head pressure and “shifts” the TPR up, moving the intersection to the left.
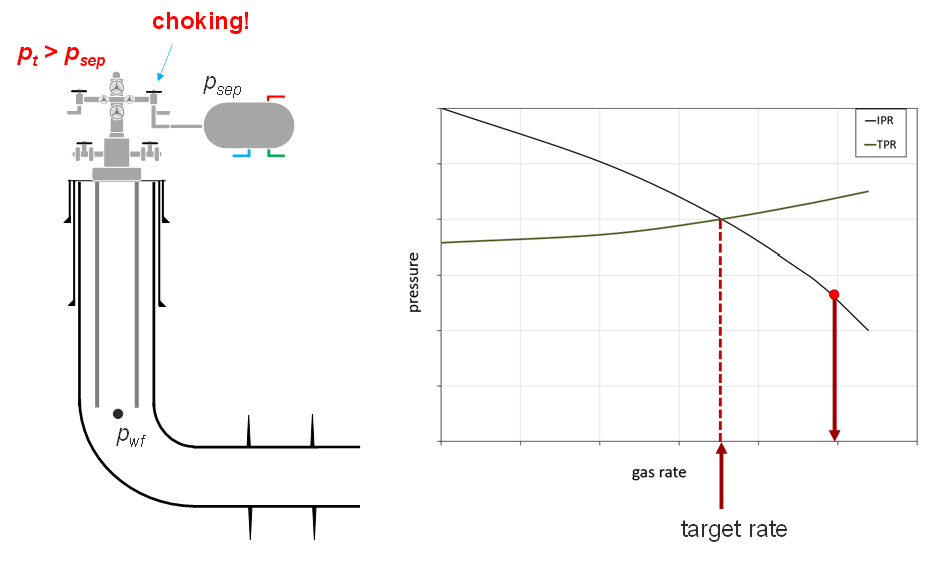
Choke Modeling
Chokes are often modeled by integrating the differential version of the momentum equation between the choke inlet and the throat and assuming no friction or localized losses between these two points. Due to the convergence of the flow, the effective throat cross-section area (often referred to as vena contracta) is not exactly equal to the throat cross-section area (), thus a correction factor () is introduced () and is often varied in the range (0,1] such that the model predicts accurately measured data.
The one-dimensional momentum equation in differential form for liquid-gas flow, neglecting friction and localized losses, is:
where is holdup, is velocity, is density, and pressure.
The whitson+ model assumes liquid and gas travel at the same velocity (mixture velocity, , equal to the sum of local rates of oil, gas and water divided by cross-section area). Then, the equation above is integrated between the inlet and the throat, while neglecting inlet velocity, to obtain:
is the homogeneous mixture density, defined as:
where is the gas mass fraction, and , are the gas and liquid phase densities, respectively.
Calculation Details
In all whitson+ applications like bhp calculations and nodal analysis, rate across and pressure downstream the choke are known, and it is desirable to find inlet pressure.
The equation is solved by computing numerically the homogeneous density integral, assuming isothermal flow and thermodynamic equilibrium. However, there is some care to be exercised about the pressure value to employ at the throat.
When operating in the subcritical regime, the pressure downstream of the choke is usually employed to approximate the pressure at the throat, assuming there is very little pressure recovery after the throat. When operating in the critical regime, the pressure measured downstream of the choke is lower than the pressure at the throat and is initially unknown. The main challenge is that often it is not known beforehand if the choke is operating in the critical or subcritical regime, so the calculation requires some trial and error.
As an example, consider the flow of dry gas through a choke, outlet pressure equal to 50 bara, inlet temperature 80 °C. The figure below shows the value of the residual of the choke model for a rate of 1e6 Sm3/d, and for several combinations of inlet pressure and throat pressure values, from 50 bara to 500 bara. Cases where the inlet pressure is lower than the throat pressure are discarded. The black line is the inlet-throat pressure combinations where the residual is zero (potential solutions to the choke model). The physical solution is the minimum point in the black curve. When the minimum lies when the throat pressure is equal to the downstream pressure, the choke operates in the subcritical regime. Otherwise, the choke operates in the critical regime (like in the figure below).
