Multi-well Numerical Model
This module closely mirrors the single-well numerical model module, essentially adhering to the same fundamental principles. The primary distinction lies in its capacity to enable users to incorporate either a single well or multiple well within a single numerical model.
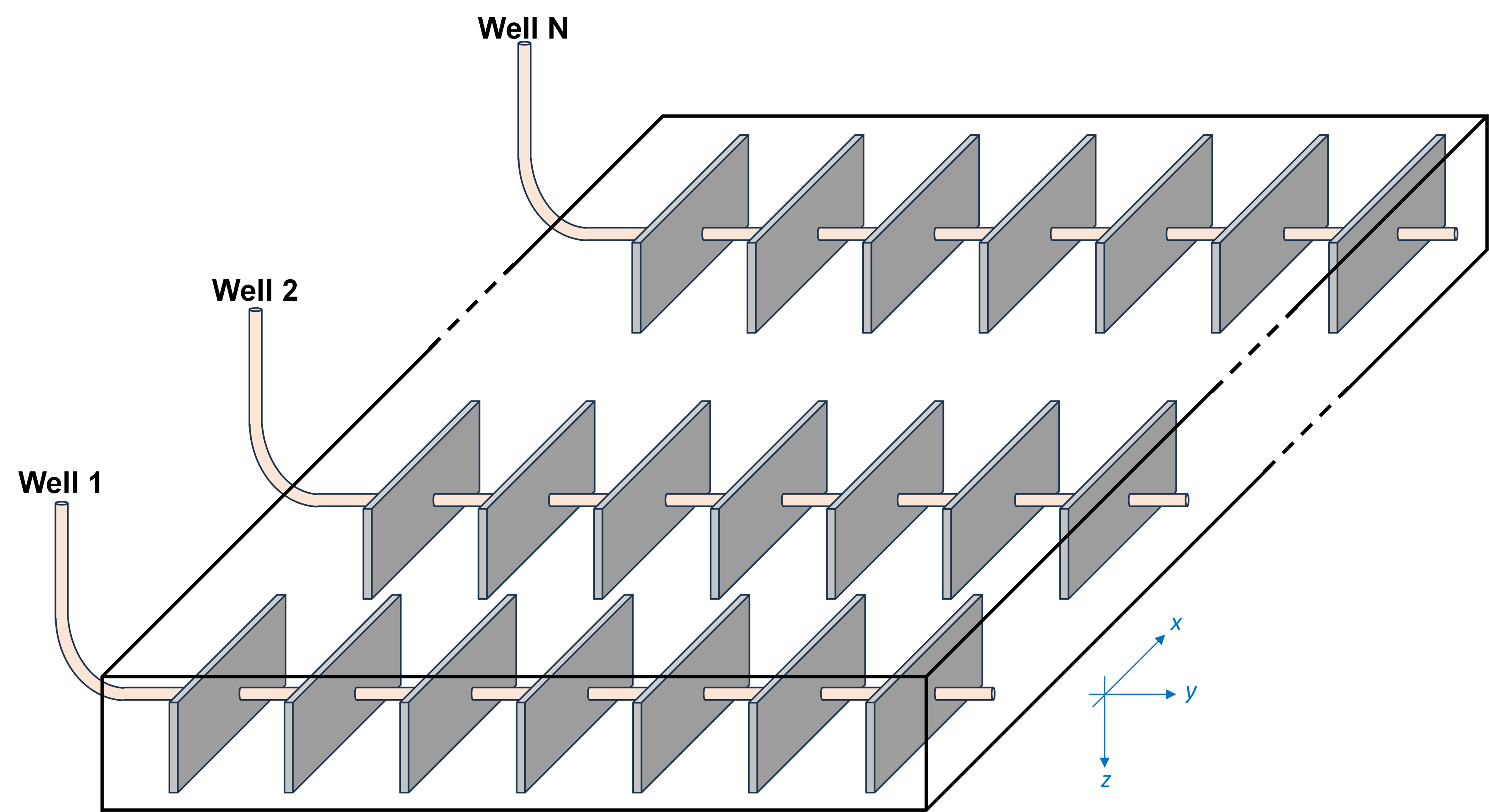
Fig. 1: Multi-well Model
1. Assumptions
1.1 Model Design
1.1.1 Symmetry element
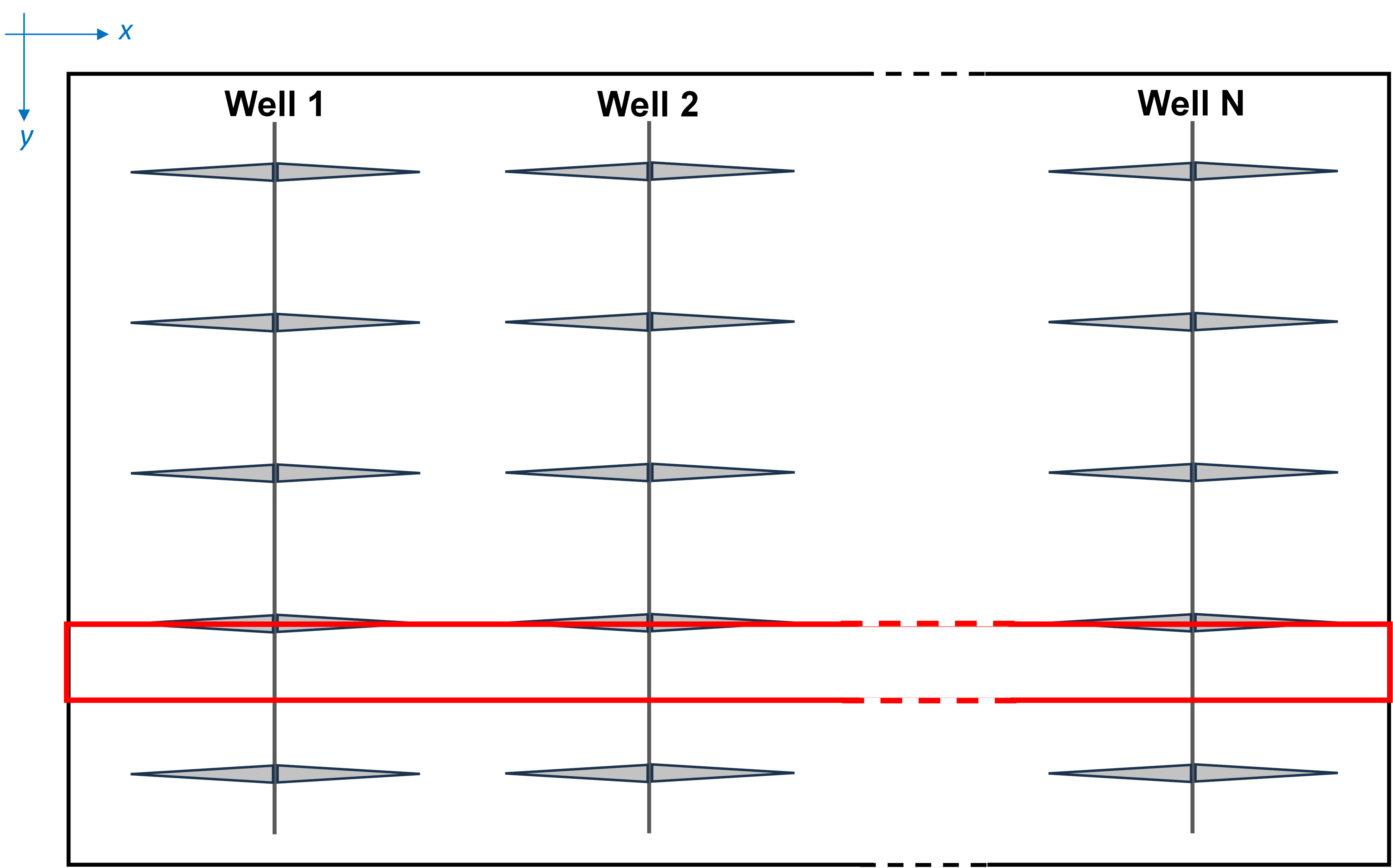
Fig. 2: Birds Eye View
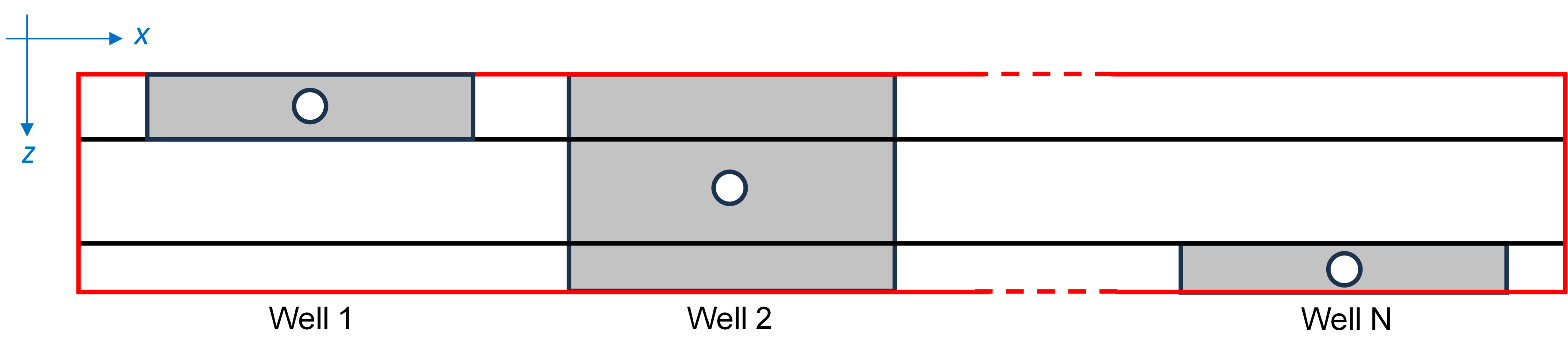
Fig. 3: Gun Barrel View
In accordance with the symmetry element approach, it is assumed that all wells within the model have the same number of fractures. This