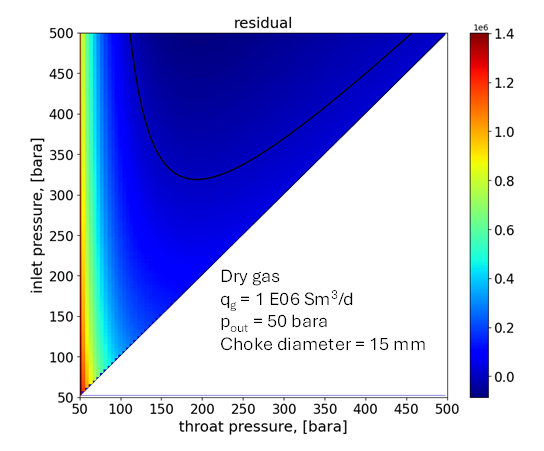
Recommended Practice for BHP Calculations
When estimating BHP, always aim to use the shortest and most reliable pressure path. If there is a wellhead choke, but measured tubing head pressure or casing head pressure is available and considered reliable, it is generally best to ignore the wellhead choke and calculate BHP directly from this surface pressure. Doing so minimizes assumptions, simplifies the pressure path, and improves accuracy.
Preferred Calculation Path:
- Tubing/casing head pressure → tubing/casing pressure drop → bottomhole pressure
This direct approach is preferable to the more assumption-heavy path that includes a wellhead choke:
- Line pressure → wellhead choke pressure drop → tubing/casing head pressure → tubing/casing pressure drop → bottomhole pressure
This distinction is especially important when high-confidence surface pressure data is available — performing wellhead choke calculations in such cases may unnecessarily introduce uncertainty.
When Downhole Gauge Data Available
If a downhole pressure gauge is available, it is best to use that data directly for BHP estimation. This eliminates the need for pressure gradient assumptions and calculations entirely, resulting in the shortest and more reliable output.
When to Use Wellhead Choke-Based Calculations
- Surface pressure is unavailable or unreliable, but line pressure and flow rates are available.
- Line pressure and surface pressure are available, but flow rates are unavailable or unreliable (an iterative approach will be used to adjust rates until the calculated surface pressure matches the measured value)
- Simulating or designing choke strategies for operational optimization, such as evaluating pressure response or production control, erosion mitigation, etc
3.10. Vertical Flow Performance (VFP) Export
VFP tables are used to model the well's VFP under a range of flowing conditions, without requiring BHP to be recalculated for every individual parameter set. Instead, simulators can interpolate the parameters based on defined combinations of key input variables.
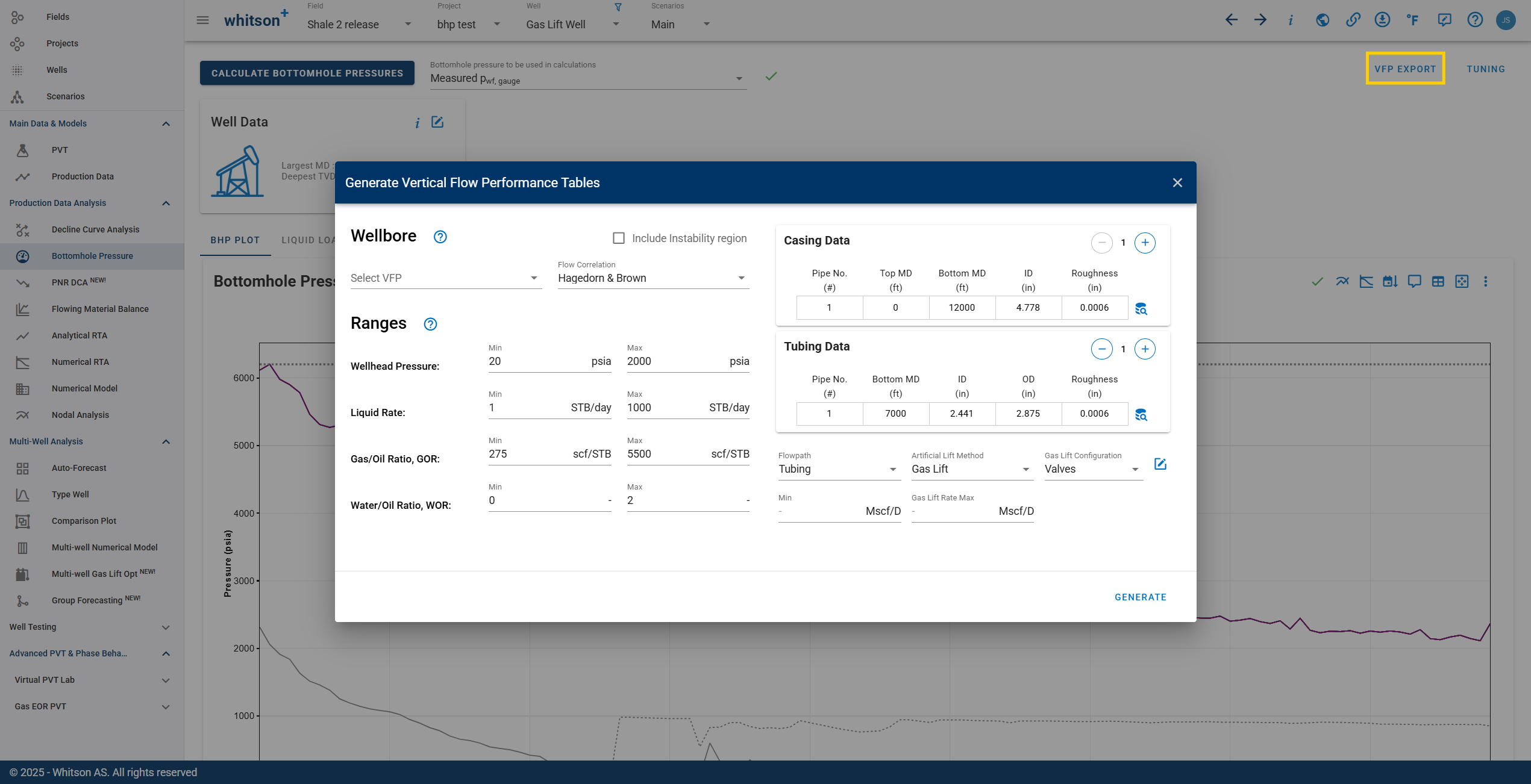
The VFP Export feature in whitson+ generates a sensitivity-based table in ECLIPSE-compatible format, allowing users to import it directly into their software.
To generate the VFP sensitivity table, the user must specify:
-
Well configuration (tubing, deviation, depth, etc.).
-
Surface pressure, liquid rate, GOR and WOR limits.
-
BHP Flow Correlation.