assumption makes it possible to model a half-fracture for all wells as illustrated in Fig. 2 and Fig. 3. The scaling factor will subsequently be employed to adjust the production performances as defined below
1.1.2 Fracture half-length
Each individual well can have different fracture half-lengths \(\left(x_f\right)\) and heights \(\left(h_f\right)\). The software allows user to have overlapping fractures in the same or different layer between adjacent wells as shown in Fig.4.
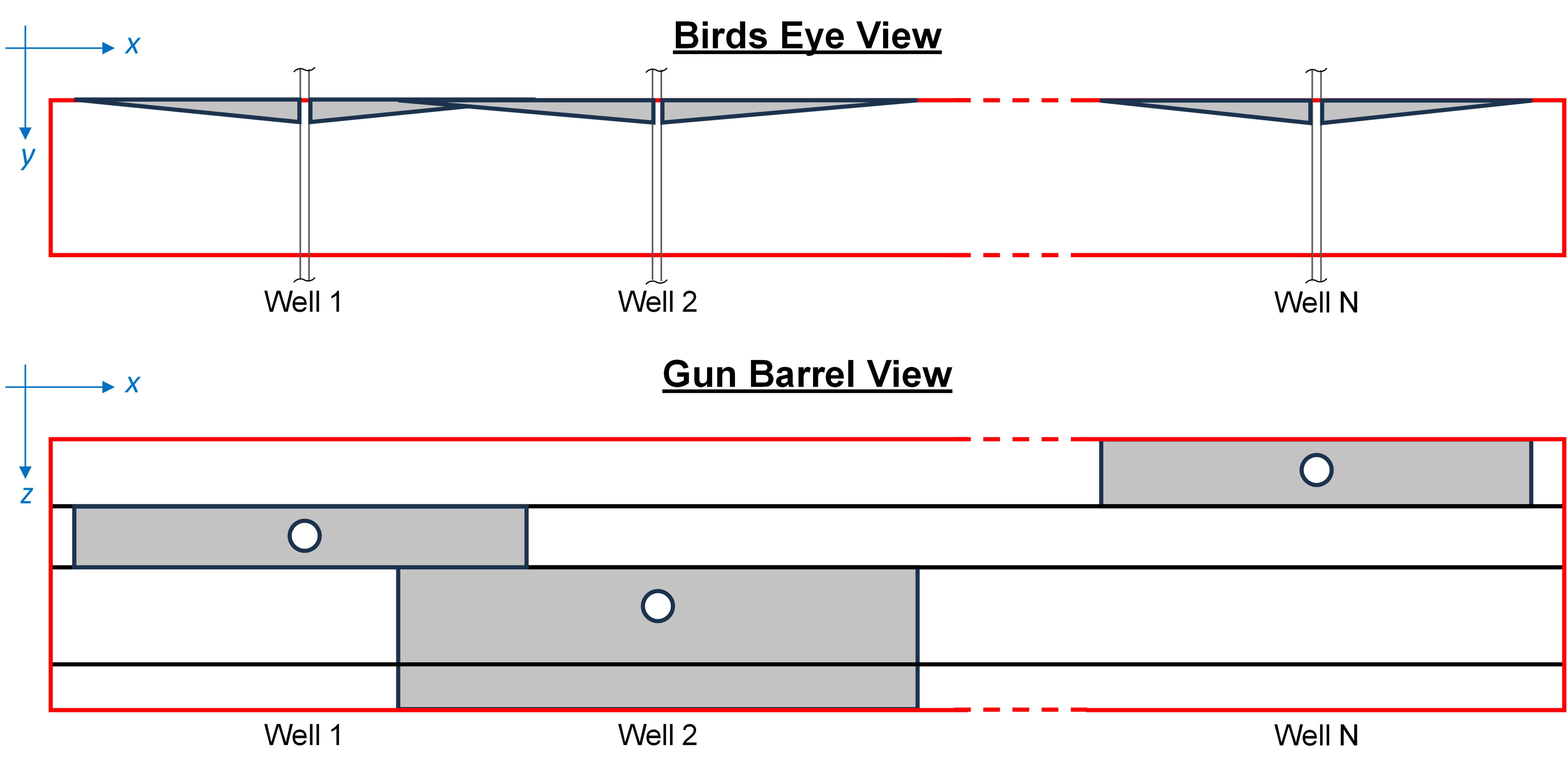
Fig. 4: Overlapping Fractures
1.1.3 Enhanced Fracture Region (EFR) Option
This option is not supported by the current version of multi-well numerical model.