File Output
Once the necessary inputs are provided, the export will generate a file with structured combinations of the input parameters. A preview of the output format is shown below:
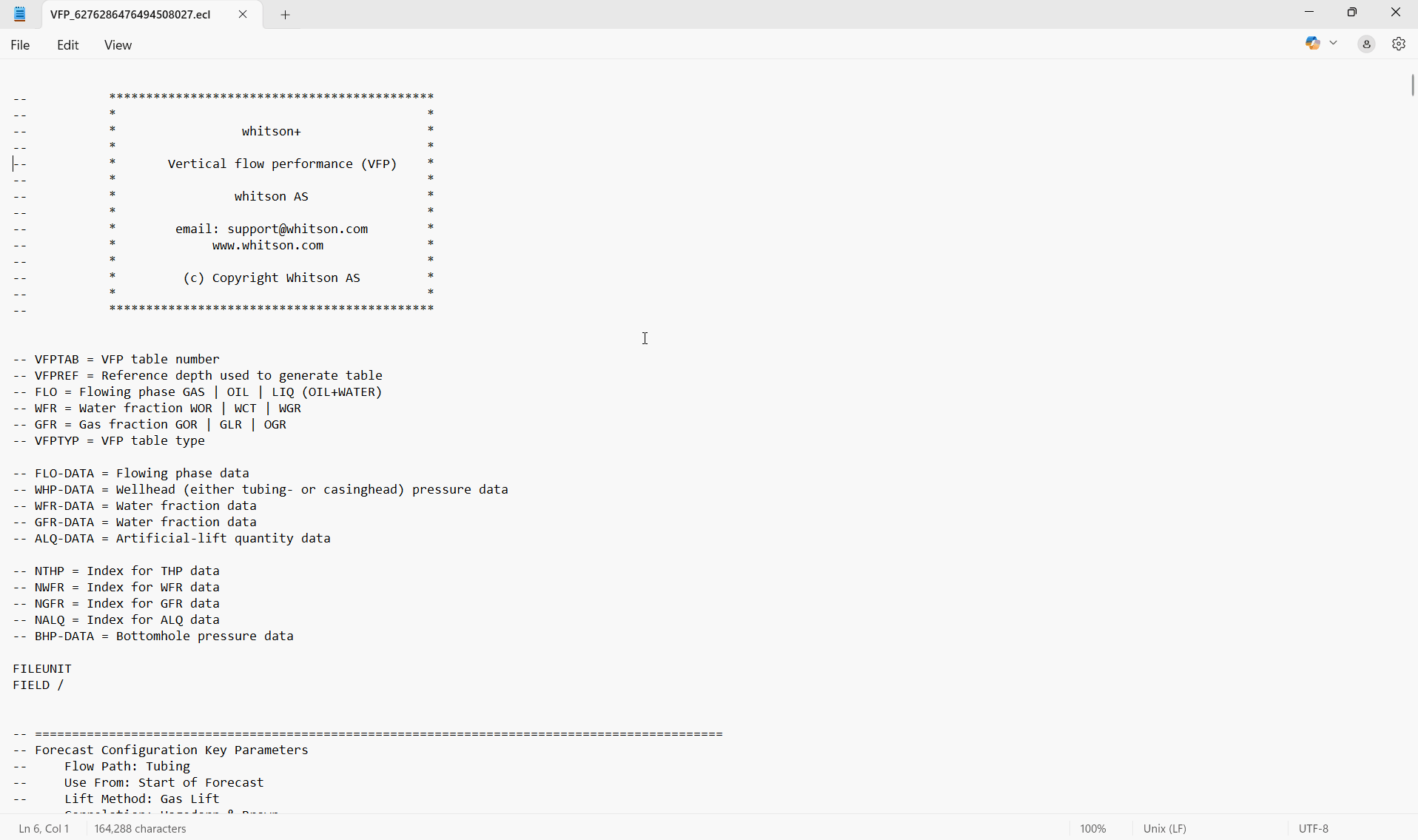
By default, the generated table includes:
- 25 points for flow rates
- 10 points for wellhead pressure
- 5 points for WOR/WGR
- 8 points for GOR/CGR
- 3 points for gas lift injection rate (if applicable).
All points are linearly spaced within the defined minimum and maximum range. The final VFP table includes all valid combinations (sensitivity mix) across the defined ranges.
VFP Export Output
- The VFP table format is compatible with ECLIPSE simulators only.
- Each table is well-specific and sensitive to the wellbore design, trajectory, artificial lift, and fluid properties.