1.1.4 Gridding
The numerical model utilizes logarithmic gridding for the matrix area between hydraulic fractures within the same well, i.e. along y-axis, while maintaining a uniform grid pattern along the x-axis, as visually depicted in Fig.5.
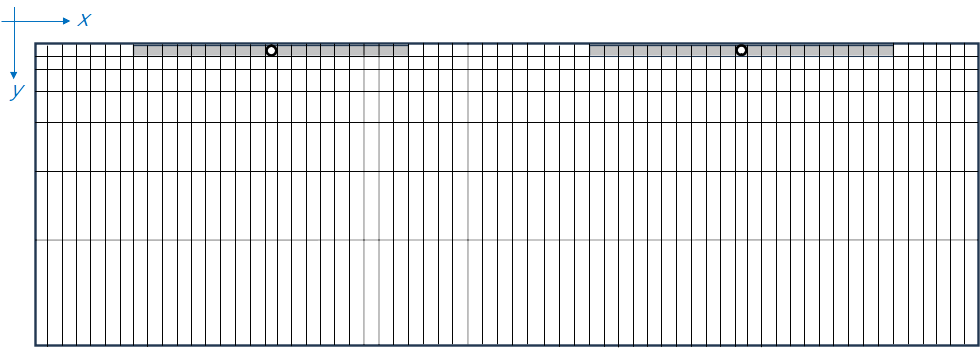
Fig. 5: Gridding of Numerical Model
The number of grid blocks is determined the same manner to that of the single-well numerical model. Here, users are provided with five levels of grid refinement: very low, low, medium, high and very high. Very High option is best capturing the details but compromised by expensive simulation run time. Conversely, selecting Very Low option yields the shortest simulation run time but may potentially lose some detail in the simulation outcomes.
1.1.5 LFP and OOIP calculation
The LFP is calculated for each well separately and the OOIP is calculated for the entire multi-well model as a whole, similar to the single well numerical models, like so -
where, in multi-well, multilayer models like this,
For LFP calculations:
Nf = Number of fractures, set to be the same for all wells.
xf = Individual well fracture half-length, as entered.
hf = Total height of all layers that the fracture extends into, from the layering in Reservoir Data input card.
k = For wells fractured into a single layer, the layer permeability as entered for that layer. For wells fractured into multiple layers, the height-averaged permeability is used for all the layers included in 'Fractured Layers' column.
Here's an example worksheet to demonstrate LFP calculations for different cases - single well, multi-well and multi-layer numerical models in whitson+.
For OOIP calculations:
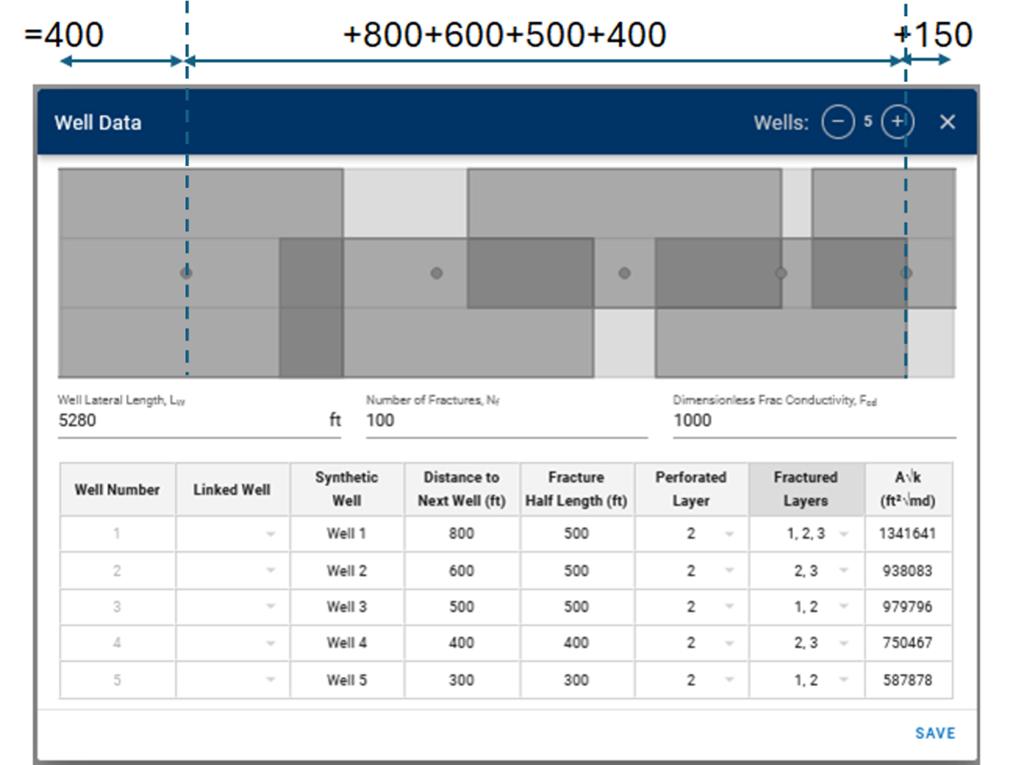
Fig. 6: Illustration of how the xe is calculated for multi-well numerical models
xe = cumulative sum of distances to next well + edge distances on either side as illustrated in this example above.
L = Lateral length, set to be the same for all wells.
hf = Total height of all layers, from the layering in Reservoir Data input card.
Φ = height averaged net porosity, from the layering in Reservoir Data input card.
Swi, Bti = from the selected well PVT in the Fluid Initialization card.
2. Input
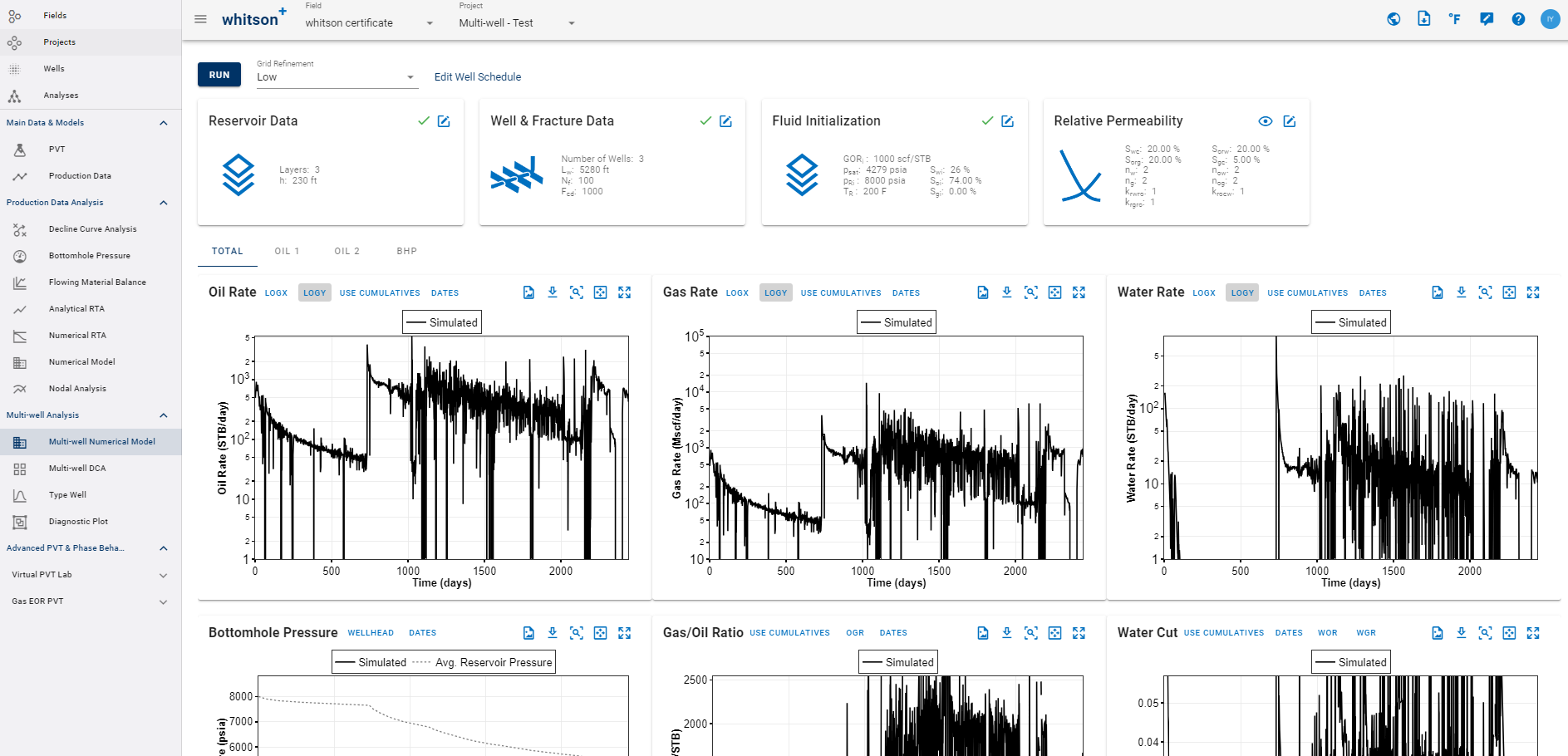
Fig. 7: Multi-well Numerical Model in whitson+
2.1 Reservoir Data
Reservoir height \(\left(h_f\right)\), matrix permeability \(\left(k_m\right)\), matrix porosity \(\left(\phi_m\right)\), rock compressibility \(\left(c_r\right)\), fracture \(\left(\gamma_f\right)\) and matrix gamma \(\left(\gamma_m\right)\) are entered through this data card. The model can be configured as a single- or multi-layer system as depicted in Fig. 7.
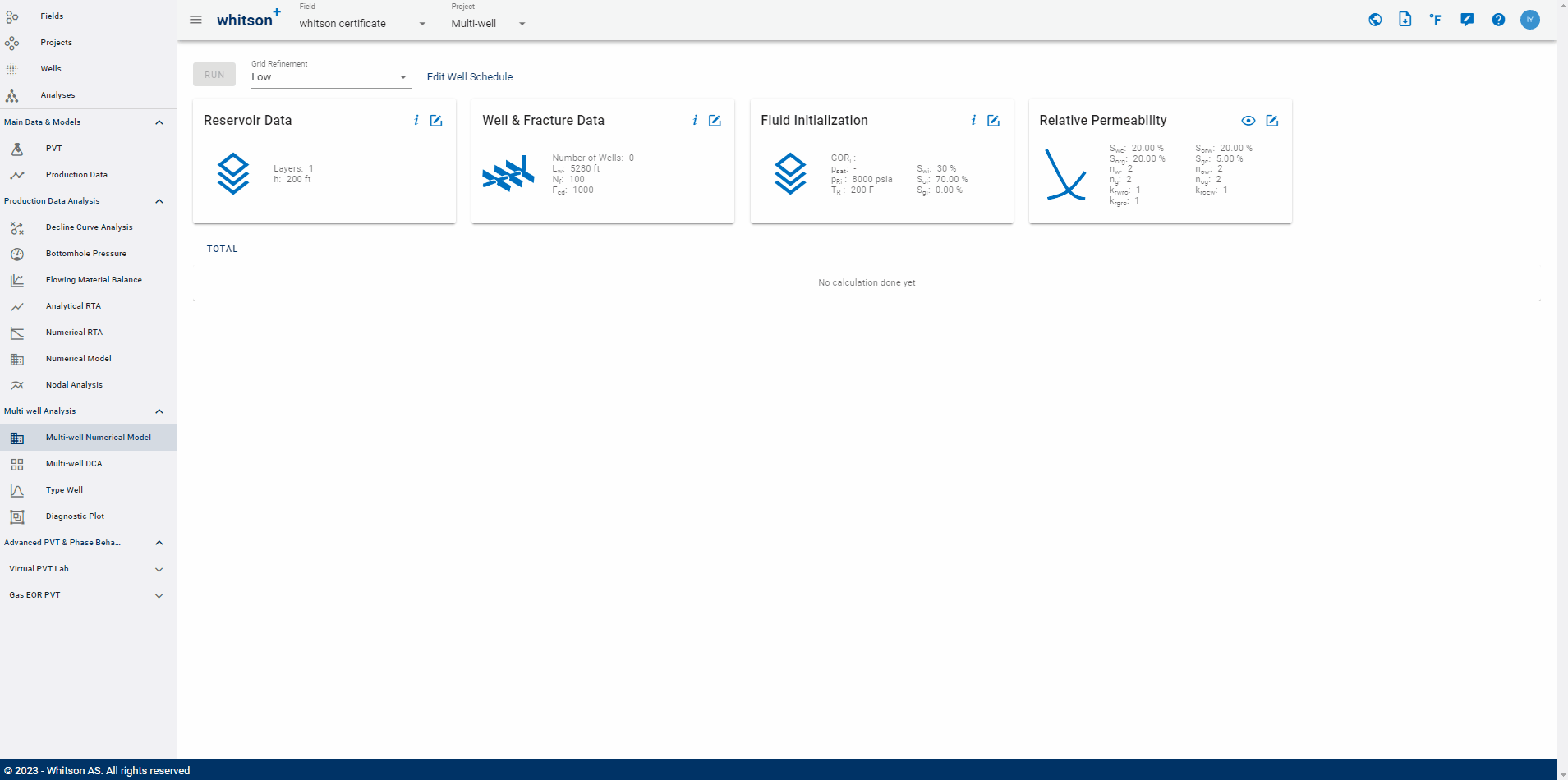
Fig. 8: Reservoir Data Input
2.2 Well & Fracture Data
This data card allows user to input all properties related to well and fractures. Well lateral length \(\left(L_w\right)\), number of fractures \(\left(N_f\right)\), and dimensionless fracture conductivity \(\left(F_{cd}\right)\) are properties applicable to all wells. Properties for each well includes:
- Linked Well: to honor historical data associated with a specific well within the project.
- Synthetic Well: to create a synthetic well. This designated well name serves a role for plotting and visualization purposes.
- Distance to Next Well (ft): well spacing between two individual wells.
- Fracture Half Length (ft): presumed to be uniform for both left and right \(x_f\).
- Perforated Layer: landed layer.
- Fractured Layers: may span across multiple layers.
- \(A\sqrt{k}\): automatically calculated by the software.
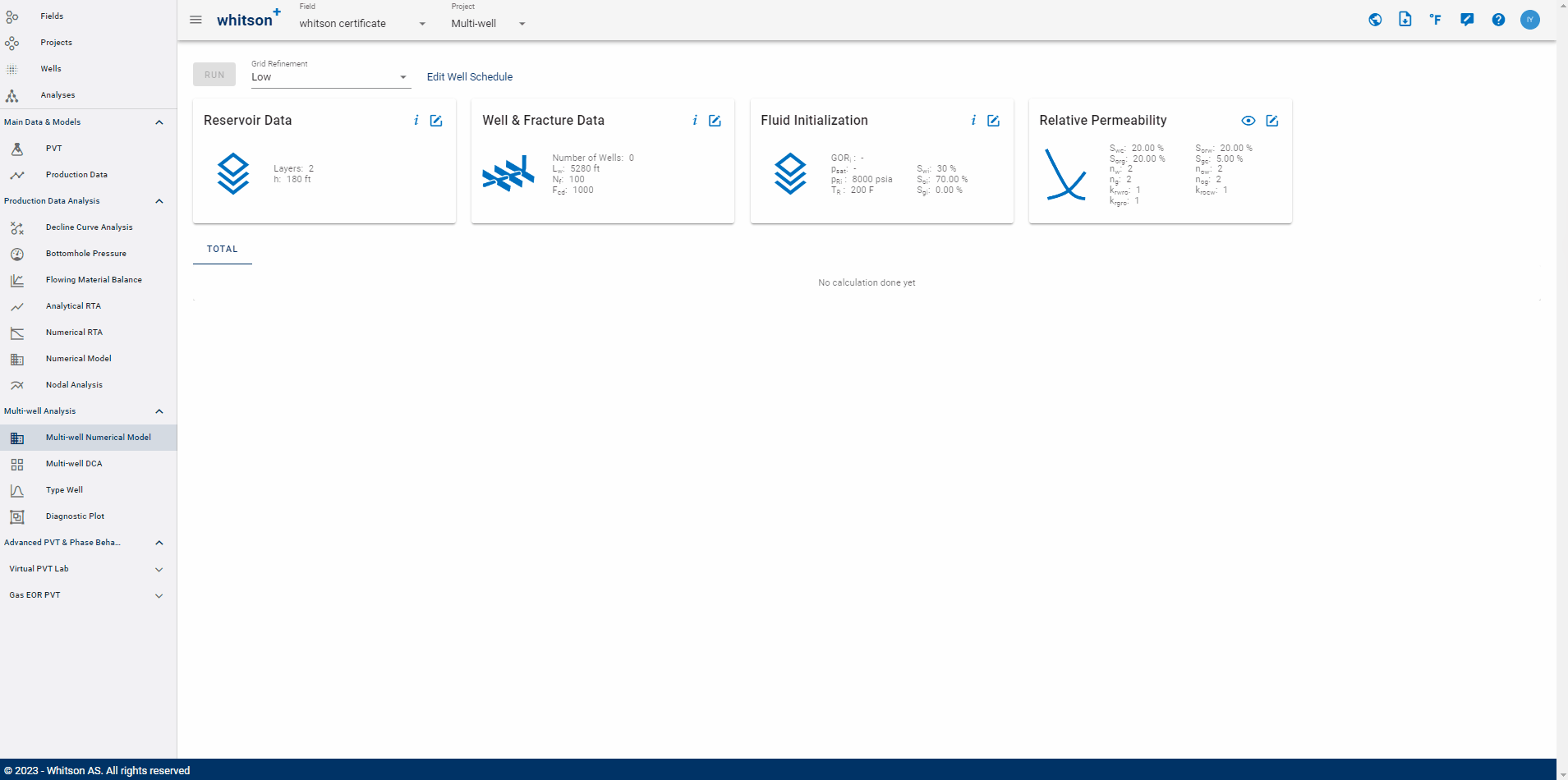
Fig. 9: Well & Fracture Data Input
2.3 Fluid Initialization
This feature offers both single and multi-layer fluid initialization options, seamlessly integrated with PVT characteristics of a designated well. The requirement is to input initial GOR \(\left(R_{ti}\right)\), initial water saturation \(\left(S_{wi}\right)\) and initial reservoir pressure \(\left(p_i\right)\). While for initial solution GOR \(\left(R_s\right)\), initial solution CGR \(\left(r_s\right)\), oil \(\left(S_o\right)\) and gas saturation \(\left(S_g\right)\), and saturation pressure \(\left(p_{sat}\right)\) are calculated by incorporating black oil table and initial GOR, ensuring accuracy and reliability in the modelling process.
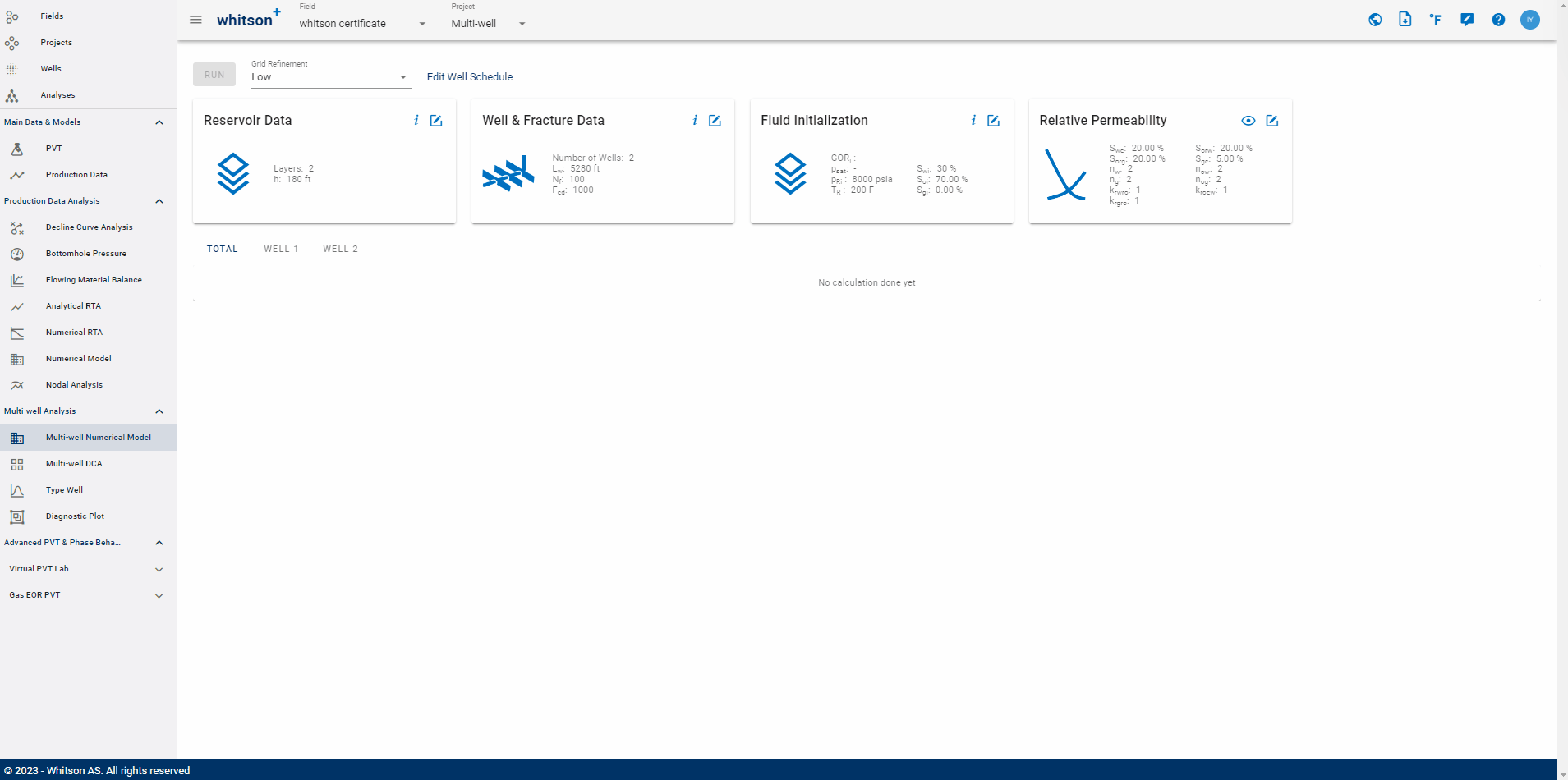
Fig. 10: Fluid Initialization Input
2.4 Relative Permeability
The numerical model incorporates a single set of matrix and fracture permeability.
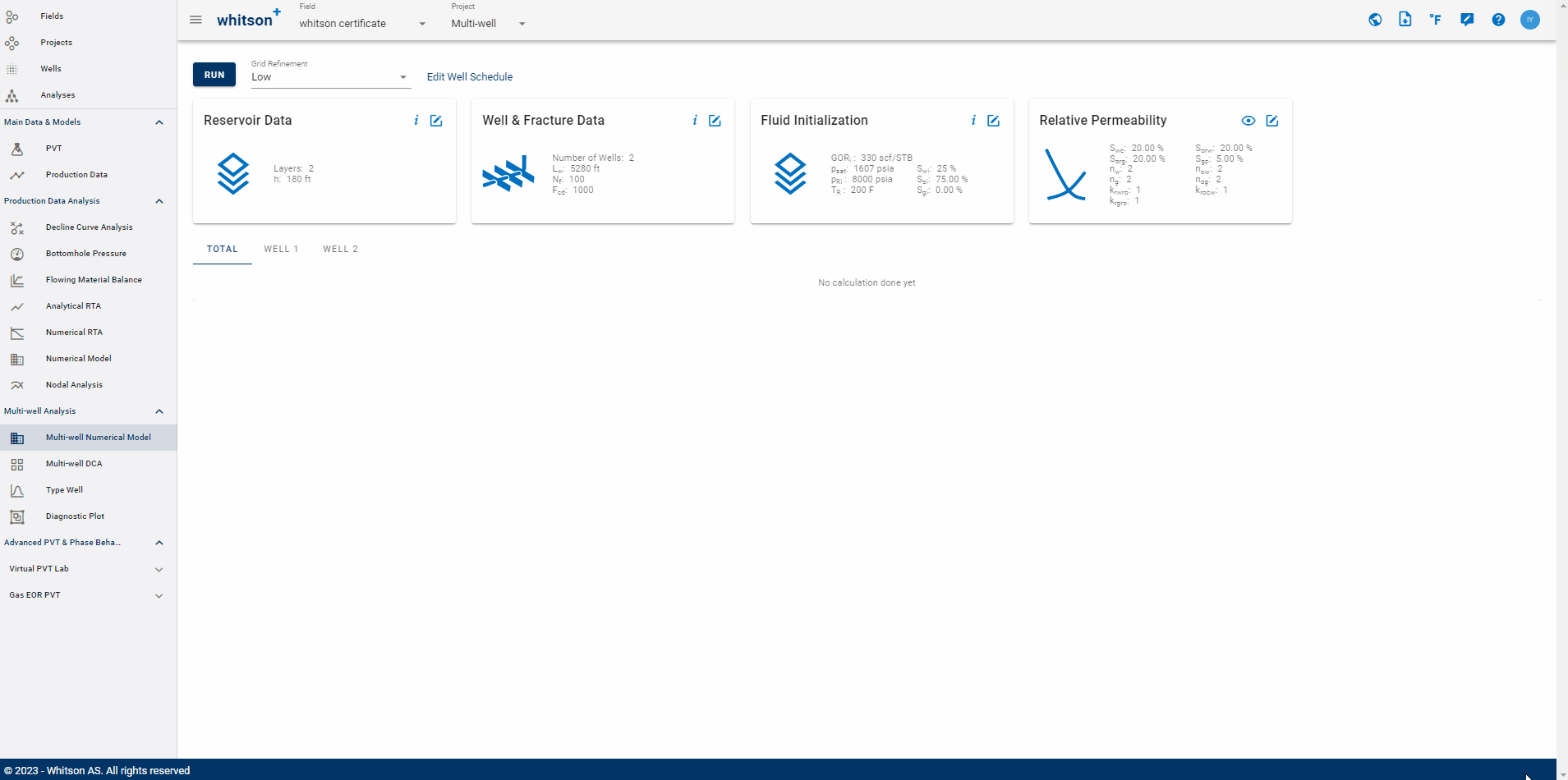
Fig. 11: Relative Permeability Input
2.5 Well Schedule
There are six well control options:
- Oil
- Gas
- Water
- Liquid
- BHP
- BHP (synthetic)
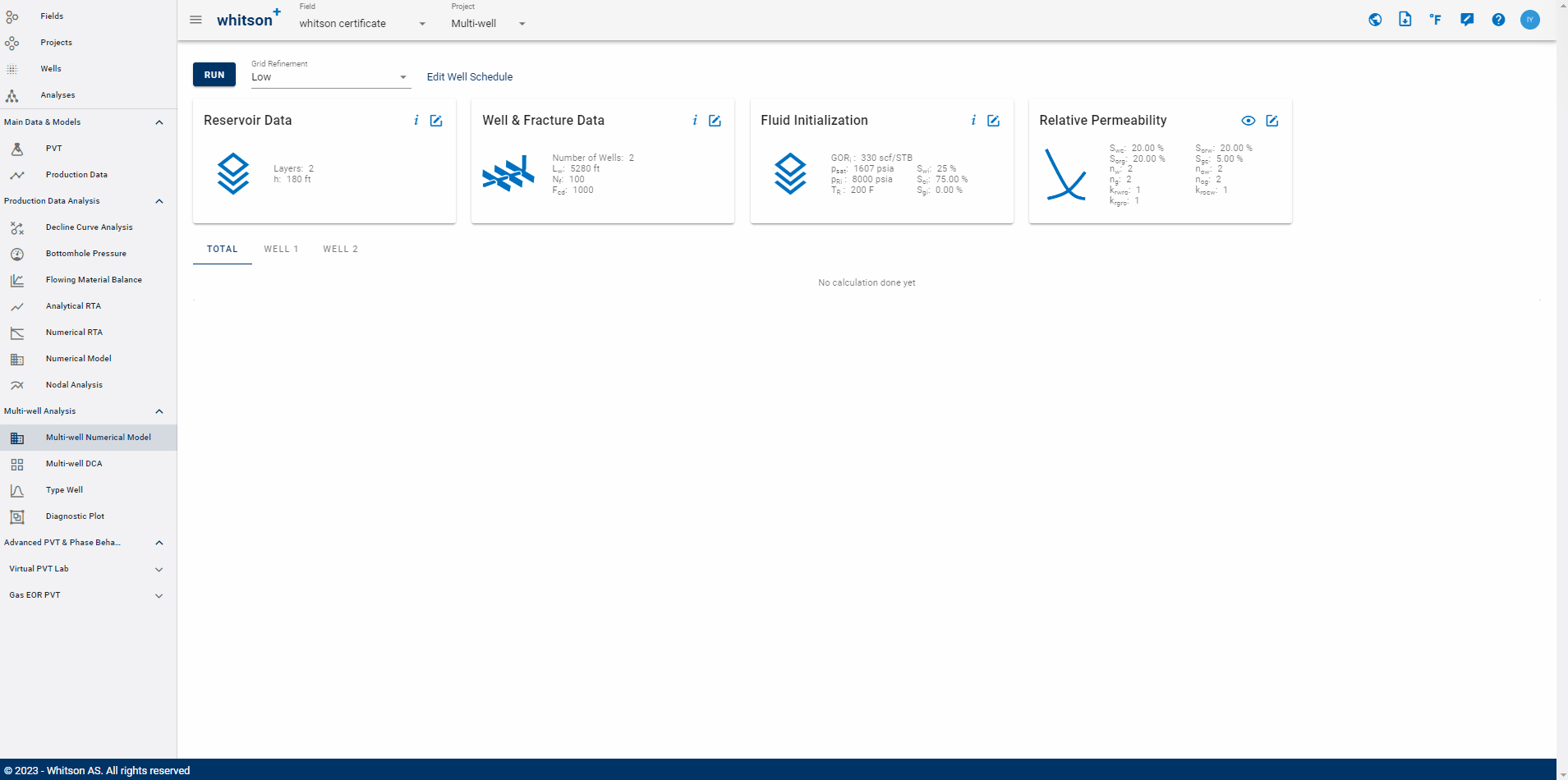
Fig. 12: Well Schedule Input
2.6 Case Examples
Below are three case examples that demonstrate how to configure and run the model in whitson+:
- Case 1 - Linked Wells: Model three SPE Data Repository wells and use production data as well schedule control.
- Case 2 - Synthetic Wells: Model two synthetic wells.
- Case 3 - Combination: Model two SPE Data Repository wells and a synthetic well.
2.6.1 Case 1 - Linked Wells
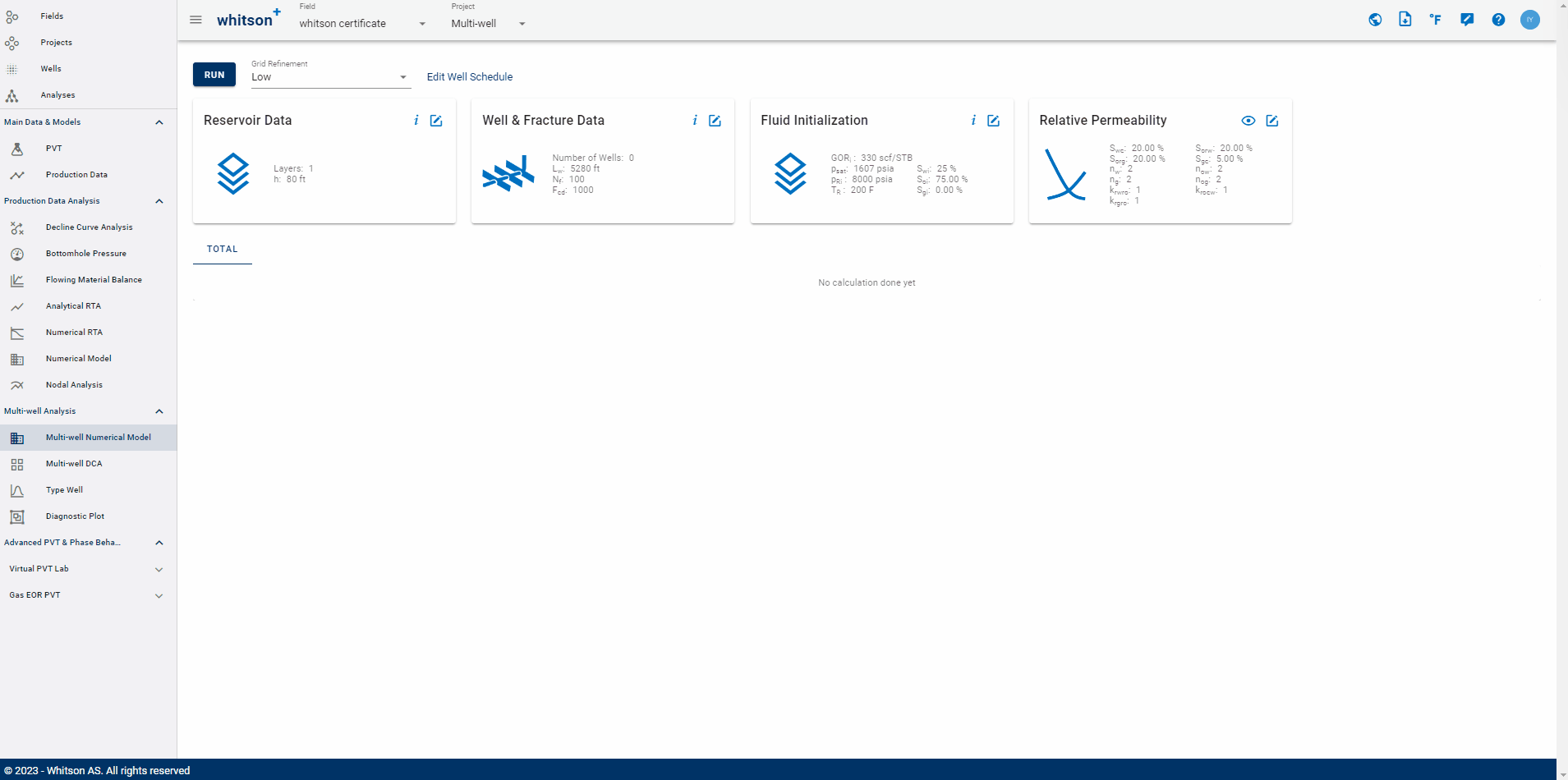
Fig. 13: Example Case 1
2.6.2 Case 2 - Synthetic Wells
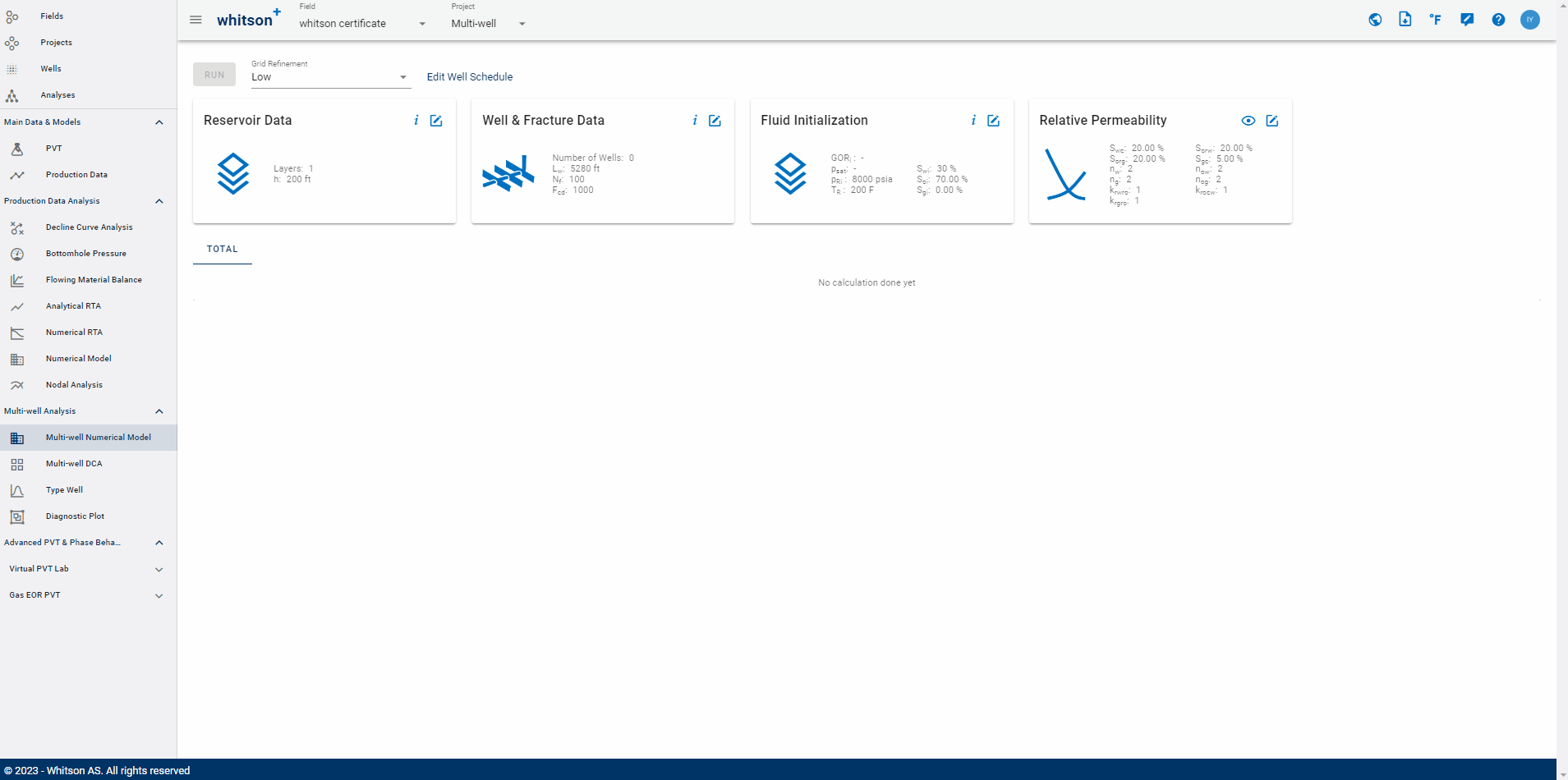
Fig. 14: Example Case 2
2.6.3 Case 3 - Combination
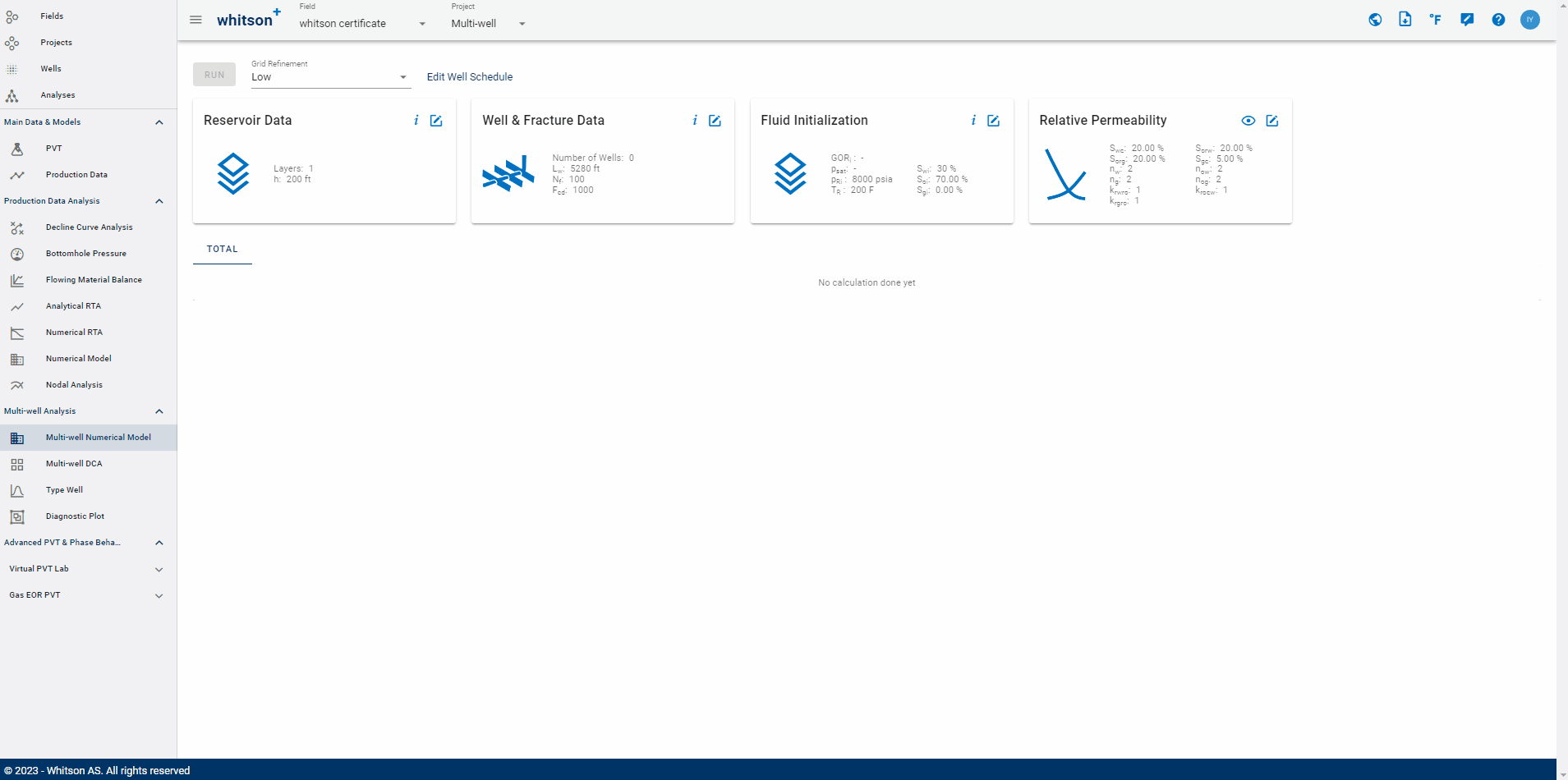
Fig. 15: Example Case 3